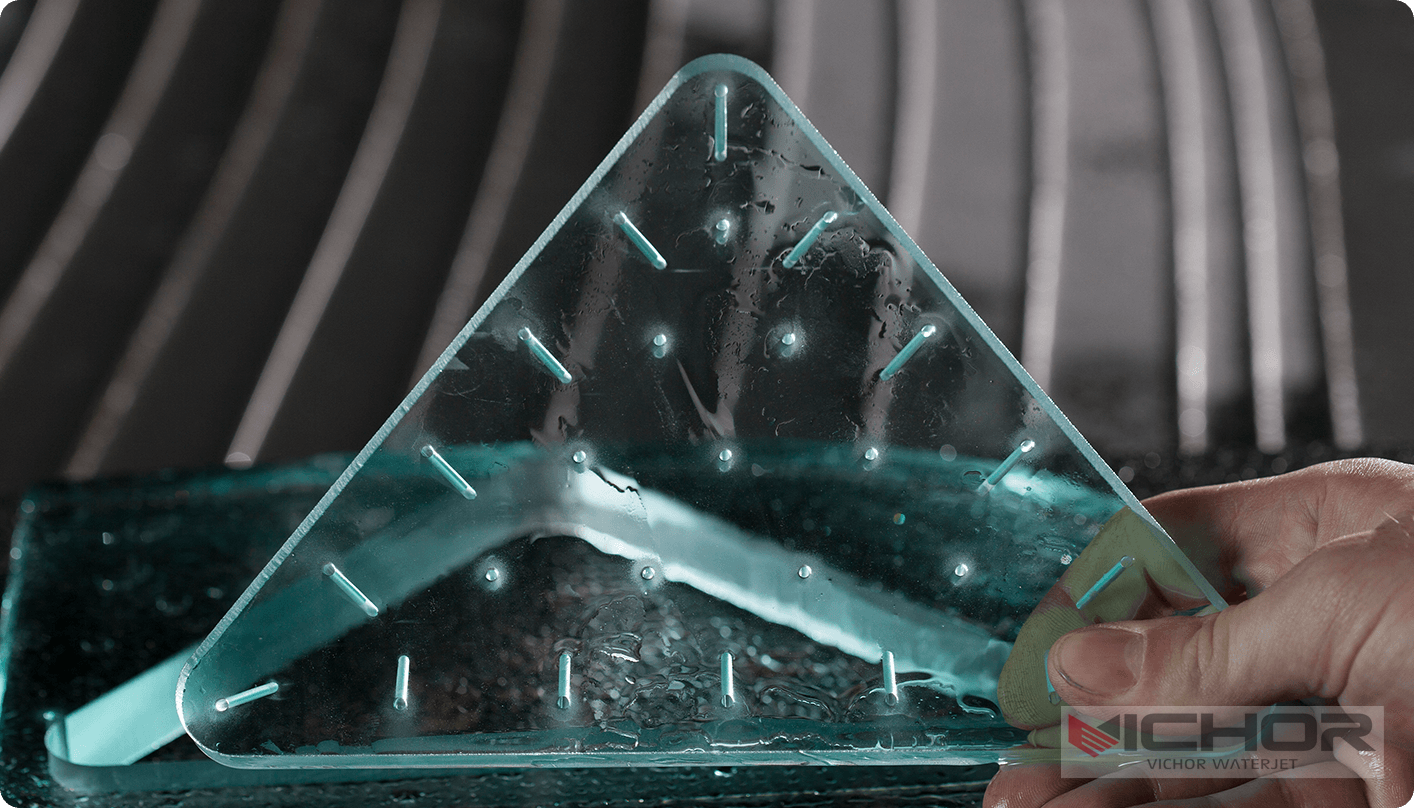
Water That Cuts Steel: The Ultimate Guide to Abrasive Waterjet Cutting Technology
Imagine slicing through inches of hardened steel, titanium, or delicate marble not with a fiery torch or a screaming saw, but with a precise, high-velocity stream of water that cuts steel. This isn’t science fiction; it’s the remarkable reality of Abrasive Waterjet (AWJ) cutting technology. This revolutionary process harnesses the power of water that cuts steel to perform intricate cuts on virtually any material without generating heat-affected zones or harmful fumes. Its versatility, precision, and eco-friendly nature have made it indispensable across countless industries. This comprehensive guide explores the fascinating world of water that cuts steel, delving into how it works, its unique advantages, diverse applications, and its future potential.
How Does Water Actually Cut Steel? The Core Technology Explained
The concept of water that cuts steel seems counterintuitive at first. Pure water alone, even under immense pressure, struggles to cut hard metals effectively. The true magic lies in the transformation of a high-pressure water stream into an abrasive slurry jet.
Ultra-High Pressure Generation: The process begins with an intensifier pump. This pump takes ordinary tap water (often filtered) and pressurizes it to extreme levels, typically between 30,000 PSI (2,000 bar) and 90,000 PSI (6,200 bar). To put this in perspective, a firehose operates around 300 PSI. This pressurized water is stored in accumulators to ensure a smooth, pulsation-free flow.
Focusing the Stream: The high-pressure water is forced through a tiny gemstone orifice (usually made of diamond or sapphire), narrowing its diameter to as little as 0.004 inches (0.1 mm). This transforms the pressurized water into an incredibly fast, coherent “pure” water jet, reaching speeds up to 2.5 times the speed of sound (Mach 2.5+).
Introducing the Cutting Edge – Abrasives: For cutting hard materials like steel, stone, or composites, pure water isn’t enough. This is where the water that cuts steel truly forms. In a mixing chamber located just downstream of the orifice, a precise amount of finely-ground abrasive garnet (a very hard mineral) is introduced into the supersonic water stream. The abrasive particles are entrained and violently accelerated by the water.
The Cutting Nozzle: The mixture of high-velocity water and abrasive particles then travels through a focusing tube (also called a mixing tube or nozzle), typically made of ultra-hard tungsten carbide. This tube further aligns and concentrates the abrasive slurry into a coherent cutting jet.
The Erosion Process: When this hypersonic stream of water that cuts steel impacts the target material, the accelerated abrasive particles perform the cutting through micro-mechanical erosion. Each particle acts like a microscopic chisel, literally sandblasting away tiny fragments of the material. The water serves three critical functions: accelerating the abrasives, removing the eroded debris from the cut (kerf), and cooling the cutting zone.
The Cutting Mechanism: Why Waterjet Works on Steel and Beyond
Understanding the mechanics behind water that cuts steel reveals its unique advantages:
Cold Cutting: Unlike laser, plasma, or oxy-fuel cutting, AWJ produces virtually no heat in the workpiece. There is no Heat-Affected Zone (HAZ), meaning the material’s original microstructure, hardness, and temper near the cut edge remain completely unchanged. This is critical for materials that warp, crack, or change properties with heat (e.g., hardened tool steel, aerospace alloys, tempered glass, certain plastics).
Mechanical Erosion Dominance: The cutting action relies purely on the kinetic energy of the abrasives eroding the material particle by particle. This makes AWJ effective on almost any material – metals (steel, aluminum, titanium, copper), stone, glass, ceramics, composites, rubber, plastics, foam, and even food products. The hardness of the material primarily determines the cutting speed and abrasive consumption rate, not its electrical conductivity or optical properties.
Kerf Characteristics: The cut width (kerf) is relatively small, typically ranging from 0.020″ to 0.050″ (0.5mm to 1.3mm) depending on the nozzle size and material thickness. The cut edge usually has a matte finish with a slight taper (wider at the top than the bottom). Modern machines can compensate for this taper. The edge quality is generally very good, often requiring little to no secondary finishing for many applications.
Minimal Force: The cutting head exerts very little lateral force on the workpiece, allowing for the cutting of delicate or thin materials without distortion and enabling intricate shapes to be cut from material held only by thin tabs.
Key Advantages of Using Water That Cuts Steel
The unique characteristics of abrasive waterjet technology translate into significant benefits for manufacturers and fabricators:
Unmatched Material Versatility: This is arguably the biggest strength. A single machine equipped with water that cuts steel can seamlessly switch between cutting 6-inch thick titanium, delicate circuit boards, fragile stone inlays, layered composites, and food items like cakes or frozen fish – all without changing the fundamental cutting tool, only the abrasive feed rate and potentially the nozzle size.
No Heat-Affected Zone (HAZ): As emphasized, the cold cutting nature preserves material integrity. This eliminates warping, hardening, softening, or micro-cracking near the cut edge, saving costs on post-processing and ensuring the structural integrity of critical components.
Exceptional Precision and Complexity: Modern CNC-controlled AWJ machines achieve remarkable positional accuracy (often within +/- 0.001″ or 0.03mm) and repeatability. They excel at cutting intricate contours, sharp corners, and complex geometries that are difficult or impossible with other thermal or mechanical methods. The narrow kerf minimizes material waste.
Environmentally Friendly: The process uses water and natural garnet abrasive (non-toxic). It generates no hazardous fumes, gases, or molten spatter (like plasma or laser). The waste stream is primarily water mixed with eroded material and spent abrasive, which can often be filtered and recycled or disposed of safely. Noise levels are generally lower than many other cutting processes.
Minimal Set-Up and Fixturing: Due to the low cutting forces, parts often require only simple fixturing or can even be stacked or nested closely, maximizing material utilization. No special clamps to counteract thermal distortion are needed.
Ability to Cut Thick Materials: AWJ can effectively cut very thick materials (steel plates exceeding 12 inches/300mm are possible), where lasers struggle with beam divergence and plasma loses cut quality.
Where is Water That Cuts Steel Used? Diverse Industrial Applications
The versatility and advantages of water that cuts steel have led to its adoption across a vast spectrum of industries:
Aerospace & Defense: Cutting high-strength alloys (titanium, Inconel), aluminum structures, composites (carbon fiber, fiberglass), honeycomb panels, and intricate engine components without compromising material properties or inducing stress. Prototyping complex parts is common.
Automotive: Manufacturing gaskets, interior trim (textiles, leather, foam), fiberglass body parts, composite components, insulation materials, and prototyping parts. Cutting various materials on the same line is a major advantage.
Machine Tool & General Fabrication: Producing parts from plate steel, stainless steel, aluminum, brass, and copper. Creating gears, flanges, brackets, tools, dies, and molds. Ideal for one-off prototypes, small batches, and large-scale production.
Architecture, Art, & Stoneworking: Cutting intricate designs in marble, granite, slate, glass, and decorative metals for countertops, flooring, sculptures, signage, wall art, and building facades. The ability to cut thick stone without chipping is crucial.
Electronics: Precisely cutting circuit boards (PCBs), laminates, insulators, and thin metals without thermal damage that could destroy sensitive components.
Glass & Ceramics: Cutting thick or laminated glass, bulletproof glass, ceramic tiles, and technical ceramics (e.g., alumina, silicon carbide) without cracking or thermal stress.
Food Industry: Cutting frozen foods, baked goods, poultry, fish, and other products hygienically (using food-grade garnet or other approved abrasives, and often pure waterjet) without crushing or generating heat that cooks the product.
Medical Device Manufacturing: Cutting biocompatible materials like titanium for implants, surgical instruments, and intricate components from plastics and composites, all with high precision and no thermal degradation.
Understanding the Limitations and Considerations
While water that cuts steel is incredibly powerful, it’s essential to understand its limitations:
Cutting Speed vs. Thermal Methods: AWJ is generally slower than plasma or laser cutting for thinner sections of mild steel. While speeds have increased dramatically, productivity for high-volume, simple shapes in thin metal might favor thermal processes. However, for thicker materials, complex shapes, or sensitive materials, AWJ often becomes competitive or faster overall when factoring in secondary operations eliminated by the lack of HAZ.
Abrasive Cost and Consumption: Garnet abrasive is a significant operational cost. Consumption rates depend on material hardness, thickness, and desired cut quality. Efficient abrasive delivery systems and recycling initiatives help manage this cost.
Kerf Taper: As mentioned, the cut naturally has a slight taper. While modern dynamic head control (tilting the nozzle) can produce near-vertical edges, it adds complexity. For many applications, the inherent taper is acceptable.
Edge Finish: While good, the AWJ edge has a characteristic “striated” or matte finish caused by the abrasive action. It’s different from a machined or laser-cut edge. For applications requiring a perfectly smooth edge, secondary finishing might be necessary, though often less intensive than after thermal cutting.
Noise and Water Management: Although cleaner than many processes, AWJ operation generates significant noise (requiring enclosures) and produces a slurry waste stream that needs proper collection, filtration, and disposal/recycling systems.
Initial Investment: High-pressure pumps and precision motion systems make AWJ machines a significant capital investment, though operating costs can be favorable depending on the application mix.
The Future of Water That Cuts Steel: Trends and Innovations
The technology of water that cuts steel continues to evolve rapidly:
Higher Pressures: Pumps capable of 100,000+ PSI are being developed and deployed. Higher pressure translates directly to faster cutting speeds, especially in thicker materials, and potentially finer cuts.
Enhanced Precision & Dynamics: Advances in CNC controls, motion systems (linear motors), and dynamic head articulation (5-axis cutting) enable even more complex 3D shapes with improved accuracy and reduced taper.
Intelligent Cutting: Integration of machine vision for automatic part recognition, in-process quality monitoring (measuring kerf width, detecting nozzle wear), and adaptive cutting parameters based on real-time sensor feedback.
Software Optimization: Smarter nesting algorithms to maximize material yield, improved path planning for faster cutting and better edge quality, and simulation software to predict outcomes.
Reduced Operating Costs: Developments in longer-lasting orifices and mixing tubes, more efficient abrasive delivery and recovery systems, and water recycling technologies aim to lower the cost per part.
Hybrid Technologies: Exploring combinations, such as using a low-power laser to pre-heat or weaken a material just ahead of the waterjet stream, potentially increasing cutting speeds for specific challenging materials.
New Abrasives & Methods: Research into alternative abrasives offering different performance characteristics or lower costs, and techniques like abrasive slurry jet (ASJ) for specialized applications.
Water that cuts steel is far more than an intriguing novelty; it’s a sophisticated, versatile, and indispensable manufacturing technology. Abrasive Waterjet cutting harnesses the immense power of ultra-high-pressure water and abrasive particles to machine materials with unparalleled flexibility, precision, and crucially, without heat damage. From the toughest aerospace alloys to the most delicate pastries, its applications span the entire industrial spectrum. While considerations like speed relative to thermal processes and abrasive costs exist, the unique benefits – particularly cold cutting and material versatility – make it the optimal or often the only feasible solution for countless cutting challenges. As pressure increases, controls become smarter, and efficiency improves, the future of water that cuts steel promises even greater capabilities, solidifying its role as a cornerstone of modern fabrication. Whether you’re an engineer, artist, or manufacturer, understanding this remarkable technology opens doors to innovative design and production possibilities.
continue reading
Related Posts
- 1631 words8.3 min read
- 1917 words9.7 min read