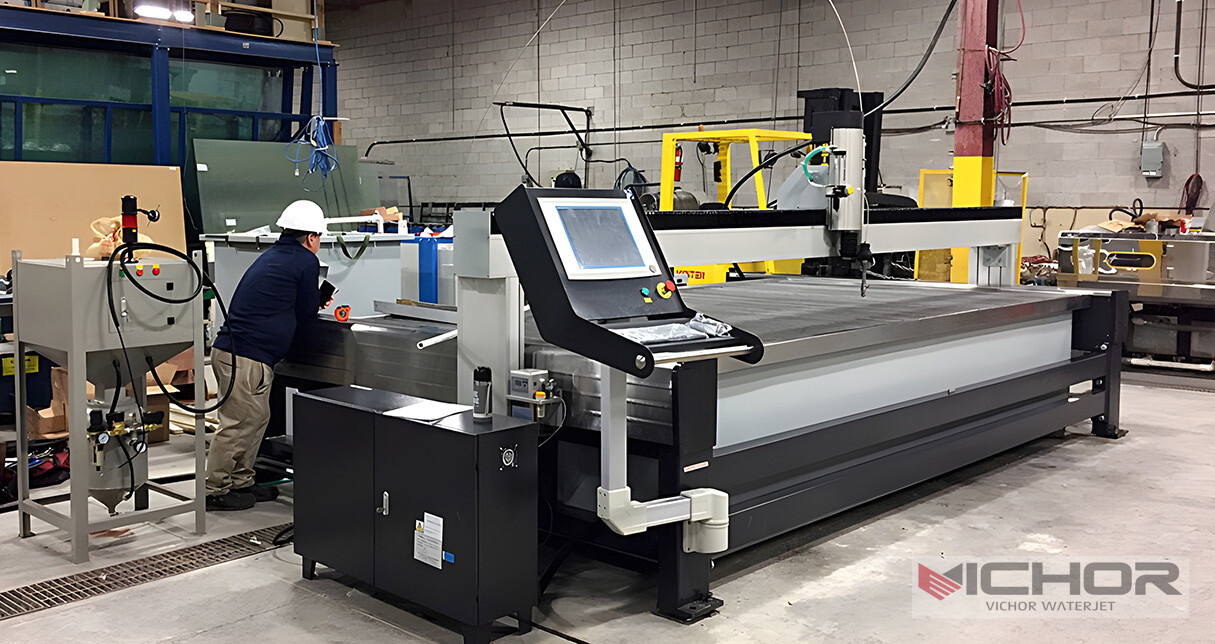
Water Jet Glass Cutting Service: Unlocking Precision, Versatility & Complex Designs in Glass
Glass, with its unique blend of transparency, strength, and aesthetic appeal, is a fundamental material in modern design and construction. Cutting it precisely, especially for complex shapes or delicate applications, has historically presented challenges. Traditional methods like scoring and breaking or sawing often lead to chipping, micro-fractures, limitations in design complexity, and significant material waste. Enter the transformative water jet glass cutting service. This advanced technology harnesses the power of ultra-high-pressure water, often mixed with abrasive garnet, to cut through glass with unparalleled accuracy and minimal thermal or mechanical stress. This article delves deep into the world of water jet glass cutting service, exploring its core principles, advantages, applications, and why it has become the preferred choice for industries demanding perfection in glass cutting.
What is a Water Jet Glass Cutting Service?
A water jet glass cutting service utilizes specialized computer-controlled machinery. At its heart is a high-pressure pump intensifier that pressurizes water to levels exceeding 60,000 PSI (often reaching 90,000 PSI). This ultra-high-pressure stream is then focused through a tiny gemstone orifice (like diamond or sapphire), creating a supersonic jet. For cutting hard materials like glass, a precisely metered stream of abrasive garnet sand is introduced into this water stream within a mixing tube. The abrasive particles, accelerated by the water, perform the actual erosive cutting action. The entire process is guided by sophisticated CAD/CAM software, translating intricate digital designs into precise cutting paths executed by the machine. The result is a water jet glass cutting service capable of handling projects impossible or impractical with other methods.
The Unmatched Advantages of Water Jet Glass Cutting
Precision and Intricate Detail: Beyond the Limits of Conventional Cutting
This is where a water jet glass cutting service truly shines. The narrow kerf (cutting width) of the abrasive waterjet stream, typically ranging from 0.020″ to 0.050″ (0.5mm to 1.3mm), allows for exceptional precision and the creation of incredibly intricate details. Sharp inside corners, complex curves, fine lettering, and intricate patterns are all achievable with minimal limitations. Tolerances of +/- 0.005″ (0.13mm) or better are common, ensuring parts fit together perfectly in assemblies or match design specifications exactly. Whether it’s replicating a complex architectural motif, cutting precise holes for hardware in shower enclosures, or creating delicate art pieces, the accuracy offered by a professional water jet glass cutting service is unparalleled. The CNC control guarantees repeatability, making it ideal for both one-off custom projects and batch production.
Material Versatility: Handling More Than Just Standard Glass
While excelling with standard annealed glass, a water jet glass cutting service offers remarkable versatility across a wide spectrum of glass types and thicknesses. This includes:
Tempered Glass (Pre-cut): Waterjet cuts tempered glass before the tempering process. The service precisely cuts the annealed glass to the final shape, including holes and notches, which is then sent for tempering. Trying to cut tempered glass post-temper would cause it to shatter.
Laminated Glass: Can be cleanly cut through all layers simultaneously, including the PVB interlayer, maintaining the integrity of the laminate without delamination at the edges.
Insulated Glass Units (IGUs – Pre-assembly): Individual glass panes for IGUs are cut to exact size and shape, including any necessary holes for hardware, before assembly into the sealed unit.
Patterned/Textured Glass: Handles the uneven surfaces effectively.
Low-Iron (Optically Clear) Glass: Cut without compromising its clarity or introducing optical distortions.
Chemically Strengthened Glass: Cut precisely before or after strengthening (depending on the specific glass type and requirements).
Thick Glass: Capable of cutting glass several inches thick, a feat difficult or impossible for many other methods.
This versatility makes a water jet glass cutting service a single-source solution for diverse projects involving different glass specifications.
Edge Quality and Minimal Stress: The Cold Cutting Advantage
Perhaps the most significant technical advantage of a water jet glass cutting service is its status as a cold cutting process. Unlike laser cutting (which generates intense localized heat) or traditional mechanical methods (which impart significant shock and pressure), waterjet cutting uses no heat and minimal mechanical force. This has profound benefits for glass:
No Heat-Affected Zone (HAZ): Eliminates the risk of thermal stress, micro-cracking, or changes in the material’s properties near the cut edge. Glass retains its full strength.
Smooth, Finished Edges: The abrasive action produces a finely satined (“matte”) edge directly from the cutting process. While not optically polished, this edge is typically very smooth, consistent, and free from the chipping, splintering, or large burrs common with sawing or scoring/breaking. This often reduces or eliminates the need for secondary edge finishing (like seaming or polishing) for many applications, saving time and cost.
No Structural Weakening: The absence of heat and shock prevents the creation of micro-fractures that can act as failure points later, ensuring the structural integrity of the glass component is maintained.
Design Freedom and Minimal Waste: Realizing Complex Visions Efficiently
The combination of precision, lack of thermal constraints, and CNC programmability grants designers and engineers unprecedented freedom. A water jet glass cutting service can effortlessly produce:
Complex geometric shapes and organic curves.
Precise internal cutouts (holes, slots, notches) without the need for starter holes in many cases (the jet can pierce the glass).
Nesting: CAD software can optimize the placement of multiple parts on a single sheet of glass, significantly reducing material waste compared to methods requiring larger borders or simpler shapes. This nesting efficiency makes a water jet glass cutting service both cost-effective and environmentally friendly by maximizing material yield.
Prototyping and Customization: Ideal for one-off pieces, custom architectural features, art installations, or rapid prototyping of new glass designs without expensive tooling.
Broad Applications Across Industries: Where Waterjet Glass Cutting Excels
The unique capabilities of a water jet glass cutting service make it indispensable across numerous sectors:
Architecture & Construction: Custom windows, skylights, complex curtain wall panels, decorative partitions, shower enclosures (precise holes for hardware), railings, signage, intricate floor inlays, stair treads.
Interior Design & Furniture: Tabletops, shelves, cabinet inserts, decorative panels, lighting fixtures, display cases, unique furniture components.
Automotive & Transportation: Windshield prototypes, specialized mirrors, instrument panel components (pre-tempering cut), decorative trim elements.
Art & Sculpture: Creating intricate glass art pieces, sculptures, awards, trophies, and decorative elements with complex shapes impossible otherwise.
Aquariums & Displays: Cutting thick panels for custom aquariums, terrariums, and museum display cases, often requiring precise holes for plumbing or fixtures.
Electronics & Appliances: Insulators, specialized viewing windows, control panels, oven doors (pre-tempering cut).
Renewable Energy: Components for solar panels or specialized glazing.
Essentially, any application demanding precision, complex shapes, high-quality edges, or the use of specialty glass types benefits significantly from utilizing a professional water jet glass cutting service.
Implementing Water Jet Glass Cutting: Key Considerations for Your Project
Successfully leveraging a water jet glass cutting service involves collaboration:
Design: Provide accurate CAD files (DXF, DWG are common). Clearly specify dimensions, tolerances, material type, thickness, and any critical edge requirements. Discuss design feasibility with the service provider early on.
Material Specification: Clearly identify the type of glass (annealed, tempered-pre, laminated, etc.), manufacturer (if known), thickness, and any special coatings (though coatings might be affected near the cut edge).
Tolerances: Understand the achievable tolerances of the water jet glass cutting service and ensure they meet your project’s needs. Be realistic about expectations on very thick glass or intricate details.
Edge Finish: While waterjet provides a smooth satin finish, specify if a polished, seamed, or other specific edge finish is required post-cutting, as this adds cost and time.
Handling & Packaging: Glass is fragile. Discuss handling procedures and packaging requirements with the service provider to ensure safe transit, especially for large or thin pieces.
Choosing the Right Water Jet Glass Cutting Service Provider
Not all waterjet shops specialize in or are equally adept at glass cutting. When selecting a water jet glass cutting service, consider:
Glass-Specific Experience: Proven track record in cutting the specific types and thicknesses of glass you require. Ask for examples or case studies.
Equipment & Technology: Modern, well-maintained machines with sufficient pressure capabilities (90,000 PSI is often preferred for glass) and precision controls. Inline abrasive metering systems ensure consistency.
Software Capabilities: Proficiency in handling complex CAD files and optimizing cutting paths/nesting for glass.
Material Handling: Proper techniques and equipment for safely moving and cutting large glass sheets.
Quality Control: Robust processes for inspecting cuts, verifying dimensions, and ensuring edge quality.
Secondary Services: Ability to provide related services like tempering, laminating, polishing, or drilling if needed (often through partners).
Communication & Customer Service: Responsive, knowledgeable staff willing to collaborate on design and feasibility.
The water jet glass cutting service represents a paradigm shift in glass fabrication. By combining unparalleled precision, the ability to handle incredibly complex designs and diverse glass types, superior edge quality through cold cutting, and significant material savings, it solves the limitations of traditional methods. Whether for ambitious architectural landmarks, high-end interior design, functional industrial components, or stunning artistic creations, waterjet technology unlocks possibilities previously deemed impractical or impossible. As demand for customization, sustainability, and high-performance materials grows, the role of the professional water jet glass cutting service becomes increasingly vital. By understanding its capabilities and partnering with experienced providers, designers, engineers, and fabricators can push the boundaries of what’s achievable with glass, transforming visionary concepts into tangible, precision-crafted reality.
continue reading