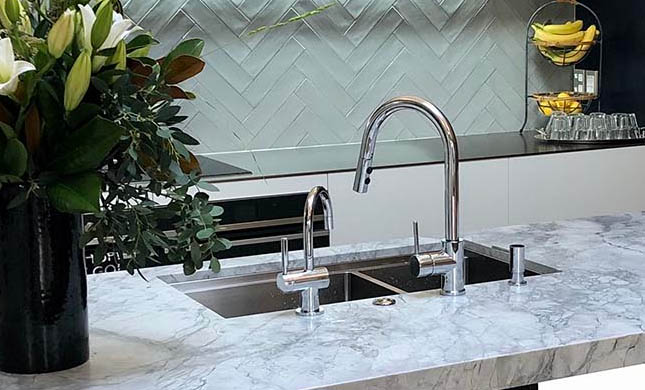
Water Jet Cutting Iron: The Ultimate Guide to Precision, Benefits & Applications
In the demanding world of metal fabrication, finding methods that combine precision, versatility, and minimal material stress is paramount. While lasers and plasma cutters dominate many discussions, water jet cutting iron stands out as a uniquely powerful and adaptable technology, especially for ferrous metals. This cold-cutting process utilizes the immense energy of ultra-high-pressure water, often mixed with abrasive particles, to slice through tough materials like iron and steel with remarkable accuracy and without altering the material’s inherent properties through heat. This comprehensive guide delves deep into the science, advantages, applications, and practicalities of water jet cutting iron, showcasing why it’s an indispensable tool for modern manufacturing.
1. The Science Behind Water Jet Cutting Iron: Harnessing Hydraulic Power
At its core, water jet cutting iron is a marvel of fluid dynamics and focused energy. Here’s how it works:
Ultra-High Pressure Generation: The process begins with an intensifier pump or direct drive pump, capable of generating pressures ranging from 40,000 PSI (2,750 bar) to an astonishing 90,000 PSI (6,200 bar) or even higher. Ordinary water is pressurized to this extreme state.
Focusing the Stream: The high-pressure water is forced through a small orifice, typically made of diamond or sapphire, ranging from 0.004″ to 0.016″ (0.1mm to 0.4mm) in diameter. This orifice transforms the pressurized water into a coherent, supersonic stream traveling at speeds exceeding Mach 3 (over 2,000 mph or 3,200 km/h).
Introducing the Abrasive (For Iron Cutting): Pure water jets are excellent for soft materials but lack the necessary force to effectively erode hard metals like iron and steel. Therefore, for water jet cutting iron, an abrasive material (almost always garnet sand) is introduced into the stream. This happens in a mixing chamber just below the orifice. The high-velocity water stream accelerates the abrasive particles, turning them into countless microscopic cutting tools.
The Cutting Action: The abrasive-laden water jet impacts the iron surface with tremendous kinetic energy. The hard, sharp garnet particles rapidly erode the material through a micro-machining process, essentially “sandblasting” an extremely narrow path through the metal. The water serves primarily to accelerate the abrasives and flush away the eroded material (swarf) from the cut kerf. This cold-cutting mechanism avoids the Heat-Affected Zone (HAZ) associated with thermal processes.
2. Why Choose Water Jet Cutting for Iron? Key Advantages Unveiled
Water jet cutting iron offers a compelling set of benefits that make it superior to many alternative cutting methods in numerous scenarios:
Zero Heat-Affected Zone (HAZ): This is the most significant advantage. Unlike laser, plasma, or oxy-fuel cutting, water jet cutting iron generates no significant heat at the cut surface. This means:
No Metallurgical Changes: The crystalline structure of the iron remains unchanged. There is no hardening, tempering loss, warping, or residual stresses induced by heat.
No Thermal Distortion: Thin sections or complex geometries won’t warp or buckle due to uneven heating/cooling.
Preserved Material Integrity: Critical for parts requiring maximum strength and fatigue resistance, where HAZ can be a weak point.
Material Versatility: While focused on water jet cutting iron, the same machine can effortlessly cut virtually any material – aluminum, copper, titanium, stone, glass, composites, rubber, plastics, ceramics, food – simply by adjusting pressure and the use of abrasives. This eliminates the need for multiple dedicated cutting machines.
Exceptional Precision and Edge Quality: Modern abrasive water jet systems offer high precision (±0.003″ to ±0.005″ or ±0.075mm to ±0.125mm is common) and can produce intricate shapes, sharp corners, and complex contours with minimal taper (especially with taper compensation software). The cut edge is typically smooth, with a uniform matte finish, often requiring little to no secondary finishing for many applications.
No Hazardous Fumes or Byproducts: The process uses water and natural garnet abrasive. It produces no toxic fumes, gases, or molten slag associated with thermal cutting of iron. This creates a cleaner, safer work environment and reduces ventilation requirements.
Minimal Mechanical Stress: The cutting force exerted by the waterjet is relatively low and localized, minimizing the risk of distorting delicate parts or fixtures compared to high-force mechanical methods like shearing or punching.
Ability to Cut Thick Materials: Abrasive water jets excel at cutting thick sections of iron and steel, routinely handling thicknesses from thin sheet metal up to 6 inches (150mm), 8 inches (200mm), and even thicker with specialized equipment and slower speeds.
3. Capabilities and Performance: Cutting Iron and Steel Effectively
Understanding the practical performance metrics is crucial when considering water jet cutting iron:
Cutting Speed vs. Thickness & Quality: Cutting speed is inversely proportional to material thickness and the desired edge quality.
Thin Iron/Steel (e.g., 1/8″ / 3mm): Can be cut very quickly (tens of inches per minute).
Thick Iron/Steel (e.g., 4″ / 100mm): Requires significantly slower speeds (inches per minute). Higher pressures and optimized abrasives allow for faster cutting in thicker sections.
Quality Settings: Machines offer different quality modes. “Rough” cuts are faster but have more striations. “Finish” or “Quality” modes slow the jet down, producing a smoother, more precise edge, often with reduced taper.
Edge Quality and Taper:
Finish: The abrasive water jet produces a characteristic smooth, satin finish with fine striations running parallel to the cut direction. The striations become more pronounced at faster speeds and in thicker materials. The edge is typically burr-free.
Taper (Kerf Angle): Due to the nature of the jet diverging slightly as it cuts deeper, a slight taper naturally occurs (wider at the top than the bottom). Advanced systems use dynamic head tilting (“5-axis” cutting) or sophisticated software algorithms to compensate for this taper, producing near-vertical edges even in thick iron plates.
Kerf Width: The abrasive water jet removes a small amount of material, known as the kerf. Kerf width typically ranges from 0.030″ to 0.050″ (0.76mm to 1.27mm), depending on the orifice size, abrasive flow rate, and material thickness. This must be accounted for in nesting parts for material efficiency.
Tolerances: Modern CNC-controlled water jets deliver excellent repeatability and accuracy, typically holding tolerances within ±0.003″ to ±0.005″ (±0.075mm to ±0.125mm) under optimal conditions for precision parts. Tolerances widen slightly with increasing thickness.
4. Diverse Applications: Where Water Jet Cutting Iron Shines
The unique advantages of water jet cutting iron make it the preferred choice across a vast spectrum of industries:
Aerospace & Defense: Cutting high-strength alloys, titanium components, intricate engine parts, landing gear components, and armored plate without compromising material integrity or inducing stress. Prototyping complex shapes is also common.
Automotive Manufacturing: Producing prototypes, gaskets, brackets, suspension components, specialized tools, fixtures, and even trimming composite parts. The ability to cut dissimilar materials or stacks is valuable.
Machine Building & Tool & Die: Fabricating machine bases, frames, gears (pre-hardened state), molds, dies, jigs, fixtures, and wear plates with precision and no HAZ. Cutting tool steel blanks is frequent.
Marine & Shipbuilding: Cutting thick hull plates, structural components (beams, frames), decking, and specialized fittings from various grades of steel, including high-strength and corrosion-resistant types.
Architectural & Artistic Metalwork: Creating intricate decorative panels, signage, sculptures, railings, stair components, and custom facades from steel, iron, and other metals. The design freedom is immense.
Energy Sector (Oil, Gas, Renewable): Fabricating pressure vessel components, flanges, valve bodies, turbine parts, wind tower sections, and pipeline fittings where material properties are critical.
General Fabrication & Job Shops: Offering a versatile service for customers needing prototypes, one-off parts, complex shapes, or materials sensitive to heat. The ability to cut virtually anything makes it invaluable.
5. Implementing Water Jet Cutting Iron: Practical Considerations
Successfully integrating water jet cutting iron requires understanding the operational aspects:
Equipment Investment: Abrasive water jet systems represent a significant capital investment. Costs vary based on cutting envelope size, maximum pressure capability, pump type, automation level, and features like taper compensation or 5-axis.
Operating Costs: Key consumables include:
Abrasives (Garnet): The single largest ongoing cost. Consumption depends on material type, thickness, pressure, and cut quality.
Orifice (Diamond/Sapphire): High-pressure water jets erode these precious gem orifices over time (hundreds of hours).
Focusing Tubes (Mixing Tubes): The nozzle where water and abrasive mix and are focused; wears out regularly.
High-Pressure Seals and Valves: Require periodic maintenance and replacement.
Electricity: High-pressure pumps consume significant power.
Water: Needs filtration and often deionization for the intensifier pump.
Noise and Setup: Abrasive water jets are loud (typically requiring sound enclosures) and involve high-pressure plumbing, demanding proper safety protocols and facility considerations (floor loading, drainage for the water/swarf slurry).
Material Handling: Cutting thick, heavy iron plates requires robust material handling equipment (cranes, lifting magnets, vacuum lifts) and sturdy cutting tables.
Nesting Software: Efficiently arranging parts on a sheet of iron to minimize waste is critical for cost-effectiveness. Advanced CAD/CAM nesting software is essential.
Operator Skill: Requires skilled operators for programming, optimizing cutting parameters for different materials/thicknesses, machine maintenance, and troubleshooting.
6. Water Jet vs. Alternatives: Cutting Iron Effectively
How does water jet cutting iron compare to other common methods?
vs. Laser Cutting:
Laser: Faster on thin to medium steel, excellent precision. Creates HAZ, can struggle with highly reflective metals (copper, brass), and has limited thickness capacity (usually <1″ / 25mm for CO2 lasers, higher with fiber).
Water Jet: No HAZ, cuts any thickness (slower on thick), cuts reflective metals easily, cuts non-metals. Slower on thin material.
vs. Plasma Cutting:
Plasma: Faster than water jet on thick steel, lower initial cost. Creates significant HAZ, wider kerf, poorer edge quality/accuracy, generates fumes/slag, limited precision.
Water Jet: Superior edge quality, precision, no HAZ, no fumes/slag, better for intricate shapes. Slower on thick material, higher operating cost.
vs. Oxy-Fuel Cutting:
Oxy-Fuel: Lowest equipment cost, good for very thick steel sections. Very wide HAZ, poor edge quality and precision, slow, limited to carbon steels, generates significant slag and distortion.
Water Jet: Far superior precision, edge quality, no HAZ, no distortion, cuts all metals and alloys. Higher cost, slower on very thick sections.
vs. Wire EDM (Electrical Discharge Machining):
Wire EDM: Exceptional precision and surface finish, no mechanical stress. Very slow, only conductive materials, high consumable costs (wire, filters), limited thickness practicality.
Water Jet: Faster (especially thicker), cuts non-conductive materials, lower consumable cost per part (though garnet is significant). Less precise than EDM for ultrafine features.
7. The Future of Water Jet Cutting Iron: Trends and Innovations
Water jet cutting iron technology continues to evolve:
Higher Pressures (90,000+ PSI / 6,200+ bar): Enable faster cutting speeds, especially in thick materials, and improved edge quality.
Advanced Pump Technology: Direct drive pumps offer higher efficiency, faster response times, and potentially lower maintenance than traditional intensifier pumps.
Intelligent Cutting Heads & Software: Enhanced real-time monitoring of cut quality, automatic parameter adjustment, improved taper compensation algorithms, and smarter nesting for maximized material yield.
Hybrid Manufacturing: Integration of water jet cutting with additive manufacturing (3D printing) or machining centers within a single cell for complex part production.
Improved Abrasive Delivery & Recycling: Systems for more precise abrasive metering and even exploring methods for partial abrasive recycling to reduce the largest operating cost.
Enhanced Automation: Greater integration with robotics for loading/unloading, part handling, and lights-out manufacturing.
Water jet cutting iron is far more than just an alternative; it’s a uniquely capable and versatile manufacturing process that solves critical problems inherent in thermal cutting methods. Its defining characteristic – the complete absence of a Heat-Affected Zone – makes it indispensable for applications where preserving the metallurgical integrity of iron and steel is non-negotiable. Combined with its remarkable precision, ability to handle complex geometries, capacity to cut thick sections, and unparalleled material versatility, water jet technology offers a compelling solution across aerospace, automotive, energy, tooling, art, and general fabrication.
While the investment and operating costs (primarily abrasives) require careful consideration, the benefits of superior part quality, reduced secondary operations, design freedom, and the ability to cut virtually anything often deliver a significant return on investment and open doors to new manufacturing possibilities. As pressure capabilities rise, software intelligence grows, and automation deepens, water jet cutting iron is poised to remain a vital and increasingly efficient force in the future of precision metal fabrication. For engineers and fabricators seeking a cold, precise, and versatile method to shape iron and steel, the water jet is an essential tool in the modern manufacturing arsenal.
continue reading