Part Accuracy Characteristics
A distinct difference exists between part accuracy and the accuracy in which a machine can move.
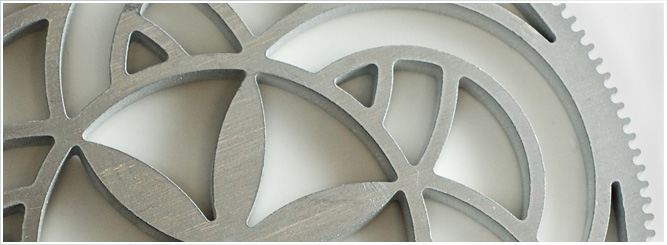
Simply buying a 0.00000000000001″ accurate machine, with perfect dynamic motion, perfect velocity control, and dead-on repeatability does not mean you will cut perfect parts.
It, however, means you will spend a lot of money on the super-accurate machine. Finished part accuracy is a combination of process error (the waterjet) + machine error (the XY performance) + workpiece stability (fixturing, flatness, stable with temperature).
The section below describes part errors that would occur even if the waterjet machine was perfect. The waterjet beam has characteristics that greatly affect part accuracy. Controlling these characteristics has been the focus of waterjet suppliers for many years.
Simply put, a highly accurate and repeatable machine may eliminate machine motion from your part accuracy equation, but it does not eliminate other part errors (such as fixturing errors and inherent waterjet stream errors).
When cutting materials under 1 inch thick, a conventional waterjet machine typically cuts parts from +/-0.003 to +/-0.015 inch (.07 to .4 mm) in accuracy. A machine equipped with Dynamic Waterjet can cut parts as accurately as +/- 0.001 inches.
For materials over 1 inch thick the machines will produce parts from +/- 0.005 to 0.100 inches (.12 to 2.5 mm). A high-performance XY table is designed to have an accuracy of about 0.005-inch linear positional accuracy or better.
So where do the part inaccuracies come from?
Beam Deflection or “Stream Lag”
When the waterjet, or other beam-type cutters like laser or plasma, are cutting through the material, the stream will deflect backward (opposite direction of travel) when cutting power begins to drop. This problem causes: increased taper, inside corner problems, and sweeping out of arcs.
Reduce this lag error by increasing cutting power or slowing down the cut speed.
Increased Taper
A “V” shaped taper is created when cutting at high speeds. The taper can be minimized or eliminated by slowing down the cut path or increasing cutting power.
Inside Corner Problems
When cutting an inside corner at high speed, the stream can dig into the part as it comes out of the corner.
Sweeping Out of Arcs
When cutting at high speed around an arc or circle the stream lag sweeps out a cone.
Fixturing
Even though the waterjet delivers under ½ pound of vertical force when cutting a high-quality part and under 5 pounds when rough cutting, proper fixturing is required to produce accurate parts.
The part must not move during cutting or piercing, and it must not vibrate. To minimize these errors, try to butt the workpiece up against the edge of the catcher or a solid bar stop secured to the table slats. Look for material vibration or movement during cutting the first article.
Material Instability
Some materials, like plastics, can be very sensitive to temperature changes. Called thermal expansion, these materials may expand when slightly heated or shrink when cooled. During waterjet cutting the material does not get hot, but it can get warm.
Also, be especially careful of air gaps in cast material, as the stream tends to open up in air gaps.
The AWJ will not induce warpage in sheet material. It will, however, relieve stress. If you are working with a sheared material <0.125 inches thick and you start your cut path off the part, enter into the part, and then cut the part, you may see the material twist and warp. Avoid this warpage whenever possible by beginning cut paths from within the material (pierce a hole and begin cutting) as opposed to beginning from outside of the material.
Pump Issues
Beyond the obvious pump issues such as ensuring that the pump is delivering water at the set pressure, other issues can also impact part accuracy. If the pump has 2 or more intensifiers, do the intensifiers always stroke at the same time? If so, then look on the part for vertical marks on the cut edge that matches in frequency with the stroking.
Check valves should be in good working order.
Water Pressure at the Nozzle
Cut speed can be lost if excessive pressure drops (greater than 2,500 psi) exist in the high-pressure plumbing run from pump to head.
Ensure the in-line filter, usually located near the cutting head, is free of excessive buildup.
If you have made any changes to the plumbing run (changed the route, replaced a large line with a smaller replacement line, etc.) then ensure that you have not created larger pressure drops. Any loss of pressure between the pump is to be minimized. Pressure is cut speed, cut speed is money.
Cutter Comp Error
Cutter compensation is the value entered into the control system that takes into account the width of the cut of the jet; in effect, you are setting the amount by which you are enlarging the cut path so that the final part comes out to proper size.
Before you perform any high-precision work where finished part tolerances are better than +/- 0.005 inches, cut a test coupon and ensure you have properly set the cutter compensation. Many a good drawing has been cut wrong because the operator did not take the time to establish the best cutter compensation value.
Programming Error
Often the most difficult of all part accuracy errors to find is a programming error where the dimension of the part program does not perfectly match the dimension of the original CAD or hand-drawn drawing.
Part programs that appear graphically on the screen of an XY control typically do not display dimensions. Therefore, this error can go undetected. When all else fails, double-check that the dimensions on the part program match exactly those of the original drawing.
Abrasive Mesh Size
Typical abrasive mesh sizes are 120, 80, and 50 (similar to sandpaper you might use for woodworking). The different mesh sizes do not have a significant impact on part accuracy. They have a greater impact on surface finish and overall cut speed. Finer abrasives (larger mesh number) produce slower cuts and smoother surfaces.
Machine Motion
The positional accuracy and dynamic motion characteristics of a machine have an impact on the part accuracy. There are many aspects to machine motion performance. A few are:
Backlash in the mechanical unit (changes in direction, is there slop in the gears or screw when the motor changes from clockwise to counterclockwise?), repeatability, will the machine come back close to the same point over and over? Servo tuning is important. Improper tuning will cause backlash, squareness, repeatability errors, and can cause the machine to chatter (wiggle at high frequency) when moving.
Position accuracy is important, as well as straightness, flatness, and parallelism of the linear rails. A small part, under 12 inches in length and width, does not demand as much from the XY table as larger parts.
A large part measuring, for example, 4×4 ft, will be greatly impacted by machine performance. A small part will not see position accuracy, or rail straightness as a major impact on finished part tolerance simply because the small part masks machine errors. Large parts expose such errors more evidently.
Remember that a machine motion characteristic does not directly correspond to finished part tolerance. An expensive super-precision machine (linear position accuracy of, for example, +/- 0.001″ over full travel, will not automatically generate a finished part of +/- 0.001″ other part accuracy factors are still there (see above).