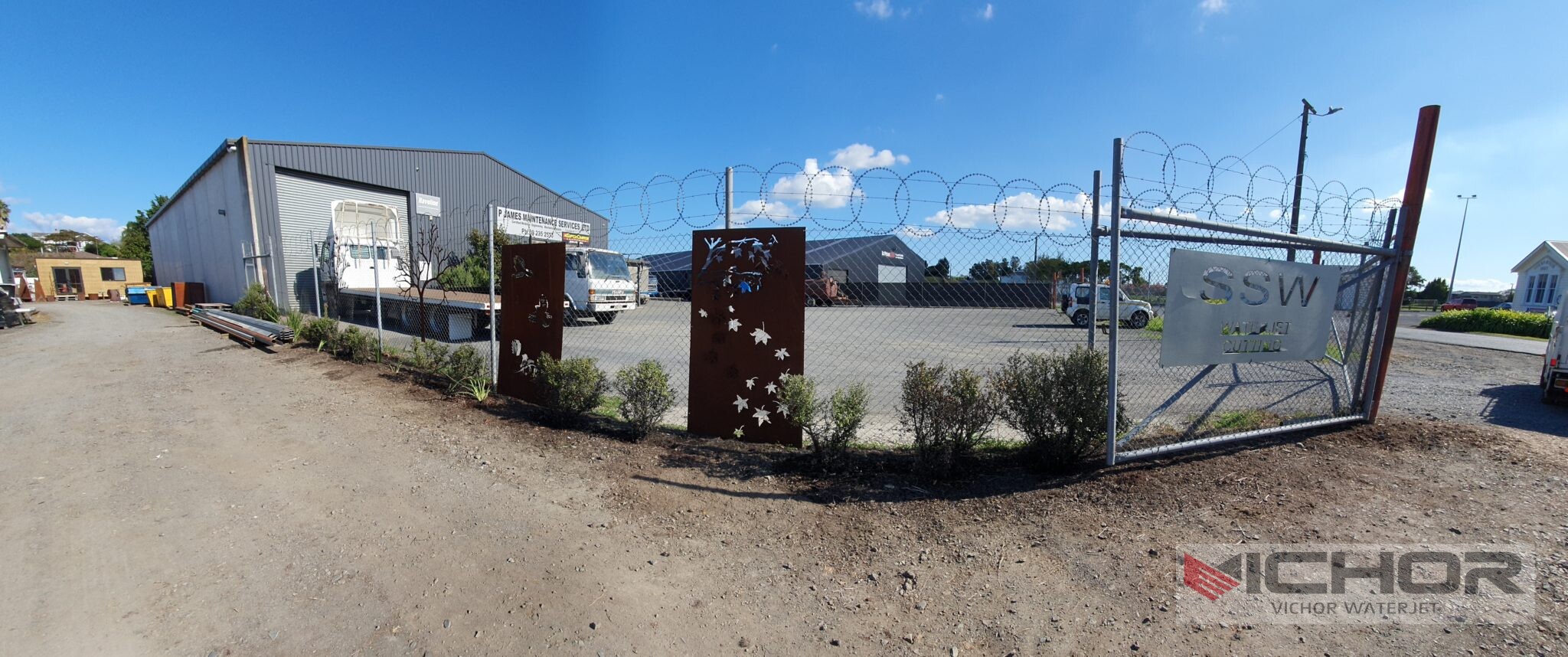
Water Laser Jet Technology: Revolutionizing Precision Machining and Cutting Applications
The relentless pursuit of precision, efficiency, and versatility in material processing has driven remarkable innovations. Among the most fascinating and impactful is Water Laser Jet technology. This sophisticated hybrid approach marries the unparalleled accuracy of laser energy with the unique benefits of a controlled water stream. Far from being a mere novelty, Water Laser Jet systems represent a significant leap forward, particularly for challenging materials and intricate applications where traditional laser cutting or pure waterjet methods fall short. This comprehensive guide delves into the intricacies of Water Laser Jet technology, exploring its principles, advantages, components, applications, and critical considerations for adoption.
What is Water Laser Jet Technology?
At its core, Water Laser Jet technology (often referred to as Water-Jet Guided Laser or Laser MicroJet®) is a hybrid machining process. It involves focusing a high-power laser beam (typically pulsed Nd:YAG or fiber lasers) into the core of a precisely formed, ultra-thin, high-pressure water jet. This water jet acts as both a waveguide and a coolant medium. The laser beam undergoes total internal reflection within the water jet, similar to how light travels through an optical fiber, guiding it directly to the workpiece with exceptional stability and minimal divergence. This creates a unique processing tool: a coherent, high-energy laser beam delivered within a coherent, high-velocity water column. The Water Laser Jet process thus leverages the benefits of both laser ablation and waterjet cutting, but in a synergistic way distinct from either standalone technology.
The Core Principles: How Water Laser Jet Works
Understanding the fundamental mechanics is key to appreciating the Water Laser Jet’s capabilities:
Laser Generation: A high-power pulsed laser generates the energy source.
Water Jet Formation: Ultra-pure, deionized water is pressurized (typically 500-1000 bar) and forced through a precisely engineered diamond nozzle (diameters ranging from 25 to 150 microns), creating a stable, laminar, high-velocity jet.
Beam Coupling & Waveguiding: The laser beam is focused directly into the entrance of the forming water jet. Due to the difference in refractive index between air and water, the laser light undergoes total internal reflection along the water-air interface of the jet. This confines the laser energy within the water column over distances of several centimeters without significant divergence or power loss.
Material Interaction: When the guided laser beam within the Water Laser Jet strikes the workpiece, the intense laser energy ablates or vaporizes the material at the point of contact.
Water’s Role: Simultaneously, the surrounding water jet performs crucial functions:
Cooling: It rapidly quenches the heat-affected zone (HAZ), minimizing thermal damage, recast layers, and micro-cracking – a major limitation of conventional lasers on sensitive materials.
Debris Removal: It efficiently flushes away molten material and ablation debris from the cut kerf, preventing redeposition and ensuring clean cuts and holes.
Confinement & Stability: The water jet physically confines the processing zone, enhances process stability, and suppresses plasma formation that can absorb laser energy in air.
This elegant combination is the essence of the Water Laser Jet process.
Key Advantages of Water Laser Jet Technology
The Water Laser Jet system offers a compelling set of benefits that address limitations of both pure laser and pure waterjet cutting:
Minimal Heat Affected Zone (HAZ): This is arguably the most significant advantage. The intense, localized cooling effect of the water jet surrounding the laser interaction zone drastically reduces thermal diffusion. This is critical for processing thermally sensitive materials like semiconductors (silicon, gallium arsenide), certain ceramics, thin metals, composites, and heat-treated components, where conventional lasers cause cracking, delamination, or altered material properties.
Exceptional Precision and Edge Quality: The stable, waveguide-like delivery of the laser beam within the water jet enables remarkably precise machining. Kerf widths are extremely narrow (comparable to the water jet diameter), and feature sizes down to tens of microns are achievable. Cut edges are typically clean, sharp, and free of burrs, slag, or significant recast layers.
No Tool Wear: Unlike mechanical machining tools (drills, end mills) or abrasive waterjet nozzles, the Water Laser Jet uses a non-contact process. The diamond nozzle is highly wear-resistant against pure water, and the laser beam itself doesn’t degrade. This eliminates downtime for tool changes and ensures consistent quality over long production runs.
Ability to Cut Complex and Brittle Materials: The combination of precise energy delivery and minimal thermal stress makes Water Laser Jet uniquely suited for materials notoriously difficult to machine cleanly with other methods. This includes:
Brittle ceramics and crystals (Al2O3, AlN, SiC, Sapphire, Glass)
Hardened metals and alloys
Thin foils and laminates (metals, polymers)
Composite materials (CFRP, GFRP) without delamination
Semiconductors (Si wafers, GaAs, InP)
Sensitive polymers and medical device materials
Reduced Mechanical Stress: While pure abrasive waterjet generates significant impact force, the Water Laser Jet process relies primarily on laser ablation. The water jet’s force is much lower, minimizing mechanical stress on delicate or thin workpieces, preventing deformation or breakage.
Clean and Dry Process (Mostly): The process generates minimal debris compared to dry laser cutting, as the water jet captures most particles. The water evaporates quickly after machining, often leaving parts relatively dry and clean,
reducing post-processing needs. Components of a Water Laser Jet System
A sophisticated Water Laser Jet system integrates several key subsystems:
Laser Source: Pulsed Nd:YAG lasers were historically common due to their pulse control and wavelength absorption characteristics. Modern systems increasingly utilize high-power pulsed fiber lasers, offering greater efficiency, reliability, and beam quality. Laser power typically ranges from 50W to over 500W.
High-Pressure Water System: This includes:
Water Purification Unit: Produces ultra-pure, deionized water (resistivity > 15 MΩ·cm) to prevent nozzle clogging and ensure stable jet formation and optimal laser transmission.
High-Pressure Pump: Generates the extreme pressure (500-1000+ bar) needed for the micronozzle. Intensifier pumps are standard.
Pulsation Dampeners: Ensure smooth, stable water pressure delivery.
Nozzle Assembly: The heart of the system. Features a high-precision diamond orifice (25µm to 150µm diameter) mounted in a robust nozzle body. Precise alignment of the laser beam into the forming water jet is critical and achieved via micro-positioning stages.
Beam Delivery and Focusing Optics: Guides the laser beam from the source to the nozzle entrance with minimal loss and focuses it precisely into the water jet. Fiber delivery is common with fiber lasers.
Motion Control System: High-precision CNC stages (X-Y-Z, often with rotary axes) position the workpiece or the nozzle assembly relative to each other with micron-level accuracy to execute complex machining paths.
Control System: Sophisticated software integrates laser control (power, pulse frequency, duration), water pressure control, motion control, and process monitoring. User interfaces allow programming of complex jobs and recipe management.
Catch Tank & Filtration: Collects the spent water and debris mixture. Filtration systems recycle the water for reuse, improving sustainability and reducing operating costs.
Major Industrial Applications
The unique capabilities of Water Laser Jet technology have opened doors in demanding sectors:
Semiconductor & Electronics Manufacturing:
Singulation (dicing) of compound semiconductors (GaAs, InP, GaN) wafers where low thermal stress is paramount to prevent cracking and preserve die strength.
Precision cutting of silicon wafers, particularly thick wafers or those with sensitive structures.
Trimming resistors, capacitors, and other components on substrates.
Drilling micro-vias in PCBs and substrates.
Cutting flexible circuits (FPC).
Medical Device Manufacturing:
Precision cutting of stents (metal and polymer) with minimal HAZ and burr-free edges critical for biocompatibility.
Machining intricate features in surgical instruments.
Cutting bio-absorbable polymers and sensitive implant materials.
Creating micro-fluidic channels in lab-on-a-chip devices.
Aerospace & Defense:
Machining high-strength, heat-sensitive alloys (e.g., Inconel, Titanium) for engine components.
Cutting composites (CFRP, GFRP) without delamination or fiber pull-out for airframe parts.
Processing ceramic thermal barrier coatings (TBCs).
Automotive:
Precision cutting of airbag initiator foils.
Machining fuel injector components.
Cutting gaskets and seals from advanced materials.
Processing sensors and electronic components.
Solar & Photovoltaic:
Edge deletion (insulation scribing) on solar cells.
Cutting thin-film solar panels.
Structuring silicon wafers.
Precision Engineering & Tooling:
Fabricating micro-molds and inserts.
Cutting hard metals and ceramics for wear parts.
Creating fine meshes and screens.
Drilling micro-holes in nozzles and filters.
Considerations and Implementation Factors
While powerful, Water Laser Jet technology requires careful consideration:
Capital Investment: Systems represent a significant capital expenditure, typically higher than comparable conventional lasers or waterjets due to their complexity (high-pressure water, pure water, precision nozzles, laser).
Operating Costs: Consumables include ultra-pure water (though recycled), electricity for laser and pump, and periodic nozzle replacement/reconditioning (diamond nozzles are durable but not immortal). Maintenance requires specialized expertise.
Material Thickness Limitations: Primarily suited for thin materials (generally < 2mm, though capable up to several mm depending on material and laser power). It is not a solution for thick-section cutting like traditional abrasive waterjet.
Cutting Speed: Material removal rates are generally lower than high-power conventional lasers on thick materials or pure abrasive waterjets. Speed is highly material and thickness-dependent. It excels in precision, not bulk removal.
Process Development: Optimizing parameters (laser power, pulse settings, water pressure, nozzle diameter, traverse speed) for a specific material and desired outcome requires expertise and experimentation. Process development is crucial.
Nozzle Alignment and Maintenance: Maintaining perfect laser beam alignment into the micronozzle is critical for stable process performance and requires precise mechanisms and procedures. Nozzle inspection and cleaning are essential maintenance tasks.
Water Handling: Requires infrastructure for ultra-pure water generation and handling of wastewater containing ablated material particles, necessitating filtration and potentially waste disposal considerations.
Water Laser Jet technology stands as a remarkable testament to engineering ingenuity, overcoming inherent limitations of standalone laser and waterjet processes. By harnessing the precision of a laser beam guided and cooled by a coherent water jet, it delivers unparalleled results in applications demanding minimal thermal damage, exceptional precision, and the ability to process fragile or complex materials. From the intricate world of semiconductor dicing to the life-saving precision of medical stents and the demanding environments of aerospace, the Water Laser Jet has carved out a vital niche. While considerations like cost and material thickness limitations exist, its unique advantages make it an indispensable tool for manufacturers pushing the boundaries of precision engineering and material processing. As laser and control technologies continue to advance, the capabilities and reach of Water Laser Jet systems are poised to expand further, solidifying their role in the future of high-precision manufacturing.
continue reading