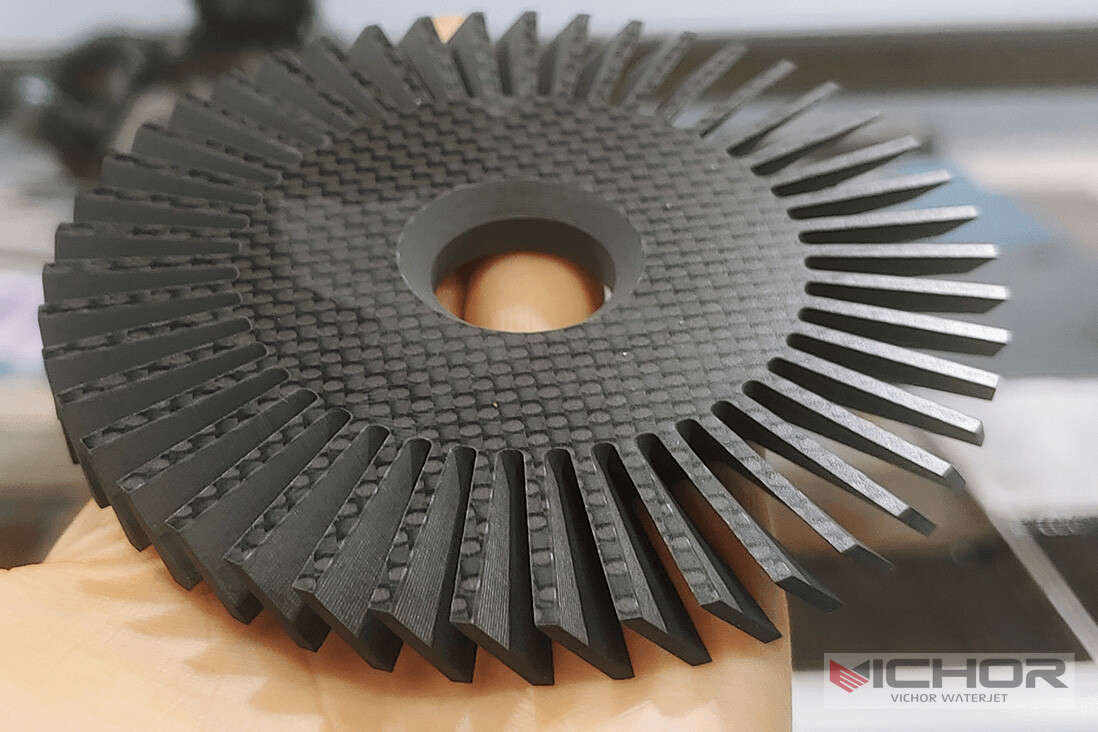
Water Jet Stone Carving: The Ultimate Guide to Precision, Versatility & Artistic Freedom
The world of stone carving, an art form millennia old, has undergone a quiet revolution. Gone are the days where intricate designs and complex shapes were solely the domain of chisels, hammers, and years of master craftsmanship. Enter water jet stone carving, a technology harnessing the incredible power of high-pressure water and abrasives to cut, carve, and shape stone with astonishing precision and flexibility. This comprehensive guide delves deep into the world of water jet stone carving, exploring its technology, advantages, capabilities, applications, and future potential.
What is Water Jet Stone Carving? (The Core Technology
At its heart, water jet stone carving is a subtractive manufacturing process. It utilizes an ultra-high-pressure pump (often generating pressures of 60,000 PSI or more) to force water through a tiny orifice (typically a diamond or sapphire nozzle), creating a supersonic stream. For cutting hard materials like stone, an abrasive material – usually finely ground garnet – is introduced into this high-velocity water stream within a mixing chamber. The abrasive particles are accelerated to incredible speeds, transforming the water stream into an immensely powerful cutting tool.
The Cutting Action: This abrasive-laden stream impacts the stone surface with tremendous kinetic energy. The abrasive particles microscopically erode the material, effectively “sanding” or “milling” away the stone particle by particle along a precisely controlled path dictated by Computer Numerical Control (CNC) software. Think of it as an incredibly precise, high-powered sandblaster moving with robotic accuracy.
The CNC Factor: The water jet stone carving head is mounted on a sophisticated CNC gantry system. This system interprets digital design files (like CAD drawings or vector art) and moves the cutting head along the X, Y, and sometimes Z axes with micron-level precision. This digital control is what unlocks the unparalleled accuracy and repeatability of the process. The lack of heat generation is another critical differentiator.
Key Advantages of Water Jet Stone Carving Over Traditional Methods
Why choose water jet stone carving? Its benefits are numerous and significant, particularly for modern design and fabrication demands:
Unmatched Precision and Accuracy: CNC-guided water jet stone carving achieves tolerances as tight as ±0.1 mm (±0.004 inches). This level of accuracy is virtually impossible to replicate consistently with manual carving or even many other mechanical cutting tools, especially for intricate designs and complex geometries. Edges are clean and sharp.
Zero Heat-Affected Zone (HAZ): Unlike laser cutting or plasma cutting, the water jet stone carving process is cold-cutting. There is no heat generated at the cut line. This is absolutely crucial for stone:
Prevents Thermal Stress Cracking: Stone is brittle and susceptible to cracking from sudden temperature changes. Water jet eliminates this risk entirely.
Preserves Material Integrity: No heat means the inherent strength, color, and crystalline structure of the stone adjacent to the cut remain completely unaffected. No hardened edges or micro-fractures caused by heat.
Material Versatility: A single water jet stone carving machine can handle an astonishingly wide range of natural and engineered stones:
Natural Stone: Granite, Marble, Limestone, Travertine, Slate, Sandstone, Onyx, Quartzite, Soapstone, Basalt.
Engineered Stone: Quartz (like Silestone, Caesarstone, Cambria), Porcelain Slabs, Terrazzo, Sintered Stone (Neolith, Dekton, Lapitec).
Thickness Capacity: Modern water jets can cut stone slabs from thin veneers (3mm) up to impressive thicknesses of 150mm (6 inches) or even more, depending on the machine’s power and the stone type.
Design Freedom and Complexity: This is where water jet stone carving truly shines. The narrow kerf (cut width, typically 0.8mm to 1.5mm with abrasives) and the ability of the waterjet head to maneuver in any direction allow for:
Intricate Details: Cutting incredibly fine details, delicate lace-like patterns, complex logos, and lettering that would be prohibitively expensive or impossible with other methods.
Sharp Corners and Internal Cuts: Achieving true sharp inside corners (no radius limitations like routers) and easily creating internal cutouts without the need for starter holes (the jet can pierce the material).
True Contouring: Effortlessly cutting complex curves, arcs, and 3D bevels in a single pass.
No Tooling Changes: Unlike milling machines that require different bits for different operations, the water jet cuts everything with the same abrasive stream, streamlining production.
Minimal Material Waste & Efficiency: The narrow kerf translates directly to less material consumed compared to wider blade cuts. Nesting software optimizes the placement of parts on a slab, maximizing material yield. The CNC automation also allows for unattended operation, including overnight cutting, boosting productivity for batch jobs.
Clean and Environmentally Friendlier Process: The cutting process primarily uses water and natural garnet abrasive (an inert mineral). While slurry (water, abrasive, and stone dust) is generated, it can be collected, settled, and often recycled or disposed of more responsibly than coolants or cutting oils used in machining. Dust generation is also significantly lower than sawing or grinding.
Unleashing Creativity: Design Possibilities with Water Jet Stone Carving
The design flexibility afforded by water jet stone carving has opened new frontiers in architectural and artistic stonework:
Custom Inlays and Mosaics: Precise cutting allows for intricate inlays of different stone types or materials (like metal or glass) into a stone base, creating stunning visual contrasts and patterns. Perfect for medallions, logos, borders, and artistic floors/walls.
Decorative Panels and Screens: Creating elaborate pierced stone screens (jalis), decorative wall panels, room dividers, and balustrades with complex geometric or organic patterns. Water jet stone carving makes these feasible and reproducible.
Signage and Lettering: High-precision cutting of dimensional letters, logos, house numbers, and memorial plaques in any font or design, with crisp edges and fine details.
Furniture and Bespoke Elements: Crafting unique tabletops, countertops with integrated drainboards or complex edge profiles, fireplace surrounds, sculptural bases, and other high-end architectural features.
Artistic Sculpture and Reliefs: While not replacing the artist’s hand for freeform sculpture, water jets excel at producing complex bas-reliefs, intricate components for larger installations, and precisely shaped pieces based on digital models.
Technical Components: Manufacturing precise stone parts for machinery bases, scientific instruments, or specialized industrial applications where stone’s properties are beneficial.
Material Considerations: Which Stones Work Best?
While water jet stone carving is remarkably versatile, the characteristics of the stone do influence the process and results:
Hardness: Generally, harder stones like granite, quartzite, and engineered quartz cut well but may require slightly slower speeds or more abrasive. Softer stones like marble, limestone, and travertine cut faster. Extremely hard stones may approach the practical limits of the technology in terms of cutting speed for very thick sections.
Homogeneity: Stones with consistent mineral composition and structure (like many granites and engineered quartz) cut most predictably and cleanly. Stones with significant veining, voids, or varying hardness (some marbles, travertine) can sometimes cause minor deflection of the jet or require adjustments to cutting parameters. Proper fixturing is crucial.
Thickness: Cutting speed decreases significantly as thickness increases. While thick cuts (100mm+) are possible, they require powerful pumps, optimized parameters, and patience. Edge taper (a slight widening of the kerf towards the bottom) also becomes more noticeable in very thick materials but can be compensated for in programming.
Surface Finish: The water jet stone carving process leaves a characteristic matte, slightly textured finish on the cut edge – often described as a “natural sandblasted” look. This is desirable for many applications. If a polished edge is required, the water jet cut provides a perfectly accurate base for subsequent polishing operations.
Applications Across Industries
Water jet stone carving finds diverse applications:
Architecture & Interior Design: Custom countertops, backsplashes, feature walls, flooring inlays, decorative panels, fireplace surrounds, stair treads, intricate cladding elements, signage.
Monumental & Memorial: Highly detailed headstones, memorial plaques, cremation niches, complex lettering and emblems, custom shapes in durable granite.
Art & Sculpture: Creating components for installations, precise geometric sculptures, public art pieces, intricate bas-reliefs, custom bases.
Furniture Design: Unique tables, benches, reception desks, shelving with integrated stone elements, sculptural pieces.
Landscaping & Exterior: Decorative stone elements for gardens, water features, complex paving patterns, custom pool coping.
Retail & Hospitality: High-impact store fixtures, branded elements for hotels and restaurants, luxurious bar tops, reception areas.
Choosing a Water Jet Stone Carving Service Provider
Selecting the right partner is key to a successful project:
Experience & Expertise: Look for proven experience specifically in water jet stone carving with the type of stone and complexity of design you require. Ask for a portfolio.
Technology: Inquire about their machine capabilities (maximum pressure, cutting bed size, Z-axis capability for bevels), software proficiency (CAD/CAM), and maintenance standards. Modern, well-maintained equipment is crucial.
Design Support: Can they assist with file preparation, design optimization for water jetting, and troubleshooting potential issues? Good communication is essential.
Material Sourcing & Handling: Do they offer material sourcing? How do they handle and transport large, heavy slabs? What is their process for minimizing breakage?
Finishing Capabilities: Do they offer secondary services like polishing cut edges, honing, or sealing, or will you need to arrange this separately?
Quality Control: Understand their process for ensuring dimensional accuracy and quality checks throughout production.
Project Management & Communication: Ensure they are responsive, provide clear timelines and cost estimates, and keep you informed.
The Future of Water Jet Stone Carving
The technology continues to evolve, promising even greater capabilities:
Increased Power and Speed: Higher pressure pumps and more efficient abrasive delivery systems will enable faster cutting of thicker materials.
Enhanced Precision & 5-Axis Cutting: Wider adoption of 5-axis heads will allow for more complex 3D shapes and undercuts directly from the water jet, pushing the boundaries of sculptural forms possible through water jet stone carving.
Smarter Software: Advancements in CAD/CAM software will improve nesting efficiency, predictive cutting models for different stones, automatic taper compensation, and simulation to prevent errors.
Improved Abrasive Recovery & Sustainability: More efficient closed-loop systems for abrasive recovery and recycling will reduce waste and operational costs, enhancing the environmental profile.
Integration with Other Technologies: Combining water jet cutting with robotic polishing or assembly systems for more automated production lines.
Water jet stone carving is far more than just a cutting tool; it’s a transformative technology that has redefined the boundaries of what is possible with stone. Its unparalleled precision, cold-cutting nature, immense design freedom, and material versatility make it the go-to solution for architects, designers, artists, and fabricators seeking to push the envelope. From breathtaking architectural features and intricate inlays to durable memorials and unique sculptures, water jet stone carving unlocks a world of creative potential within solid stone. As the technology continues to advance, its role in shaping the future of stone design and fabrication is assured, enabling ever more complex, beautiful, and innovative applications. Whether for a simple custom countertop cutout or a monumental artistic installation, water jet stone carving offers a blend of accuracy, flexibility, and quality that traditional methods simply cannot match.
continue reading