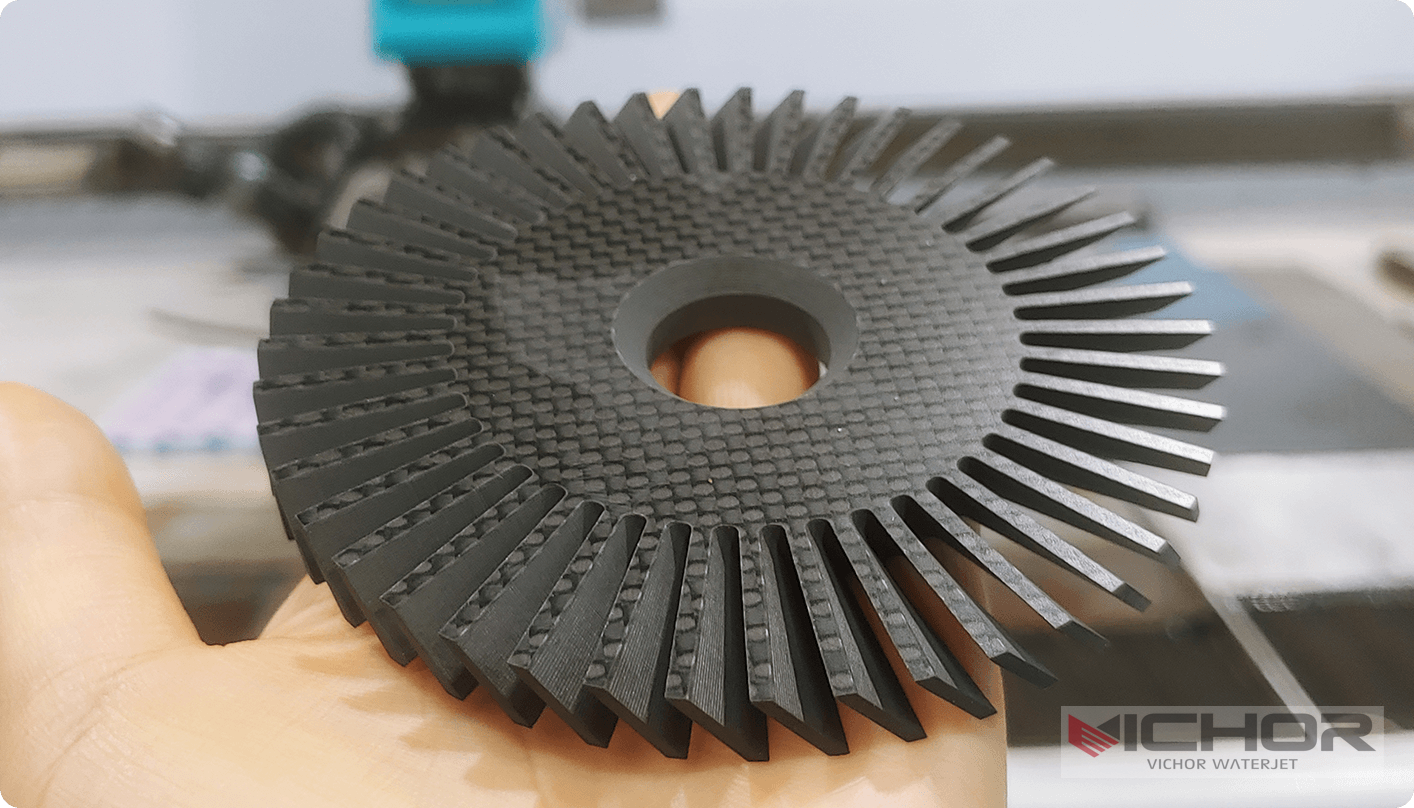
Waterjet Pumps Explained: The Ultimate Guide to Types, Technology & Applications
In the world of precision cutting and surface preparation, few technologies match the versatility and power of waterjet systems. At the very heart of these powerful machines lies the critical component responsible for generating the immense force required: the waterjet pump. Understanding these pumps is fundamental to grasping waterjet technology’s capabilities, limitations, and optimal operation. This comprehensive guide delves deep into waterjet pumps, exploring their function, types, key components, performance factors, applications, and maintenance essentials.
Introduction: The Powerhouse Behind Precision Cutting
A waterjet cutter harnesses the erosive power of a supersonic stream of water, often mixed with abrasive garnet, to slice through materials ranging from soft foam and rubber to hardened steel, titanium, stone, and composites. But this incredible capability doesn’t originate at the cutting head; it begins far upstream, within the waterjet pump. These pumps are sophisticated, high-pressure systems designed to take ordinary tap water (or filtered water) and pressurize it to extreme levels, typically between 60,000 PSI (4,100 bar) and 94,000 PSI (6,500 bar), though some specialized systems operate outside this range. This pressurized water is the lifeblood of the waterjet process. Without a reliable, high-performance waterjet pump, the entire cutting system is rendered ineffective. They are the unsung heroes, transforming potential energy into the kinetic energy that drives modern manufacturing and fabrication.
1. How Waterjet Pumps Work: The Intensifier Principle vs. Direct Drive
There are two primary technologies used to generate the ultra-high pressures required for waterjet cutting: Intensifier Pumps and Direct Drive (or Crankshaft) Pumps. Understanding the fundamental difference is key.
Intensifier Pumps (The Most Common Type):
Principle: These waterjet pumps utilize Pascal’s Law, which states that pressure applied to a confined fluid is transmitted undiminished throughout the fluid. They employ a hydraulic system driven by a lower-pressure oil pump (typically 3,000 PSI / 200 bar).
The Intensification Process: Hydraulic oil acts on a large-area piston. This piston is mechanically linked to a smaller-area plunger on the water side. Because force = pressure x area (F = P x A), the same force generated by the oil on the large piston is concentrated onto the much smaller water plunger. This results in a significant pressure multiplication. The ratio of the piston area to the plunger area determines the intensification ratio (e.g., 20:1). A 3,000 PSI oil pressure acting on a 20:1 intensifier generates 60,000 PSI water pressure.
Reciprocating Action: Intensifiers operate reciprocally. As the hydraulic piston moves in one direction, it pushes the water plunger, pressurizing water on that side and discharging it. Simultaneously, the opposite plunger is retracting, filling with low-pressure water. A sophisticated valve system (often a sliding “spool” valve) synchronizes this action, directing oil flow and switching water inlet/outlet ports to ensure a relatively smooth flow output despite the reciprocating motion. Most modern intensifier waterjet pumps use dual opposed plungers to help balance forces and reduce vibration, improving flow consistency.
Output: Delivers pulsating flow due to the reciprocating action, though accumulators dampen this significantly. Capable of generating the highest pressures (up to 94,000+ PSI).
Direct Drive (Crankshaft) Pumps:
Principle: These waterjet pumps operate much like a car engine but pressurizing water instead of air-fuel mixtures. An electric motor drives a rotating crankshaft connected to multiple plungers (typically 3 or more) via connecting rods.
Pressurization Process: As the crankshaft rotates, the plungers move in and out of their respective cylinders in a phased sequence. On the intake stroke, a valve opens, allowing water to fill the cylinder. On the compression stroke, the valve closes, and the plunger forces the water out at high pressure through a check valve.
Output: The phased action of multiple plungers results in a much smoother, nearly continuous flow output compared to intensifiers, with minimal pulsation. They are generally more energy-efficient at lower pressures and flow rates.
Limitations: Historically, direct drive pumps were limited to lower maximum pressures (typically maxing out around 60,000-65,000 PSI) due to the challenges of sealing and managing extreme forces on rotating components. However, technological advancements are pushing these limits higher. They also tend to be more complex mechanically than intensifiers.
2. Core Components of a Waterjet Pump System
A waterjet pump is more than just the pressure-generating unit. It’s an integrated system comprising several critical components:
Prime Mover: Usually a high-efficiency electric motor (AC or DC) providing the primary power to drive either the hydraulic pump (intensifier) or the crankshaft (direct drive).
Hydraulic Power Unit (HPU – Intensifier Pumps Only): Consists of a hydraulic pump, reservoir, filters, coolers, and control valves. It generates the lower-pressure hydraulic oil flow that drives the intensifier’s large piston.
Intensifier Assembly or Crankshaft Assembly: The core pressure-generating mechanism, as described above. Includes pistons, plungers, cylinders, rods, and seals.
High-Pressure Cylinders & Plungers: Made from ultra-strong, wear-resistant materials like ceramic, tungsten carbide, or hardened stainless steel. They withstand extreme pressures and friction. Seal life is a critical maintenance factor here.
Valving System:
Intensifier: Sophisticated spool or poppet valves control the direction of hydraulic oil flow to reverse the piston/plunger motion and switch the water inlet/outlet ports.
Direct Drive: Check valves (inlet and outlet) on each plunger cylinder control water flow direction.
High-Pressure Accumulators: Essential vessels filled with nitrogen gas acting like a “spring.” They absorb pressure pulsations from the reciprocating action of the pump, delivering a significantly smoother flow of water to the cutting head. This protects downstream components and improves cut quality.
Water Filtration System: Crucial for pump longevity. Multi-stage filtration (often including sediment filters, water softeners, and sometimes deionizers) removes particles, minerals, and contaminants from the inlet water. Impurities cause rapid wear of seals and check valves in high-pressure waterjet pumps.
Cooling System: Removes heat generated by compression and friction within the pump. May involve heat exchangers using chilled water or refrigerant circuits. Overheating is a major cause of pump failure.
Control System & Sensors: Modern waterjet pumps feature sophisticated PLCs or dedicated controllers monitoring pressure, temperature, flow, motor status, seal life, and diagnostic data. They provide operational control, safety interlocks, and user interfaces.
High-Pressure Tubing: Thick-walled, seamless stainless steel tubing capable of handling extreme pressures safely, connecting the pump outlet to the cutting head.
3. Key Performance Factors and Specifications
When evaluating waterjet pumps, several critical specifications define their capability and suitability for an application:
Maximum Operating Pressure (PSI/Bar): The highest pressure the pump can reliably and safely generate. Determines the maximum material thickness and cutting speed achievable, especially with abrasives (higher pressure = faster cutting on hard/thick materials). Common ratings are 60K, 87K, 90K, 94K PSI.
Horsepower (HP/kW): The power rating of the electric motor driving the pump. Directly relates to the pump’s ability to generate both high pressure and high flow. Higher HP allows higher flow rates at target pressures.
Flow Rate (GPM/LPM): The volume of pressurized water the pump can deliver per minute at a specified pressure. Higher flow rates enable faster cutting speeds and/or the use of larger orifice sizes. Flow rate typically decreases as pressure increases for a given pump/HP.
Pressure Stability & Pulsation: How consistently the pump maintains the set pressure and how much fluctuation (pulsation) exists in the output stream. Lower pulsation (damped by accumulators) translates to better cut quality, especially edge finish and taper control. Direct drives inherently offer smoother flow.
Efficiency: The ratio of hydraulic/mechanical power output (pressure x flow) to the electrical power input. Direct drive pumps often have higher efficiency at lower pressures, while intensifiers can be efficient across a wider pressure range, especially at peak pressures. Overall system efficiency impacts operating costs.
Duty Cycle: The percentage of time the pump can operate at its maximum rated pressure and flow without overheating or excessive wear. Industrial waterjet pumps are typically designed for near-continuous duty (90-100%).
Seal Life: The expected operating hours before high-pressure seals need replacement. Seal life is heavily influenced by water quality, operating pressure, and temperature. Longer seal life reduces maintenance downtime and costs. Key metric for TCO (Total Cost of Ownership).
4. Applications: Where Waterjet Pumps Drive Innovation
The high-pressure water generated by waterjet pumps unlocks capabilities across diverse industries:
Precision Metal Fabrication: Cutting complex shapes from sheet metal (steel, aluminum, brass, copper), plates, tubes, and structural components with no heat-affected zone (HAZ), preserving material properties. Essential for aerospace, automotive, and machinery.
Stone and Tile Processing: Cutting intricate countertops, tiles, mosaics, and architectural elements from granite, marble, quartz, and other natural or engineered stone. Allows for complex designs impossible with saws.
Glass Cutting: Creating shapes for architectural glass, automotive windows, mirrors, and decorative panels with smooth edges and minimal chipping.
Composites Manufacturing: Cutting carbon fiber, fiberglass, Kevlar, and laminates without delamination or fraying, crucial for aerospace and high-performance sports equipment.
Food Processing: Using pure waterjets (no abrasive) for hygienic, cold cutting of frozen foods, pastries, meat, poultry, and fish. Precise portioning with no contamination.
Rubber, Plastics, and Foam: Cutting gaskets, seals, insulation, packaging materials, and intricate foam prototypes cleanly and accurately.
Electronics: Precision cutting of circuit boards, thin films, and delicate components where heat and mechanical stress must be avoided.
Surface Preparation & Coatings Removal: Using lower-pressure pure waterjets for cleaning, paint stripping, rust removal, and surface texturing without damaging the substrate.
Demolition and Decommissioning: High-powered waterjets cut through concrete, rebar, and hazardous materials (like radioactive components) with minimal dust, vibration, and spark risk.
Art and Sculpture: Enabling artists to create intricate designs from a vast array of materials.
5. Selection, Operation, and Maintenance Best Practices
Choosing and maintaining the right waterjet pump is critical for performance and longevity:
Selection Criteria:
Material & Thickness: Harder, thicker materials demand higher pressure (87K+ PSI). Thinner materials or softer substances can use lower pressure (60K PSI).
Required Cut Quality & Speed: Higher pressure and flow generally enable faster speeds and better edge quality on challenging cuts. Smoother pumps improve finish.
Production Volume: High-volume shops need robust pumps with high duty cycles, long seal life, and easy maintenance access.
Available Power & Space: Pump HP dictates electrical requirements. Intensifier systems tend to be larger due to the HPU.
Budget (Initial & Operating): Consider purchase price, energy consumption, expected maintenance costs (seals, filters, parts), and uptime.
Water Quality: Poor water necessitates more extensive filtration, impacting cost and maintenance. Assess your water source.
Operation:
Water Quality is Paramount: Rigorously maintain the filtration system. Test water hardness and TDS (Total Dissolved Solids) regularly. Follow manufacturer guidelines strictly. This is the #1 factor affecting seal and component life.
Proper Warm-up/Cool-down: Follow manufacturer procedures to thermally condition the pump, minimizing thermal stress on components.
Avoid Dry Running: Never run the pump without adequate water supply and pressure. This causes catastrophic damage.
Monitor System Parameters: Pay close attention to pressure, temperature, flow rates, and any system alarms. Address anomalies immediately.
Follow Pressure Guidelines: Don’t constantly operate at the absolute maximum pressure unless necessary; it accelerates wear.
Maintenance:
Preventative Maintenance (PM) Schedule: Adhere rigorously to the manufacturer’s PM schedule. This includes regular oil changes (for HPUs), filter replacements (oil, water, air), accumulator pre-charge pressure checks, and inspections.
Seal Kits: High-pressure seals are wear items. Keep spares and replace them proactively based on operating hours or performance indicators (pressure drop, leaks). Proper installation is critical.
Check Valves: These critical components wear and require periodic inspection and replacement.
Fluid Analysis: Periodic analysis of hydraulic oil and coolant can reveal internal wear issues before they cause failures.
Training: Ensure operators and maintenance technicians are properly trained on the specific waterjet pump model.
Cleanliness: Keep the pump enclosure clean and free of debris that could clog filters or coolers.
Waterjet pumps are engineering marvels, transforming ordinary water into an incredibly powerful tool. From the dominant intensifier technology generating earth-shattering pressures to the increasingly capable direct drive systems offering smoother flow, these pumps are the undeniable power source enabling waterjet cutting’s unique advantages: cold cutting, material versatility, precision, and environmental friendliness. Understanding the different types of waterjet pumps, their core components, key performance metrics, vast applications, and critical maintenance requirements is essential for anyone looking to invest in waterjet technology or optimize their existing operations. As materials evolve and demands for precision and efficiency increase, the ongoing development of more powerful, reliable, efficient, and intelligent waterjet pumps will continue to push the boundaries of what’s possible in manufacturing and fabrication. Choosing the right pump and maintaining it meticulously ensures maximum productivity, cut quality, and return on investment for this transformative technology.
continue reading
Related Posts
- 1136 words5.7 min read
- 1322 words6.7 min read
- 1730 words8.8 min read