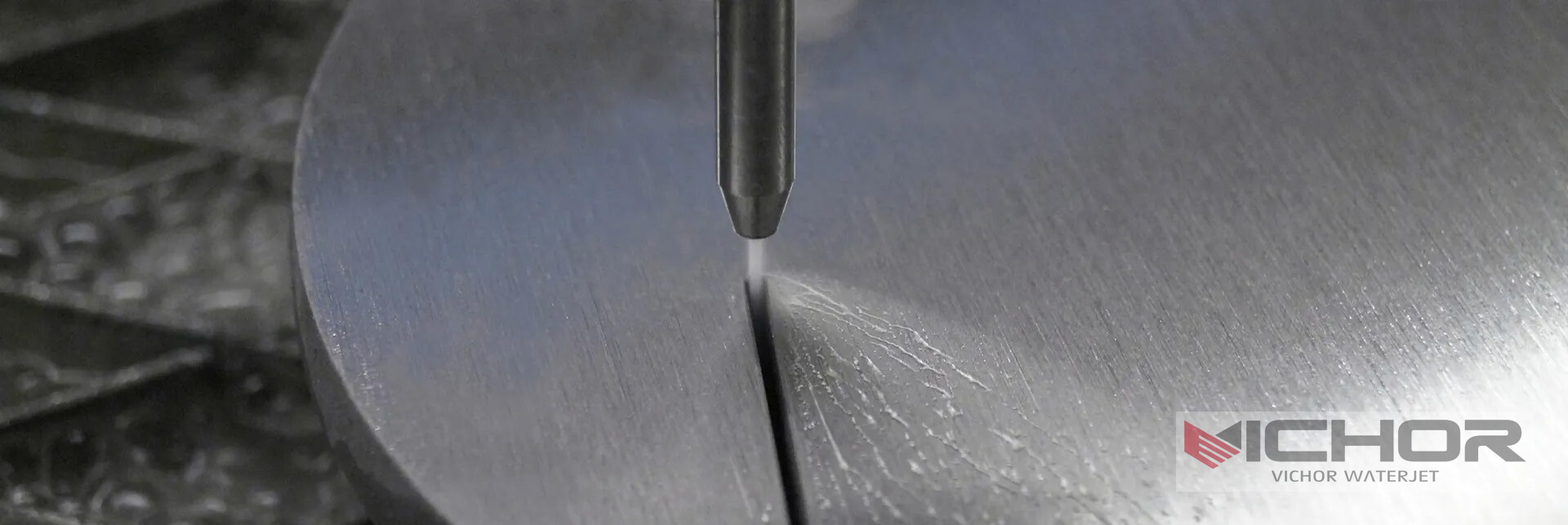
The Ultimate Guide to Water Cooled Laser Cutters: Benefits & How They Work
In the demanding world of precision fabrication, laser cutters reign supreme. But harnessing the intense power of a laser beam generates significant heat – heat that can cripple performance and destroy delicate components if not managed effectively. This is where the water cooled laser cutter becomes indispensable. Unlike simpler air-cooled counterparts, these systems utilize a sophisticated liquid cooling loop to maintain optimal operating temperatures, unlocking higher power, precision, and longevity. Whether you’re a seasoned manufacturer or exploring industrial-grade cutting solutions, understanding water cooled laser cutter technology is crucial. This comprehensive guide dives deep into five key aspects of these powerful machines, explaining their operation, advantages, applications, and critical considerations for potential buyers.
1. How Does Water Cooling Work in Laser Cutters? (The Core Mechanism)
At the heart of every water cooled laser cutter lies a closed-loop thermal management system. It’s far more complex than simply blowing air over components. Here’s a breakdown of the essential components and the cooling process:
Coolant Reservoir: Holds the cooling fluid, typically deionized water or a specialized water-glycol mixture. Deionization prevents mineral buildup and electrical conductivity.
Water Pump: Circulates the coolant under pressure throughout the entire cooling loop at a controlled flow rate.
Heat Exchanger: This is where the absorbed heat is dissipated. Coolant flows through tubes, while fans blow ambient air across fins attached to these tubes, transferring heat from the liquid to the air. Think of it like a car radiator for the laser.
Chiller Unit (Often Integrated): For high-power lasers or hot environments, a refrigeration unit cools the coolant below ambient temperature before it re-enters the laser, providing significantly greater cooling capacity than an ambient-only heat exchanger.
Cooling Channels & Cold Plates: Coolant flows through precisely machined channels embedded in or attached directly to critical components:
Laser Source (Tube or Resonator): This is the primary heat generator. Cooling channels surround the laser gas tube (CO2) or are integral to the diode arrays/modules (Fiber).
Optics: High-power mirrors and lenses can absorb heat from the laser beam itself. Water-cooled mounts stabilize their temperature.
Power Supplies & Electronics: High-current components like RF generators (CO2) or diode drivers (Fiber) generate substantial heat and require active cooling.
Temperature Sensors & Control System: Monitors coolant temperature at key points and regulates pump speed, chiller operation, and sometimes flow control valves to maintain a precise, stable temperature range.
The Cooling Cycle: Coolant absorbs heat as it flows past the laser source, optics, and electronics. This warmed fluid travels to the heat exchanger/chiller, releasing its heat to the surrounding air (or chilled refrigerant). The cooled liquid then returns to the reservoir and pump, ready to repeat the cycle. This continuous process maintains critical components within their narrow, optimal temperature window.
2. Key Advantages of Choosing a Water Cooled Laser Cutter
The investment in a water cooled laser cutter system delivers tangible benefits that directly impact performance, quality, and cost-effectiveness:
Superior Heat Dissipation & Stability: Water has a much higher heat capacity and thermal conductivity than air. This allows it to absorb vastly more heat per unit volume and transfer it away from components far more efficiently. This translates to exceptionally stable operating temperatures.
Enhanced Power Capability and Consistency: Stable temperatures are paramount for maintaining consistent laser output power. Water cooling enables lasers to operate reliably at their maximum rated power for extended periods without the power fluctuations and drop-offs common in air-cooled systems under load. This is especially critical for cutting thick materials or high-speed engraving.
Improved Beam Quality and Cut Precision: Thermal lensing – where heat causes optical components to distort, defocusing the laser beam – is a major enemy of precision. Water cooling minimizes temperature gradients in optics and the laser cavity itself, maintaining a stable, high-quality beam profile. This results in sharper cuts, finer details, and consistent kerf widths.
Extended Component Lifespan: Heat is the primary killer of lasers and sensitive electronics. By maintaining components at lower, stable temperatures, water cooling drastically reduces thermal stress and degradation. Laser tubes (especially CO2), diodes, optics, and power supplies last significantly longer, reducing costly downtime and replacement part expenses. This directly lowers the total cost of ownership.
Quieter Operation: While the chiller unit adds some noise, the core cooling of the laser source itself is often quieter than the high-velocity fans required for effective air cooling of high-power components. The noise is also typically a lower-frequency hum rather than a high-pitched fan whine.
Ability to Handle Demanding Environments: Water cooling provides a buffer against ambient temperature fluctuations. A water cooled laser cutter with a chiller can maintain performance even in hot factory environments where air-cooled systems would struggle or shut down due to overheating.
3. Water Cooling vs. Air Cooling: When is Water Essential?
Not all laser cutters require water cooling, but understanding the distinction is vital:
Air-Cooled Laser Cutters:
Mechanism: Rely on heatsinks and fans blowing ambient air directly over components (laser tube, electronics).
Power Range: Primarily used for lower-power systems (typically below 80W-100W for CO2, lower for some desktop Fiber lasers).
Pros: Simpler design, lower initial cost, no coolant maintenance, more portable.
Cons: Limited cooling capacity, susceptible to ambient temperature swings, prone to power instability at higher loads, shorter component lifespan under heavy use, louder fans, generally unsuitable for continuous industrial operation at higher powers.
Water Cooled Laser Cutters:
Mechanism: Closed-loop liquid cooling system as described previously.
Power Range: Essential for higher-power lasers (generally 100W+ CO2, most industrial Fiber lasers >1kW), and highly recommended for any laser used intensively or in challenging environments, even at medium powers.
Pros: Superior heat removal, stable power output, higher achievable power, better beam quality, longer component life, quieter laser source cooling, handles demanding environments.
Cons: Higher initial cost, more complex system, requires regular coolant maintenance (level checks, fluid changes, cleaning), needs dedicated space for chiller/reservoir, potential for leaks (mitigated by quality components and maintenance).
The Verdict: If you need consistent high-power performance, industrial reliability, maximum precision, long component life, and the ability to cut thick materials or run production shifts, a water cooled laser cutter is not just beneficial – it’s essential. Air-cooling is generally reserved for hobbyist, educational, or very light-duty professional applications at lower power levels.
4. Applications Where Water Cooled Laser Cutters Excel
The capabilities unlocked by water cooling make these machines the workhorses of numerous demanding industries:
Industrial Metal Fabrication: Cutting sheet metal (steel, stainless, aluminum), tubes, and profiles with high-power Fiber lasers (1kW to 10kW+). Water cooling is absolutely mandatory for thermal stability and component longevity at these power levels. Used for automotive parts, machinery components, architectural elements.
Precision Engineering: Manufacturing intricate parts from metals, ceramics, and specialized alloys requiring micron-level accuracy and minimal heat-affected zones. Stable temperature ensures consistent results.
Signage and Architectural Metalwork: Producing detailed letters, decorative panels, railings, and structural elements from various metals where clean edges and precision are paramount.
Aerospace and Defense: Cutting high-strength, heat-sensitive alloys and composites for critical components. Water cooling ensures process reliability and material integrity.
Tool and Die Making: Creating molds, dies, and precision tooling where dimensional accuracy is non-negotiable. Stable laser power prevents defects.
High-Volume Acrylic and Plastic Processing: Cutting thick acrylic sheets or performing high-speed engraving on plastics with high-power CO2 lasers requires sustained power only possible with water cooling.
Medical Device Manufacturing: Fabricating precise, clean-cut components from medical-grade metals and polymers.
Research and Development: Labs requiring stable, high-power laser output for material processing experiments rely on water cooled laser cutter systems.
5. Choosing and Maintaining Your Water Cooled Laser Cutter
Investing in a water cooled laser cutter requires careful consideration and commitment to maintenance:
Selection Criteria:
Laser Type & Power: Match the cooling capacity to the laser source (CO2, Fiber) and its wattage. Higher power demands more robust cooling (larger reservoir, higher flow pump, powerful chiller).
Cooling Capacity: Ensure the chiller/heater unit has sufficient BTU/hr (or kW) rating to handle the laser’s heat output plus a safety margin, considering your maximum ambient temperature. Consult the laser manufacturer’s specifications.
Coolant Quality: Use ONLY deionized (DI) water or manufacturer-recommended coolant mixtures. Tap water causes scaling, corrosion, and algae growth, destroying the system. Additives inhibit biological growth and corrosion.
System Quality: Look for reliable pumps (preferably magnetic drive to prevent seal leaks), corrosion-resistant components (brass, stainless steel), clear reservoir for level checks, and a reputable chiller brand.
Flow Monitoring & Protection: Ensure the system has flow sensors and temperature sensors that automatically shut down the laser if coolant flow stops or temperature exceeds safe limits, preventing catastrophic damage.
Essential Maintenance:
Coolant Level: Check DAILY before operation. Top up only with DI water or the correct coolant mixture. Never let the pump run dry.
Coolant Quality: Monitor color and clarity. Replace coolant according to the manufacturer’s schedule (typically every 6-12 months). Test conductivity/resistivity periodically (DI water should have high resistivity >1 MΩ·cm).
System Cleanliness: Keep the reservoir and fill cap clean. Periodically clean or flush the system if contamination is suspected. Clean the chiller’s air intake filter and condenser coils regularly (monthly or as needed) – clogged coils drastically reduce cooling efficiency.
Leak Checks: Routinely inspect tubing, connections, and the reservoir for any signs of leaks. Address immediately.
Temperature Calibration: Periodically verify the accuracy of temperature sensors, especially on the chiller.
Winterization (if applicable): In freezing environments, use a coolant mixture with antifreeze properties or ensure the machine/chiller is kept in a heated space. Drain water systems if necessary.
The water cooled laser cutter is not merely an option; it is the technological backbone enabling high-power, high-precision, and reliable industrial laser processing. By efficiently managing the intense heat generated during operation, water cooling systems unlock consistent beam quality, maximize cutting power, extend the operational lifespan of expensive components, and ensure production stability even in challenging environments. While requiring a higher initial investment and diligent maintenance compared to air-cooled systems, the long-term benefits in performance, reliability, quality, and total cost of ownership are undeniable. For any serious fabrication shop, manufacturer, or research facility pushing the boundaries of laser cutting and engraving, investing in a robust water cooled laser cutter system is a fundamental requirement for achieving exceptional and sustainable results. Understanding the technology, its advantages, and its care ensures you harness its full potential for years to come.
continue reading