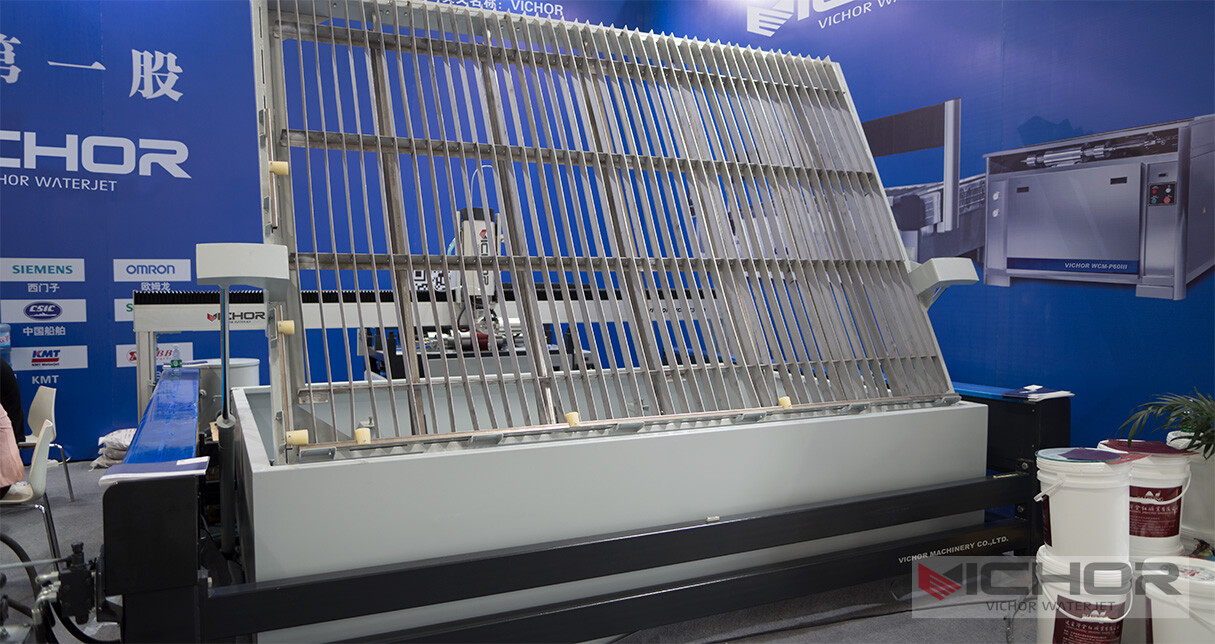
Water jet for Industrial: Powering Precision & Versatility in Modern Manufacturing
In the demanding world of modern manufacturing and fabrication, the quest for efficient, precise, and versatile material processing solutions is relentless. Among the most powerful tools answering this call is water jet for industrial applications. Far more than just high-pressure water, industrial waterjet technology harnesses the immense kinetic energy of water, often mixed with abrasive particles, to cut, shape, and machine an astonishingly wide array of materials with exceptional precision and minimal thermal or mechanical stress. This comprehensive guide delves deep into the world of water jet for industrial use, exploring its core technology, unparalleled advantages, diverse applications, and critical considerations for implementation.
1. The Core Technology: How Industrial Waterjets Work
At the heart of every water jet for industrial cutting system lies a simple yet profoundly powerful principle: converting pressurized water into a focused, high-velocity stream. This process involves several key components:
High-Pressure Pump: The powerhouse of the system. Utilizing either intensifier pump technology (creating pressure hydraulically) or direct-drive pumps (using crankshafts), these pumps generate pressures typically ranging from 40,000 PSI (2,750 bar) to over 90,000 PSI (6,200 bar) for abrasive cutting.
Water Filtration & Preparation: Pure water is essential. Multi-stage filtration removes impurities and minerals that could damage pumps and nozzles. Water is then pressurized.
Intensifier/Accumulator: Intensifier pumps use hydraulic oil acting on a large piston to drive a smaller piston pressurizing the water. Accumulators smooth out pressure pulses for a consistent jet.
Cutting Head & Nozzles: Pressurized water passes through a small orifice (typically made of diamond or sapphire) in the cutting head, forming a coherent, supersonic stream. For cutting hard materials, abrasive garnet is introduced into a mixing chamber within the head, entrained by the water stream, and focused through a longer mixing tube (also called a focus tube or nozzle). Pure water jets use just the orifice.
Motion Control System: Advanced CNC (Computer Numerical Control) systems precisely move the cutting head along the X, Y, and Z axes (and often include rotational A/B axes for complex 3D cutting) according to programmed designs. Accuracy and repeatability are measured in thousandths of an inch or hundredths of a millimeter.
Catch Tank: Positioned below the cutting table, this tank absorbs the energy of the spent jet and collects the water, abrasive, and cut material particles (swarf) for separation and disposal/recycling.
The synergy of ultra-high pressure and precise motion control makes water jet for industrial tasks a uniquely capable technology.
2. Unparalleled Material Versatility: Cutting (Almost) Anything
Perhaps the most significant advantage driving the adoption of water jet for industrial systems is their extraordinary material versatility. Unlike thermal processes limited by melting points or conductivity, waterjets cut via mechanical erosion, making them effective on:
Metals: Steel (mild, tool, stainless, armor plate), aluminum, copper, brass, titanium, inconel, tungsten, bronze, lead. Thicknesses from foil to over 12 inches (300mm+) are achievable.
Stone & Tile: Granite, marble, slate, limestone, engineered stone, porcelain tile, ceramic tile. Ideal for intricate countertops, signage, and architectural elements.
Glass: Float glass, tempered glass (edge work only), laminated glass, mirrors. Perfect for decorative panels, dividers, and artistic installations without thermal stress cracking.
Composites: Carbon fiber reinforced polymers (CFRP), fiberglass, Kevlar, laminates (like G10/FR4). Minimizes delamination and fraying compared to mechanical tools.
Plastics & Polymers: Acrylic (Plexiglas), polycarbonate, PVC, HDPE, UHMW, rubber, foam (without melting or toxic fumes).
Food Products: Cutting frozen foods, baked goods, meat, fish, and poultry hygienically with pure water jets.
Exotic Materials: Textiles, insulation materials, gasketing, circuit boards, honeycomb structures.
This “one machine for almost all materials” capability simplifies factory floor logistics and reduces the need for multiple specialized cutting systems. The water jet for industrial use truly shines as a universal cutting solution.
3. Precision, Edge Quality, and the Cold Cutting Advantage
Water jet for industrial cutting delivers exceptional precision and edge quality, coupled with a critical non-thermal advantage:
High Precision: Modern CNC-controlled waterjets achieve positioning accuracies of +/- 0.001″ to +/- 0.005″ (0.03mm to 0.13mm) and repeatability within similar tolerances. Intricate contours, sharp corners, and complex geometries are easily machined directly from CAD files.
Superior Kerf Quality: The kerf (cut width) is typically narrow (0.020″ to 0.050″ / 0.5mm to 1.3mm depending on orifice/abrasive size and material). Abrasive waterjet cuts generally produce a smooth, sandblasted finish on the top surface, transitioning to a slightly rougher texture near the bottom (taper). Advanced techniques and dynamic cutting heads minimize taper.
Minimal Heat Affected Zone (HAZ): This is the defining “cold cutting” advantage. Unlike lasers, plasma, or EDM, waterjet cutting generates negligible heat. There is:
No thermal distortion or warping of the material.
No hardening, annealing, or micro-structural changes in metals.
No heat-affected zone that weakens the material near the cut edge.
No melting or charring of plastics or composites.
No hazardous fumes or vapors typically associated with thermal processes.
No Mechanical Stresses: Unlike traditional milling or sawing, there is no direct tool contact, eliminating chatter, burrs (minimal edge rounding), and tool-induced stresses or vibrations in the workpiece. Secondary finishing operations are often significantly reduced or eliminated.
This combination of precision, quality, and cold processing makes water jet for industrial applications ideal for critical components, heat-sensitive materials, and finished parts requiring minimal post-processing.
4. Comparing Industrial Waterjets to Other Cutting Technologies
Understanding where water jet for industrial fits requires comparison to its primary competitors:
vs. Laser Cutting:
Waterjet Wins: Thick materials (>1″ metal), reflective metals (copper, brass), heat-sensitive materials (plastics, composites, glass), no HAZ, no toxic fumes from coated metals/plastics.
Laser Wins: Very thin sheet metal speed, extreme precision on thin materials, lower operating costs for thin sheets, smoother edges on thin metals.
vs. Plasma Cutting:
Waterjet Wins: Precision, edge quality (no dross), ability to cut non-conductive materials, minimal HAZ, versatility beyond metals.
Plasma Wins: Speed on thick conductive metals (>1″), lower initial cost for basic systems, lower consumable cost per inch on thick steel.
vs. EDM (Wire & Sinker):
Waterjet Wins: Cutting speed (especially thicker sections), no need for conductive materials, ability to start cuts anywhere (no pilot hole needed), lower consumable costs.
EDM Wins: Extreme precision and surface finishes on conductive materials, ability to cut very hard materials without inducing stress, intricate detail on thin sections.
vs. Mechanical Cutting (Saws, Routers, Mills):
Waterjet Wins: No tool wear/chatter, minimal cutting forces (no part clamping distortion), greater design flexibility (no tool radius limitations), ability to cut very hard or brittle materials.
Mechanical Wins: Speed on softer materials in simple shapes, potentially lower operating costs for high-volume standard shapes, superior surface finish on some materials (milling).
The water jet for industrial solution excels as a versatile, precise, and material-agnostic technology, particularly valuable for thick materials, prototypes, short runs, and complex shapes across diverse materials.
5. Diverse Industrial Applications Across Sectors
The unique capabilities of water jet for industrial systems have led to widespread adoption across numerous industries:
Aerospace & Defense: Precision cutting of titanium, aluminum alloys, composites (CFRP) for airframe components, engine parts, heat shields, and armor plating with no HAZ compromising material integrity.
Automotive: Prototyping, gaskets, interior trim (textiles, foam, plastics), body panels, fiberglass components, airbag fabric, headliners, and custom aftermarket parts.
Machine Shops & Job Shops: Versatile “one-stop” cutting solution for diverse customer materials and projects – from intricate brackets and gears to thick plates and decorative elements.
Architecture, Construction & Stone Fabrication: Cutting intricate patterns in granite, marble, and tile for countertops, flooring, cladding, signage, and artistic features. Cutting structural steel shapes.
Electronics: Precise cutting of circuit boards (PCBs), insulating materials, gaskets, and thin metals without inducing thermal damage or static.
Energy (Oil & Gas, Renewable): Cutting pipeline parts, flanges, valves, wind turbine components (composites, metals), and solar panel mounting structures.
Medical Device Manufacturing: Cutting biocompatible materials (titanium, stainless steel, plastics, composites) for implants, surgical instruments, and diagnostic equipment housings with sterile-capable pure water options.
Food Processing: Hygienic portioning of frozen foods, baked goods, meat, fish, and poultry using pure waterjet technology.
Art & Signage: Creating complex sculptures, detailed metal artwork, dimensional letters, and intricate signage from almost any material.
The adaptability of the water jet for industrial platform makes it a critical asset in any modern fabrication environment dealing with diverse materials and complex designs.
6. Key Considerations When Implementing an Industrial Waterjet System
Investing in a water jet for industrial system requires careful evaluation:
Abrasive vs. Pure Water: Determine primary materials. Pure water jets are excellent for soft materials (rubber, foam, food) and offer very low operating costs. Abrasive jets are essential for metals, stone, glass, and composites but involve abrasive (garnet) purchase and disposal.
Pump Type & Pressure:
Intensifier Pumps: Proven technology, capable of ultra-high pressures (90,000+ PSI), excellent for thick, hard materials. Experience pressure fluctuations requiring accumulators.
Direct-Drive Pumps: Newer technology, linear motor-driven, offer constant pressure, potentially lower maintenance, high efficiency. Currently max out around 60,000-87,000 PSI. Often quieter.
Table Size & Configuration: Match the table size (X, Y travel) and load capacity to the largest parts anticipated. Consider options like downdraft tables (common), watertank tables (submerged cutting reduces noise/splash), or slat tables.
CNC Control & Software: Look for robust, user-friendly controls capable of precise motion and advanced features like taper compensation, automatic nozzle calibration, 5-axis cutting (for bevels and contours), and nesting software to optimize material usage.
Abrasive Delivery System: Reliable, consistent abrasive metering is crucial for cut quality and efficiency. Consider systems with hoppers and feeders designed for minimal clogging.
Filtration & Water Treatment: Essential for pump longevity. Requires multi-stage filtration (particulate, deionization/softening). Water recycling systems can significantly reduce operating costs and environmental impact.
Operating Costs: Factor in electricity, garnet abrasive (primary cost for abrasive cutting), replacement orifices/focus tubes, pump maintenance, water treatment, and waste disposal. Pure water jets have minimal consumables.
Noise & Safety: Waterjets are loud (especially abrasive cutting). Sound enclosures are highly recommended. Safety protocols for high-pressure water and flying debris are mandatory (safety glass, interlocks).
Selecting the right water jet for industrial application involves balancing technical requirements, material needs, production volume, and budget.
7. The Future of Industrial Waterjet Technology
The evolution of water jet for industrial cutting continues:
Increased Automation: Integration with robotics for loading/unloading, part handling, and lights-out manufacturing. Automated abrasive handling and waste removal systems.
Enhanced Precision & Speed: Ongoing improvements in pump efficiency (higher pressures, constant pressure), cutting head dynamics (reduced taper, faster acceleration), and motion control for finer detail and higher throughput.
Smarter Software: Advanced AI-driven nesting for maximized material yield, predictive maintenance algorithms, real-time process monitoring for quality control, and seamless CAD/CAM integration.
Multi-Technology Hybridization: Combining waterjet cutting with other processes (e.g., milling heads on the same gantry) on a single platform for complete part machining.
Sustainability Focus: Development of more efficient pumps, advanced water recycling and filtration systems, and exploration of alternative, more sustainable abrasives or abrasive recycling techniques.
5-Axis & 3D Cutting Proliferation: Wider adoption of 5-axis heads enabling complex bevel cutting, 3D shaping, and reduced secondary operations.
These advancements promise to further solidify water jet for industrial manufacturing as an indispensable, versatile, and increasingly efficient cornerstone technology.
The water jet for industrial cutting system stands as a testament to the power of harnessing a fundamental force – water – with advanced engineering. Its unique combination of cold cutting, exceptional material versatility, high precision, and excellent edge quality has revolutionized manufacturing and fabrication across countless industries. From intricate aerospace components to stunning architectural stonework, from delicate medical devices to robust machinery parts, waterjet technology delivers where other methods fall short. By understanding the core technology, its advantages and limitations compared to alternatives, and the key factors in system selection, manufacturers can leverage this powerful tool to enhance their capabilities, improve part quality, reduce waste, and unlock new design possibilities. As technology advances towards greater automation, speed, precision, and sustainability, the water jet for industrial applications is poised to remain a critical and evolving force in the future of industrial production.
continue reading