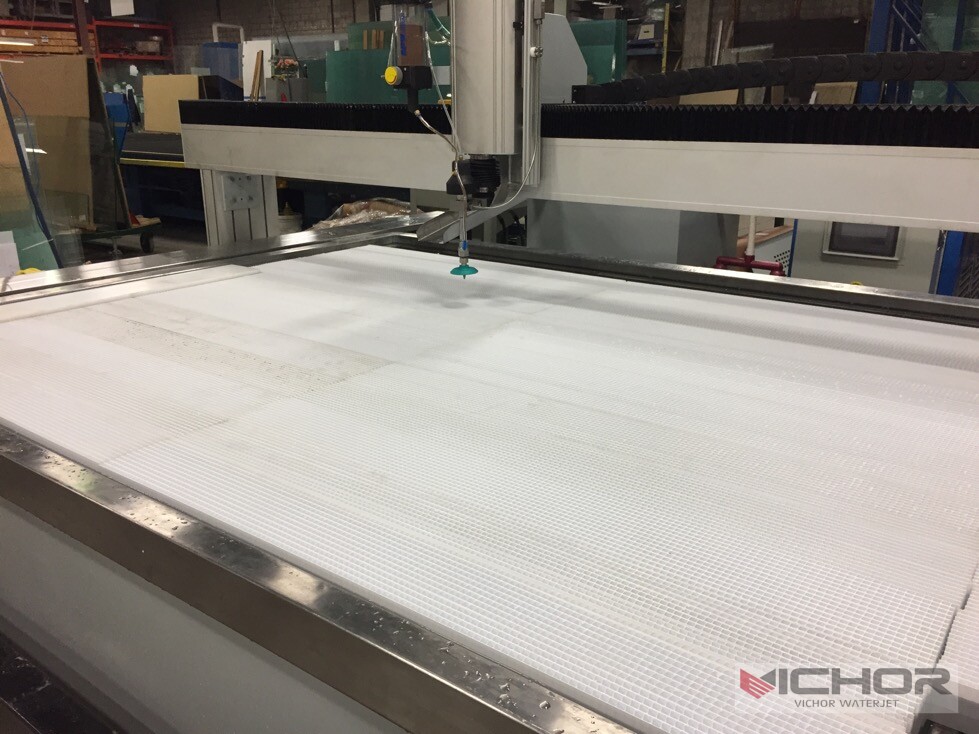
What is the Best Waterjet Machine? 5 Critical Factors for Choosing Your Ideal Cutter
In the world of precision cutting, waterjet technology stands out as one of the most versatile, powerful, and material-agnostic solutions available. From delicate composites to thick armor plate, a best waterjet machine offers unparalleled flexibility without generating heat-affected zones or hazardous fumes. But with numerous manufacturers and configurations on the market, identifying the truly best waterjet machine for your specific needs can be challenging. This comprehensive guide dives deep into the five most critical aspects to evaluate, ensuring you make an informed investment that maximizes productivity and return.
1. Cutting Technology & Capability: Pure vs. Abrasive Waterjet
The core function defines the best waterjet machine. Understanding the two primary cutting methods is essential:
Pure Waterjet Cutting: Utilizes ultra-high-pressure water (often 60,000-90,000 PSI) focused through a tiny gem orifice (typically 0.004″ to 0.016″). This creates a supersonic stream ideal for cutting soft materials like rubber, foam, gaskets, food products, insulation, carpets, paper, and thin plastics. Pure waterjet systems are generally quieter, require less maintenance on the cutting head (no abrasive mixing tube), and have lower consumable costs (no abrasive). For businesses primarily working with these softer materials, a pure waterjet configuration might represent the best waterjet machine for their budget and needs.
Abrasive Waterjet Cutting: Adds a precisely metered stream of fine garnet abrasive (usually #80 mesh) into the high-pressure water stream within a mixing chamber. This transforms the water into an incredibly erosive tool capable of slicing through virtually any material – metals (steel, aluminum, titanium, copper), stone, granite, marble, ceramics, glass, composites, and thick plastics. The cutting power is immense, enabling thicknesses exceeding 12 inches in some materials. For versatility and the ability to tackle hard materials, an abrasive waterjet is overwhelmingly considered the best waterjet machine solution for most industrial applications. Key capability factors include maximum pressure (directly impacts cutting speed and thickness capacity), abrasive delivery system consistency, and precision nozzle design.
2. Precision & Accuracy: Engineering Excellence Matters
A best waterjet machine isn’t just powerful; it’s incredibly precise. Modern systems rival laser and plasma cutting in accuracy for many applications. Key elements influencing precision include:
Motion System & Drive Technology: The foundation of accuracy. Look for robust, thermally stable frames (often granite or polymer concrete bases) and high-quality linear guides. Servo motors with precision ball screws or linear motors offer superior speed, acceleration, and positional accuracy compared to older stepper motor systems. Closed-loop feedback ensures the machine knows exactly where the cutting head is at all times. Dynamic height control (DHC) systems automatically maintain the optimal nozzle standoff distance, crucial for consistent kerf width and edge quality, especially on contoured surfaces.
Control System & Software: The machine’s “brain.” A sophisticated CNC control system (like those from Siemens, Fanuc, or proprietary high-end systems) interprets CAD/CAM instructions and precisely coordinates motion, water pressure, abrasive feed, and DHC. Intuitive, powerful software is vital for efficient nesting (arranging parts to minimize waste), optimizing cutting paths, managing pierce sequences, and simulating cuts. The best waterjet machine for intricate work will offer features like taper compensation (adjusting the cutting path to account for the natural V-shape kerf), kerf compensation, and advanced piercing routines to minimize splashback and damage.
Repeatability & Tolerance: High-end machines consistently achieve positional repeatability within +/- 0.001″ (0.025mm) and cutting tolerances of +/- 0.003″ to 0.005″ (0.075mm to 0.125mm) or better, depending on material and thickness. This level of precision is essential for aerospace, medical device manufacturing, and tooling applications.
3. Material Versatility & Thickness Capacity: The Ultimate Flexibility
Arguably the most significant advantage of waterjet cutting is its ability to handle an astonishingly wide range of materials without changing the fundamental process. A best waterjet machine truly shines here:
Unmatched Material Range: Cut metals (hardened tool steel, aluminum, brass, titanium), stone and tile, glass, laminated composites (carbon fiber, fiberglass), plastics (acrylic, PVC, Delrin), rubber, foam, food, paper, and exotic materials – all on the same machine. No thermal stress means no warping, hardening, or micro-cracking along the cut edge. This eliminates secondary processing often required after thermal cutting.
Impressive Thickness Capacity: While cutting speed decreases with thickness, waterjets excel where lasers and plasma struggle. A powerful best waterjet machine can cleanly cut through:
6-8+ inches (150-200mm+) of stainless steel or titanium
10-12+ inches (250-300mm+) of aluminum
12-18+ inches (300-450mm+) of stone, concrete, or armor plate
Edge Quality: Waterjet cutting produces a smooth, sandblasted finish. While not always mirror-smooth like a fine laser cut, the edge is typically ready for use or requires minimal finishing. The lack of a heat-affected zone (HAZ) preserves the material’s intrinsic properties right up to the cut edge, critical for structural integrity and preventing corrosion in metals or delamination in composites.
4. Productivity & Throughput: Power, Speed, and Automation
In a production environment, the best waterjet machine must deliver not just quality cuts, but also competitive throughput. Key productivity drivers include:
High-Pressure Pump: The heart of the system. Direct-drive pumps (like KMT’s Streamline Pro or Flow’s Dynamic Waterjet Pumps) offer superior reliability, higher sustained pressure (up to 94,000+ PSI), faster acceleration to cutting pressure, and lower energy consumption compared to older intensifier pumps. Higher pressure directly translates to faster cutting speeds, especially in thicker materials. Look for pumps known for durability and ease of maintenance.
Cutting Speed: While slower than lasers on thin sheet metal, waterjets are often faster on thicker sections and vastly outperform lasers and plasma on non-metallics. The best waterjet machine leverages high pressure, efficient abrasive mixing, and optimized motion control to maximize cutting velocity for a given material and thickness. Real-world speeds vary significantly but expect inches per minute (ipm) rates ranging from 100+ ipm in thin aluminum down to 1-2 ipm in very thick steel.
Automation Integration: True high-volume productivity requires automation. The best waterjet machine platforms are designed for integration with:
Automatic Loading/Unloading (Robotic Arms, Gantry Systems): Minimizes operator intervention for loading sheets and unloading finished parts or skeletons.
Multi-Head Cutting: Some larger systems can operate two or more cutting heads simultaneously, dramatically increasing throughput for suitable parts.
In-Process Piercing: Advanced systems can pierce thick materials without flipping or pre-drilling.
Nesting Software Optimization: Maximizing material utilization by efficiently packing parts significantly reduces waste costs.
Abrasive & Water Management Systems: Automated abrasive delivery and closed-loop water recycling systems reduce manual handling and consumable costs.
5. Operational Costs & Ease of Use: Total Cost of Ownership (TCO)
The purchase price is just the beginning. Evaluating the long-term TCO is crucial for identifying the best waterjet machine investment:
Abrasive Consumption: Garnet abrasive is the single largest ongoing consumable cost in abrasive waterjetting. The best waterjet machine optimizes abrasive usage through precise metering systems, efficient mixing technology, and potentially garnet recycling systems. Lower consumption rates directly impact profitability.
Pump Maintenance & Reliability: Pump downtime is costly. Direct-drive pumps generally offer lower maintenance requirements and costs compared to intensifiers. Look for manufacturers with strong service networks and readily available parts. Predictive maintenance features are a plus.
Energy Efficiency: High-pressure pumps consume significant electricity. Newer direct-drive pumps are substantially more energy-efficient than older intensifier technology or even older direct-drive models. Reduced kW consumption per hour of cutting lowers operating costs.
Nozzle & Consumable Life: Orifices (waterjet nozzles), mixing tubes, and focus tubes wear and need regular replacement. High-quality components and designs that extend consumable life reduce costs and machine downtime. Ease of replacement is also important.
Water Consumption & Filtration: While water is a consumable, closed-loop filtration and recycling systems are standard on modern machines, minimizing water waste and disposal costs. Efficient systems require less make-up water.
Software & Training: Intuitive control software reduces training time and minimizes operator errors. Look for software with good support, regular updates, and features that streamline programming (like CAD/CAM integration libraries).
Footprint & Facility Requirements: Consider the physical space needed for the machine, pump, water tank, and abrasive storage. Ensure your facility has adequate power supply, floor strength, and potentially sound dampening.
There is no single, universal “best waterjet machine.” The ideal choice hinges entirely on your specific application requirements, production volume, material mix, precision demands, and budget constraints.
High-Mix, Low-Volume Job Shops: Prioritize versatility, precision, ease of setup/use, and lower entry cost. A robust 5’x10′ or 6’x12′ abrasive system with a reliable direct-drive pump might be ideal.
High-Volume Metal Fabricators: Focus on high throughput, automation readiness (loading/unloading), cutting speed (especially in mid-thickness ranges), and low abrasive consumption. Larger tables and potentially multi-head systems become relevant.
Stone & Tile Fabricators: Need power for thick materials, large table sizes (8’x12′ or larger), excellent edge quality (minimal chipping), and efficient water/sludge management.
Aerospace & Medical: Demand ultra-high precision, superior repeatability, minimal HAZ on sensitive alloys and composites, and advanced software features like taper compensation.
By rigorously evaluating these five critical pillars – Cutting Technology & Capability, Precision & Accuracy, Material Versatility & Thickness Capacity, Productivity & Throughput, and Operational Costs & Ease of Use – you move beyond marketing claims. You gain the insight needed to identify the true best waterjet machine that will deliver optimal performance, reliability, and return on investment for your unique business, solidifying its place as an indispensable tool in your manufacturing arsenal. Carefully assess your needs, consult with reputable manufacturers, request material test cuts, and consider the long-term TCO to make the most informed decision.
continue reading
Related Posts
- 2225 words11.2 min read
- 1448 words7.3 min read