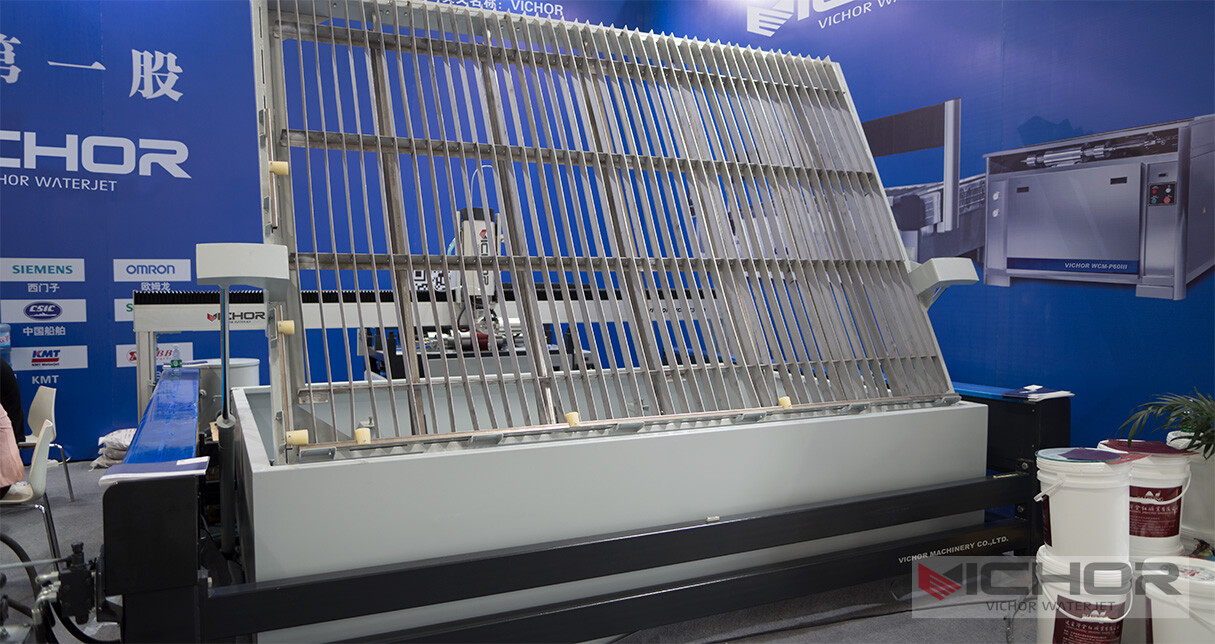
What is the Function of the Water Jet? Unveiling the Power of Precision Cutting
The term “water jet” evokes images of power and precision, but what is the function of the water jet at its core? It’s far more than just high-pressure water. The primary function of a water jet is to harness the immense kinetic energy of an ultra-high-pressure stream of water, often mixed with abrasive particles, to cut, shape, clean, or erode a vast array of materials with exceptional accuracy and minimal thermal or mechanical stress. This unique technology has revolutionized manufacturing, fabrication, and numerous other industries by offering capabilities unmatched by traditional thermal cutting methods like lasers or plasma. Let’s delve into the multifaceted function of the water jet across five key areas.
1. Precision Cutting Through Virtually Any Material
The most prominent function of the water jet is its unparalleled ability to perform precision cutting. This capability stems from the focused energy of the water stream, travelling at speeds up to three times the speed of sound (Mach 3).
How it Works: A high-pressure pump intensifies water pressure to levels ranging from 40,000 PSI (2,750 bar) to over 100,000 PSI (6,900 bar). This pressurized water is forced through a small orifice, typically made of sapphire or diamond, creating an incredibly focused, coherent stream. When abrasives (like garnet) are introduced into this stream just after the orifice, the function of the water jet transforms. The water acts as the carrier and accelerator, propelling the abrasive particles that perform the actual cutting through erosion. Pure water jets (without abrasives) excel at cutting softer materials like rubber, foam, food, and gaskets.
The Result: This process allows water jets to cut intricate shapes, sharp corners, and complex geometries with tolerances as tight as +/- 0.003 inches (+/- 0.076 mm). Unlike thermal processes, there is no Heat-Affected Zone (HAZ), meaning the material properties adjacent to the cut remain completely unchanged – a critical function of the water jet for materials sensitive to heat. The kerf (cut width) is very narrow, minimizing material waste.
2. Handling an Unmatched Range of Materials
A defining function of the water jet is its extraordinary material versatility. It is truly an “omni-cutter.”
Metals: Easily cuts through hardened tool steel, titanium, aluminum, brass, copper, stainless steel (including thick plates), armor plate, and exotic alloys. The lack of heat prevents hardening, warping, or altering the metallurgical structure.
Composites & Laminates: Water jet cutting is ideal for carbon fiber, fiberglass, Kevlar, and other composites. It delaminates significantly less than mechanical or thermal methods, preserving the integrity of layered materials – a crucial function of the water jet in aerospace and automotive industries.
Stone, Tile, and Glass: Cuts granite, marble, ceramic, porcelain tile, and glass (even bulletproof) with clean edges and minimal chipping, perfect for intricate decorative work and countertops.
Plastics & Polymers: Cuts acrylics, polycarbonate, PVC, HDPE, and other plastics without melting or releasing harmful fumes associated with laser cutting. This function of the water jet ensures a clean, burr-free edge.
Rubber, Foam, and Soft Materials: Pure water jets excel here, cleanly cutting rubber seals, gaskets, foam insulation, carpet, and even food products without crushing or tearing.
Exotic Materials: Handles materials like bulletproof glass, tungsten, inconel, and concrete effectively.
This universal cutting capability eliminates the need for multiple specialized cutting machines, streamlining production.
3. Performing a Truly “Cold” Cutting Process
A fundamental and unique function of the water jet is its operation as a cold cutting process. This stands in stark contrast to lasers, plasma, oxy-fuel, and EDM, all of which generate intense localized heat.
Eliminating the Heat-Affected Zone (HAZ): The absence of heat during cutting is perhaps the most significant advantage derived from the function of the water jet. There is no thermal distortion, hardening, annealing, or micro-cracking in the material surrounding the cut path. The base material properties remain completely intact.
No Thermal Stress: Materials prone to warping or cracking under heat (like thin metals, tempered glass, certain plastics, and hardened steels) are perfectly suited for water jet cutting. This function of the water jet ensures dimensional stability and prevents costly post-processing to correct heat-induced distortion.
Safety: The cold process eliminates fire hazards associated with hot cutting methods, making it safer for cutting flammable materials or in environments where sparks pose a risk.
4. Minimizing Contamination and Environmental Impact
An essential function of the water jet is its ability to cut with minimal contamination and relatively low environmental impact compared to some alternatives.
No Hazardous Fumes/Vapors: Unlike plasma or laser cutting certain materials (especially plastics or coated metals), the water jet process does not produce toxic fumes or noxious gases. The primary byproducts are the cut material (slurry) and the spent abrasive (in abrasive cutting). This creates a cleaner and safer working environment.
Reduced Secondary Waste: The narrow kerf minimizes material waste. The slurry (a mixture of water, abrasives, and cut material particles) can often be collected and processed. Abrasive garnet is non-toxic and can sometimes be recycled or disposed of more easily than hazardous chemical waste.
Water Usage: While water is the primary medium, modern systems are designed with efficiency in mind. Water is typically filtered and recirculated within the high-pressure pump system. The actual cutting water, mixed with abrasives and material, becomes slurry but the core pump system minimizes fresh water consumption during operation. Compared to chemical etching or some machining coolants, the function of the water jet is often more environmentally benign.
5. Enabling Complex Shaping and Secondary Operations
Beyond simple cuts, a vital function of the water jet is facilitating complex shaping and preparing parts for downstream processes.
Intricate Geometries: The small kerf and lack of tooling forces allow water jets to cut incredibly complex shapes, sharp inside corners, and fine details that are difficult or impossible with milling machines or punches. This is invaluable for prototypes, decorative elements, and complex parts.
Bevel Cutting: Advanced 5-axis water jet heads can tilt the cutting nozzle, enabling the cutting of precise bevels and angles on thick materials in a single pass, ready for welding. This eliminates secondary machining operations.
Drilling & Milling: Water jets can perform piercing, drilling holes (especially small or shaped holes), and even limited milling operations on certain materials.
Surface Preparation (Hydrodemolition): While distinct from cutting, ultra-high-pressure water jets (often without abrasives) are used for precise concrete removal (hydrodemolition), surface cleaning (paint, coatings, rust), and surface texturing/roughening for better adhesion. This showcases a related but powerful function of the water jet.
Net-Shape Cutting: The precision of water jet cutting often allows parts to be cut to their final “net” shape, significantly reducing or eliminating the need for subsequent finishing operations like grinding or milling. This reduces lead times and costs.
So, what is the function of the water jet? It is not a single action but a symphony of capabilities centered around harnessing kinetic energy. The core function of the water jet is to provide a precise, versatile, cold, and relatively clean method of material processing. Its ability to cut virtually any material without inducing heat damage, its capacity for extreme complexity, and its minimal environmental footprint make it an indispensable tool across countless industries – from aerospace and automotive manufacturing to art, architecture, food processing, and electronics.
The function of the water jet solves problems that other technologies cannot. Where heat is the enemy, the water jet excels. Where material diversity is required, the water jet adapts. Where precision is paramount, the water jet delivers. Understanding these key functions reveals why water jet technology continues to grow and evolve as a cornerstone of modern fabrication and manufacturing. It transforms a simple stream of water into a tool of remarkable power and finesse.
continue reading
Related Posts
- 1559 words7.8 min read