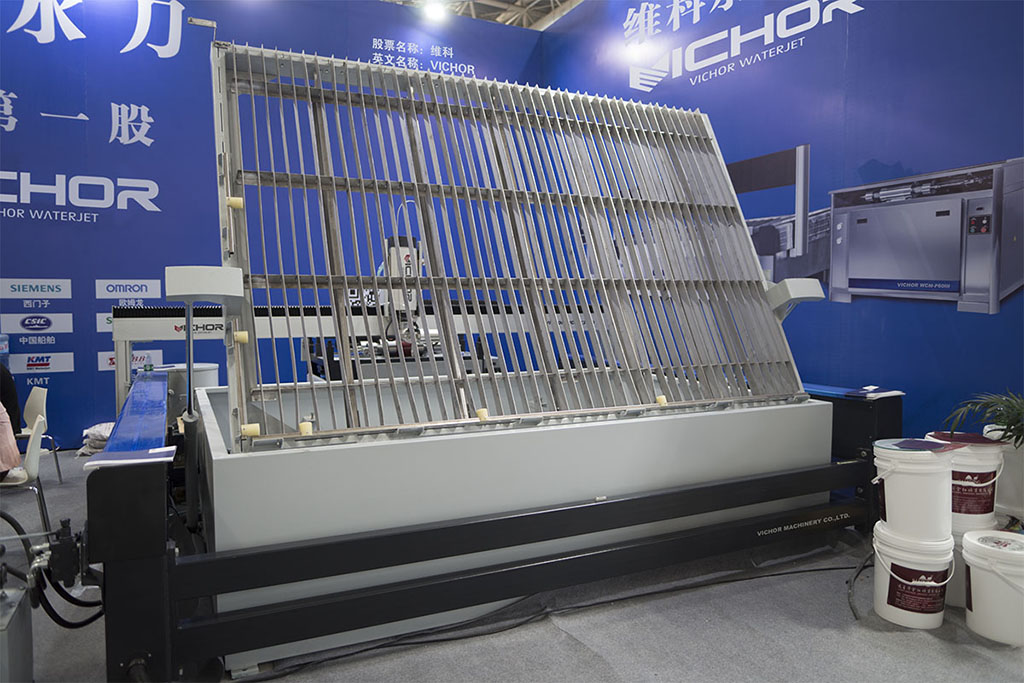
What Is a Plasma Water Jet and How Does It Revolutionize Cutting?
For decades, industries reliant on precision cutting faced a persistent challenge: cleanly slicing through incredibly hard or electrically conductive materials without damaging them. Traditional methods often fell short, leaving behind heat-affected zones, mechanical stress, or rough edges. Enter the plasma water jet – a groundbreaking hybrid technology merging the intense energy of plasma arcs with the cooling and focusing power of water. This article delves deep into the plasma water jet, exploring its principles, advantages, applications, and future potential.
1. The Core Principle: Merging Plasma and Water
At its heart, a plasma water jet system creates an incredibly focused, high-energy cutting stream through a sophisticated multi-stage process:
Plasma Generation: Inside a specialized torch, an electric arc is struck between an electrode (cathode) and either the workpiece (transferred arc) or the nozzle itself (non-transferred arc, less common in cutting). This arc ionizes a gas (often nitrogen, oxygen, argon/hydrogen mixtures, or even compressed air) passing through the torch, stripping electrons from atoms and creating the fourth state of matter: plasma. This plasma core reaches phenomenal temperatures, typically between 15,000°C and 30,000°C (27,000°F – 54,000°F).
Water Injection and Constriction: Crucially, a high-velocity vortex of water is injected radially into the plasma arc column within the torch nozzle. This water performs several critical functions simultaneously:
Constriction: The water vortex physically compresses the plasma arc, dramatically increasing its energy density and stability. Think of squeezing a hose to make the stream more powerful.
Cooling: The water rapidly cools the outer layers of the plasma stream and the torch nozzle itself, protecting the torch components from the extreme heat.
Stabilization: The swirling water vortex stabilizes the plasma arc, leading to a more consistent and precise cut.
Shielding: The water immediately surrounding the plasma core forms a protective steam layer, reducing oxidation and contamination of the cut surface, especially with inert gases.
Formation of the Cutting Jet: The intense heat of the constricted plasma arc instantly vaporizes the inner layer of the injected water. The resulting superheated steam becomes part of the ionized plasma stream. The outer layer of water remains liquid, forming a coherent, high-velocity sheath around the superheated plasma core. This combination – an ultra-hot, constricted plasma core enveloped by a high-speed water jacket – exits the nozzle as the powerful plasma water jet.
This unique synergy results in a cutting tool with significantly higher energy density and precision compared to conventional plasma or waterjet cutting alone.
2. Key Components of a Plasma Water Jet System
A robust plasma water jet system integrates several critical subsystems:
Power Supply: Provides the high-current DC power (often hundreds of Amperes) necessary to initiate and sustain the plasma arc. Precise control over current and voltage is vital for cut quality.
Gas Delivery System: Supplies and regulates the plasma gas(es) (e.g., nitrogen, oxygen, argon/hydrogen) at specific pressures and flow rates. The choice of gas significantly impacts cut quality, speed, and material compatibility.
Water Delivery System: A high-pressure pump (capable of 60-150 bar / 870-2175 psi) delivers ultra-pure, deionized water to the torch. Precise filtration is essential to prevent nozzle clogging. Flow control is critical for jet formation.
The Plasma Water Torch: The heart of the system. It houses the electrode, swirl ring for gas/water, nozzle (orifice), and shielding cap. Torch design, particularly the geometry controlling water injection and plasma constriction, is paramount for jet performance and nozzle life.
Motion Control System: A highly accurate CNC (Computer Numerical Control) system moves the torch precisely over the workpiece according to programmed cutting paths. High-speed, high-accuracy movement is crucial for complex contours and fine features.
Control Console & Software: The user interface for setting parameters (current, gas flow/pressure, water pressure/flow, cutting speed, torch height) and running cutting programs. Advanced systems include real-time monitoring and adaptive control features.
Work Table & Water Management: Supports the workpiece and efficiently drains the large volume of water and debris (dross) generated during cutting. Often includes water tanks, filtration, and recirculation systems.
The seamless integration and precise control of these components determine the effectiveness of the plasma water jet process.
3. Advantages Over Traditional Cutting Methods
The plasma water jet offers a compelling set of benefits, making it superior for specific applications compared to laser, oxy-fuel, conventional plasma, or abrasive waterjet cutting:
Exceptional Cut Quality on Conductive Materials: Delivers significantly smoother cut surfaces, near-vertical kerf walls (minimal bevel), and a drastically reduced or eliminated Heat-Affected Zone (HAZ) compared to conventional plasma. This is critical for materials sensitive to heat damage like stainless steel, aluminum, and copper alloys.
Higher Cutting Speeds: Particularly on thick sections of conductive metals (e.g., >25mm / 1-inch stainless steel, aluminum, copper), plasma water jet systems often outperform both conventional plasma and abrasive waterjet in terms of cutting speed.
Ability to Cut Reflective and Conductive Materials: Unlike CO2 or Fiber lasers, which struggle or fail with highly reflective materials like copper and brass, the plasma water jet handles them effortlessly. Its core mechanism relies on electrical conductivity.
Reduced Dross and Cleaner Cuts: The constricting water vortex and steam shielding result in much less molten slag (dross) adhering to the bottom edge of the cut, minimizing post-cut cleanup. Cut edges often require little to no secondary finishing.
Lower Operating Costs vs. Abrasive Waterjet: While the initial investment might be comparable, plasma water jet eliminates the ongoing cost of abrasive garnet, which is a major expense in abrasive waterjet operations. Consumables (nozzles, electrodes) are generally less costly than laser optics.
Improved Nozzle Life and Arc Stability: The water jacket provides excellent cooling, protecting the nozzle from heat erosion and significantly extending its lifespan compared to conventional plasma nozzles. The constriction also leads to a more stable arc.
Reduced Noise and UV Radiation: The water sheath effectively muffles the intense noise generated by the plasma arc and absorbs a significant portion of harmful ultraviolet (UV) radiation emitted, improving the working environment.
4. Diverse Industrial Applications
The unique capabilities of plasma water jet technology have led to its adoption across numerous demanding industries:
Aerospace: Cutting high-strength aluminum alloys, titanium components, and stainless steels for airframes, engine parts, and structural components where minimal HAZ and high precision are paramount. Plasma water jet ensures material integrity isn’t compromised by excessive heat.
Automotive: Manufacturing transmission components, chassis parts, suspension elements, and high-strength steel body-in-white parts requiring clean edges and precise tolerances.
Energy (Oil & Gas, Nuclear): Cutting thick-walled pipes, pressure vessels, heat exchangers, and reactor components made from stainless steel, duplex steels, and nickel alloys. The clean cut and minimal HAZ are crucial for weld preparation and component integrity in critical service.
Metal Fabrication & Job Shops: Offering a versatile solution for cutting a wide range of conductive metals (mild steel, stainless, aluminum, copper, brass) from thin sheets to very thick plates (100mm / 4 inches and beyond) with excellent quality and speed, handling diverse customer jobs efficiently.
Electronics & Semiconductors: Precision cutting of heat sinks (copper, aluminum), chassis, and specialized fixtures where thermal distortion must be absolutely minimized. The plasma water jet’s low HAZ is a key advantage here.
Transportation (Rail & Shipbuilding): Fabricating structural components, bogies, ship hull plates, and decking from thick steel and aluminum profiles.
Tool & Die Making: Creating molds, dies, and machine components requiring high dimensional accuracy and edge quality from tool steels.
5. Challenges, Considerations, and the Future Outlook
Despite its significant advantages, plasma water jet technology also presents challenges:
Material Limitation: Primarily effective only on electrically conductive materials. It cannot cut non-conductive materials like plastics, wood, ceramics, or composites (unlike abrasive waterjet or lasers).
Initial Investment: High-end plasma water jet systems represent a significant capital investment, potentially higher than some conventional plasma or oxy-fuel setups, though competitive with high-power lasers and abrasive waterjets.
Consumable Costs: While lower than abrasive waterjet garnet, electrodes and nozzles are wear parts and represent an ongoing operational cost. Maximizing their lifespan through optimal parameter settings is important.
Water Quality Requirements: Requires very pure, deionized water to prevent nozzle scaling and clogging, necessitating sophisticated water treatment systems.
Kerf Width: The kerf (cut width) of a plasma water jet is generally wider than that of a laser cutter, meaning slightly more material is removed. However, it is typically narrower than abrasive waterjet kerfs.
Process Complexity: Optimizing the numerous parameters (current, gas type/pressure/flow, water pressure/flow, cutting speed, torch height) requires expertise to achieve the best results consistently.
Looking Ahead:
The future of plasma water jet technology is bright, driven by continuous innovation:
Enhanced Precision & Speed: Ongoing developments in torch design, power supply stability, and motion control aim to push the boundaries of cut quality on thinner materials and increase cutting speeds further.
Improved Consumable Life: Research focuses on more durable electrode and nozzle materials (like hafnium inserts and advanced ceramics) and designs to reduce costs and downtime.
Smarter Control Systems: Integration of AI and machine learning for real-time process monitoring, adaptive control (automatically adjusting parameters for optimal cut quality), predictive maintenance, and simplified operation.
Hybrid Manufacturing: Exploring the integration of plasma water jet cutting with additive manufacturing (3D printing) processes for hybrid production cells.
Broader Material Compatibility: Research continues into techniques for cutting non-conductive materials or composites, potentially using auxiliary methods.
The plasma water jet stands as a testament to engineering ingenuity, solving critical challenges in industrial cutting. By harnessing the intense energy of plasma and masterfully controlling it with a vortex of water, this technology delivers unparalleled performance on thick, hard, and reflective conductive metals. Its key advantages – superior cut quality with minimal heat distortion, high speeds, and the ability to handle materials problematic for lasers – make it an indispensable tool in aerospace, energy, automotive, and advanced manufacturing. While challenges like material limitations and consumable costs exist, relentless innovation continues to refine the process, enhance capabilities, and broaden its reach. As industries demand ever-higher precision, efficiency, and material integrity, the plasma water jet is poised to remain at the forefront of advanced thermal cutting solutions, shaping the future of metal fabrication. Understanding its principles and applications is crucial for any industry seeking cutting-edge manufacturing capabilities.
continue reading
Related Posts
- 2163 words10.9 min read