Waterjet Cutting Automotive
VICHOR’s Revolutionary Approach Transforming the Industry
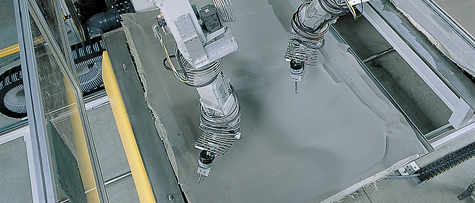
Introduction
VICHOR Waterjet: Leaders in Waterjet Technology
At VICHOR Waterjet, we leverage years of technological innovation and industry knowledge to create high-performing waterjet cutting solutions. Our commitment to quality has solidified our position as pioneers in the field of waterjet cutting technology. Our cutting-edge machinery, matched with an unwavering dedication to customer service, has garnered us a stellar reputation. We’re recognized for delivering top-notch performance in the most challenging production environments. We also stand as the only company offering a two-year warranty for our entire range of waterjet cutting machines, thereby ensuring peace of mind for our customers.
Waterjet Cutting in the Automotive Industry: A Synopsis
In the fast-paced, increasingly precise world of automotive manufacturing, waterjet cutting automotive parts has gained significant traction. This technology’s adaptability makes it a formidable tool in crafting a broad array of automotive components, from car panels and carpets to intricate engine parts. The automotive industry demands a blend of speed, efficiency, precision, and versatility – all of which are fulfilled by waterjet cutting. This cutting technique has become indispensable, contributing to increased productivity, minimal waste, and enhanced part quality.
Demystifying Waterjet Cutting Technology
Waterjet Cutting Explained
Waterjet cutting is a non-conventional machining process that employs the power of high-pressure water, either alone or infused with abrasive particles, to cut through materials. The precision of this method is unmatched, ensuring minimal material waste and reducing the need for secondary finishing processes. With no Heat-Affected Zones (HAZ) and no creation of noxious fumes or mechanical stresses, waterjet cutting automotive parts proves to be a superior, eco-friendly manufacturing solution.
Types of Waterjet Cutting: Pure and Abrasive
Waterjet cutting comes in two variations – pure and abrasive. Pure waterjet cutting, as the name suggests, uses only water under extreme pressure to cut through soft materials like foam, rubber, or textiles. It’s primarily used in the automotive industry for cutting headliners, door panels, and carpets.
On the other hand, abrasive waterjet cutting, a process we at VICHOR excel in, combines high-pressure water with a garnet abrasive. This combination enables the cutting of harder materials like steel, titanium, and composites. This is essential for the automotive industry as these materials form the backbone of several critical parts and components. The versatility of waterjet cutting technology truly shines with the ability to switch between pure and abrasive cutting based on the material, thus meeting a wide range of automotive manufacturing needs.
The Relevance of Waterjet Cutting in Automotive Manufacturing
Waterjet Cutting: The Versatile Solution
In the realm of automotive manufacturing, the demand for diversity in materials used is vast and ever-changing. From fabric elements like door panels and carpets to tougher materials like steel and composites, the versatility of waterjet cutting is perfectly suited to meet these demands. The ability to switch between pure water and abrasive waterjet cutting without changing the physical setup enhances the process’s adaptability. Moreover, the advanced software programming in VICHOR waterjet cutting machines allows a single cutting station to cut various parts without the need for physical changes in the setup, thereby making waterjet cutting a powerful solution in the automotive industry.
The Efficiency of Single Station Cutting
With VICHOR waterjet cutting machines, the efficiency of single station cutting is truly exemplified. Through the integration of high-tech software programming, a single cutting station can be customized to cut multiple different parts with nothing but a simple software modification. This dramatically reduces setup time and resources, thus leading to higher efficiency. The streamlined process results in less downtime, quicker turnaround times, and ultimately, higher productivity. In an industry as dynamic and fast-paced as automotive manufacturing, this efficiency is paramount.
Unpacking the Benefits of Waterjet Cutting for Automotive Applications
Heat-Affected Zones (HAZ): A Non-Issue with Waterjet Cutting
One of the significant advantages of waterjet cutting automotive parts is the absence of Heat-Affected Zones (HAZ). Traditional cutting methods that rely on heat often alter the material’s properties around the cut, potentially weakening the part. However, since waterjet cutting uses water or an abrasive-water mixture, it eliminates the risk of HAZ, thereby maintaining the material’s integrity.
A Cleaner, More Sustainable Cutting Process
Environmental sustainability is a growing concern in the manufacturing industry. Here, waterjet cutting shines as a cleaner, more sustainable solution. Since the process uses water and garnet abrasive, it generates no noxious fumes, unlike other cutting processes. Also, the lack of significant material waste contributes to more efficient material usage and less overall waste, making waterjet cutting an eco-friendlier choice.
Smooth, Burr-Free Cuts: The Waterjet Promise
The precision of waterjet cutting automotive parts does not stop at the cut itself. The process ensures that the cut surfaces are smooth, rough-edge, and burr-free. This not only enhances the aesthetics of the final product but also eliminates the need for secondary finishing processes, thus saving time and resources. With VICHOR Waterjet machines, manufacturers can expect consistently high-quality, ready-to-use parts right off the cutting table.
The VICHOR Waterjet Edge in Automotive Production
Mass Production Mastery with 6-Axis Robotics
For mass production in the automotive industry, our 6-Axis Robotics technology sets VICHOR Waterjet apart. Our systems have been fine-tuned to streamline the manufacturing process, delivering faster cutting speeds and greater flexibility. By integrating our waterjet cutting technology with robotics, we achieve efficient large-scale production without compromising on precision and quality.
Custom Automotive Parts: Crafted with VICHOR Waterjet
Aside from mass production, VICHOR Waterjet also thrives in the realm of crafting custom, one-of-a-kind automotive parts. Our waterjet cutting machines offer unparalleled precision and flexibility, making them ideal for producing custom parts. Whether for classic car restorations or for crafting unique performance parts, our waterjet cutting technology consistently delivers high-quality results.
Why Customers Trust VICHOR: Real Testimonials
At VICHOR, we believe our satisfied customers are our best advocates. We have a long track record of positive customer experiences, many of whom have shared their testimonials. These testimonials underscore our commitment to quality and our dedication to delivering top-notch customer service. The trust we’ve garnered from our clientele speaks volumes about the reliability and superiority of our waterjet cutting machines.
The VICHOR Advantage: Waterjet Cutting in Automotive Industry
Key Benefits of VICHOR Waterjet Cutting Technology
Our waterjet cutting technology offers several key benefits, which make it a premier choice in the automotive industry:
- Precision Cutting with Minimal Waste
With our machines, automotive manufacturers can achieve extremely narrow cutting kerfs, which allow for tighter nesting and ultimately result in less waste. The preciseness of waterjet cutting automotive components ensures optimal use of materials, contributing to cost-effectiveness and sustainability.
- Prototype Production: Quicker with Waterjet
In the world of automotive design and manufacturing, speed is essential. Our waterjet cutting technology accelerates prototype production, enabling faster design iterations and quicker time to market.
- Stress-Free Cutting: Preserving the Metal’s Integrity
Unlike traditional cutting methods, waterjet cutting does not induce mechanical stress on the material. This stress-free cutting preserves the metal’s structure and ensures the integrity of the parts being produced.
- Flexibility: A Hallmark of VICHOR Production Processes
Our waterjet cutting technology stands out for its flexibility. Whether cutting varying materials or different shapes and sizes, our machines adapt easily to meet diverse production needs. This flexibility enhances productivity and allows for the manufacture of a broader range of automotive components.
FAQ: Waterjet Cutting in Automotive Applications
What types of materials can VICHOR’s waterjet cutting machines handle in automotive manufacturing?
VICHOR’s waterjet cutting machines can handle a wide variety of materials used in automotive manufacturing. This includes, but is not limited to, steel, titanium, composites, and even soft materials such as headliners, door panels, and carpeting.
How does waterjet cutting reduce waste in automotive production?
Waterjet cutting, with its exceptional precision, can create extremely narrow cutting kerfs allowing for tighter nesting of parts. This efficient use of material dramatically reduces waste. Additionally, the process does not produce significant material waste or harmful emissions, contributing to its sustainability.
Can VICHOR’s waterjet cutting machines be used for both mass production and custom part fabrication?
Yes, our waterjet cutting machines are adept at both mass production and crafting unique, custom automotive parts. For large-scale production, we integrate our machines with 6-axis robotics for increased speed and flexibility. For custom parts, our machines deliver unmatched precision and adaptability, making them ideal for producing unique components.
What does a “Heat-Affected Zone” mean, and why is it important in cutting processes?
A Heat-Affected Zone (HAZ) is an area where the properties of a material have been altered due to the heat produced by traditional cutting methods. This can potentially weaken the part. Waterjet cutting, on the other hand, does not produce heat, eliminating the risk of HAZ and maintaining the integrity of the material.
Why should I choose VICHOR’s waterjet cutting machines for automotive manufacturing?
VICHOR’s waterjet cutting machines offer a range of benefits for automotive manufacturing. These include precision cutting with minimal waste, rapid prototype production, stress-free cutting, and flexibility in production processes. Additionally, VICHOR offers a two-year warranty for our machines, demonstrating our commitment to quality and customer satisfaction.
Conclusion
The Evolving Role of Waterjet Cutting in Automotive Production
In the fast-paced and evolving automotive industry, the role of waterjet cutting continues to grow. This technology’s adaptability, precision, and efficiency make it an invaluable asset for automotive production. Whether it’s mass-producing components with 6 axis robotics or crafting unique, custom parts, waterjet cutting is making significant inroads in the automotive manufacturing landscape.
VICHOR Waterjet: Your Go-to Partner for Automotive Waterjet Cutting
As a leader in waterjet cutting technology, VICHOR is poised to be your trusted partner in automotive manufacturing. Our advanced waterjet cutting machines, backed by a two-year warranty and a commitment to exceptional customer service, set us apart. We invite you to experience the VICHOR advantage – where innovation, quality, and service converge to deliver superior automotive waterjet cutting solutions. Trust VICHOR to drive your automotive production to new heights of precision and efficiency.