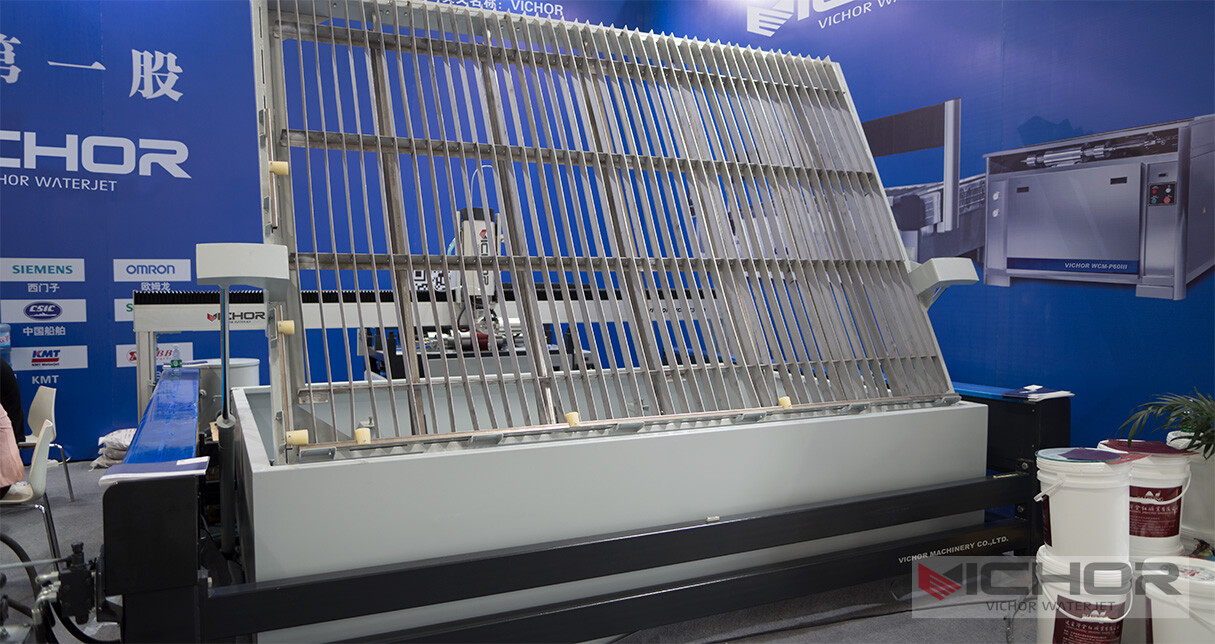
Water Cutter Head: The Precision Powerhouse Behind Modern Waterjet Cutting
In the world of industrial cutting, few technologies match the versatility and precision of abrasive waterjet (AWJ) systems. At the very heart of this remarkable capability lies a critical, often under-appreciated component: the water cutter head. Far more than just a nozzle holder, the water cutter head is a sophisticated assembly responsible for generating the ultra-high-pressure stream, precisely mixing abrasive material, and delivering the focused cutting force that defines the process. Understanding the design, function, and critical aspects of the water cutter head is essential for anyone seeking to maximize the performance, efficiency, and longevity of their waterjet system. This article delves deep into the anatomy and operation of this vital component.
1. Core Function and Working Principle of the Water Cutter Head
The fundamental role of the water cutter head is to transform ordinary water into a cutting tool capable of slicing through virtually any material. This transformation occurs through a meticulously controlled process:
Ultra-High-Pressure Intensification: Water is pressurized to extreme levels, typically between 30,000 PSI (2,000 bar) and 90,000 PSI (6,200 bar), by an intensifier pump.
Orifice Formation: This pressurized water is forced through a tiny, precisely engineered orifice (usually made of sapphire, ruby, or diamond) within the water cutter head. This constriction accelerates the water to supersonic speeds, often exceeding Mach 3 (over 2,300 mph or 3,700 km/h).
Abrasive Induction & Mixing: Immediately downstream of the water orifice, the water cutter head features an abrasive inlet port. Under the influence of the high-velocity water stream creating a powerful vacuum (Venturi effect), abrasive garnet particles are drawn into a mixing chamber within the head.
Focusing & Acceleration: The high-speed water stream and abrasive particles are thoroughly mixed within the mixing tube (also called the focusing tube or nozzle). This tube, a critical part of the water cutter head, aligns the particles and further accelerates them, forming a coherent, abrasive-laden cutting jet.
Material Erosion: This focused jet of water and abrasive exits the water cutter head and strikes the workpiece. The abrasive particles perform the cutting work through micro-erosion, while the water acts as the carrier, removes debris, and cools the cut.
The water cutter head is the essential nexus where water pressure, abrasive flow, and precise geometry converge to create the cutting action. Its design directly dictates jet coherence, cutting speed, edge quality, and kerf width.
2. Key Components and Anatomy of the Water Cutter Head
A typical water cutter head is not a single monolithic part but a carefully engineered assembly integrating several critical components, each playing a vital role:
Body/Manifold: The main structural housing of the water cutter head. It contains internal passages for the high-pressure water, features the abrasive inlet port, and provides threaded connections for mounting other components and attaching the head to the Z-axis of the cutting machine. It must withstand immense internal pressure without deformation or fatigue failure.
Orifice Holder/Insert: A precision assembly that securely holds the gem orifice (sapphire, ruby, diamond). It ensures perfect alignment with the mixing tube downstream and provides a leak-proof seal against the ultra-high-pressure water. The design allows for easy replacement of the orifice.
Gem Orifice: The tiny jewel (typically sapphire for cost-effectiveness and good life, diamond for maximum longevity and performance at highest pressures) that forms the initial high-velocity water jet. Its diameter (commonly 0.004″ to 0.016″ / 0.10mm to 0.40mm) is crucial for jet formation and abrasive suction efficiency. This is the first point of wear in the water cutter head.
Mixing Chamber: The cavity immediately downstream of the orifice where the abrasive particles are introduced and initial mixing with the water stream occurs, driven by the Venturi effect created by the high-speed water jet.
Mixing Tube (Focusing Tube/Nozzle): This is arguably the most critical wear component after the orifice. A long, narrow tube (usually made of extremely hard tungsten carbide or composite diamond) where the abrasive-water mixture is fully homogenized and accelerated into a coherent cutting jet. Its inner diameter (ID – typically 0.020″ to 0.060″ / 0.50mm to 1.50mm) and length-to-diameter ratio significantly influence jet focus, cutting precision, and taper characteristics. Wear enlarges the ID and degrades performance.
Abrasive Inlet Tube/Assembly: The connection point for the abrasive delivery hose. It includes features to ensure smooth, consistent abrasive flow into the mixing chamber without clogging. Some designs incorporate metering valves or flow sensors.
Guard/Shroud: A protective cover often surrounding the lower part of the water cutter head, shielding the mixing tube from accidental impacts and sometimes helping to contain splashback.
Seals and Fittings: High-integrity seals (often dynamic seals rated for ultra-high-pressure) are essential throughout the water cutter head assembly to prevent leaks at the numerous connection points for water, abrasive, and between components.
The precise alignment and concentricity of the orifice, mixing chamber, and mixing tube within the water cutter head are paramount for optimal jet formation and cutting performance.
3. Material Selection and Wear Mechanisms
The water cutter head operates in an incredibly harsh environment, subject to extreme pressures, abrasive particle impacts, and potential cavitation. Material choices are critical for longevity and consistent performance:
Orifice Materials:
Sapphire: Most common. Excellent hardness and good wear resistance at a reasonable cost. Life varies significantly based on pressure, water quality, and abrasiveness.
Ruby: Slightly harder than sapphire but more brittle. Less common now.
Diamond: The ultimate in orifice performance. Extremely hard and wear-resistant, offering vastly extended life (often 5-10x sapphire), especially at pressures above 60k PSI. Significantly higher initial cost. Essential for high-volume production.
Mixing Tube Materials:
Tungsten Carbide (WC): The industry standard. Offers a good balance of hardness, toughness, and cost. Available in various grades and compositions optimized for wear resistance. Life expectancy ranges from tens to hundreds of hours depending on abrasive type, flow rate, pressure, and tube quality.
Composite Diamond: Features a polycrystalline diamond (PCD) lining inside a carbide sleeve. Offers exceptional wear resistance, often extending life 5-20 times beyond standard carbide tubes. Higher cost, but excellent ROI in high-use applications demanding minimal taper and consistent kerf.
Body/Manifold Materials: Typically high-strength stainless steel (e.g., 17-4 PH, 316, 304) or specialized alloys engineered for high-pressure resistance and corrosion resistance. Precision machining is critical.
Wear Mechanisms:
Abrasive Erosion: Constant bombardment by hard garnet particles gradually wears away the orifice bore (increasing diameter, reducing jet velocity/suction) and enlarges the mixing tube ID (reducing jet coherence, increasing kerf width and taper).
Cavitation: Rapid pressure changes near the orifice can cause tiny vapor bubbles to form and implode violently, pitting metal surfaces over time. Good orifice condition and water quality mitigate this.
Impact Damage: Accidental collisions with the workpiece or fixtures can crack orifices or damage mixing tubes. Proper guarding and collision detection systems help.
Corrosion/Erosion-Corrosion: Impurities in water can lead to corrosion, which is accelerated by the abrasive flow.
Regular inspection and timely replacement of the orifice and mixing tube are the most critical maintenance tasks for the water cutter head to maintain cutting quality and efficiency.
4. Impact on Cutting Performance and Quality
The condition and configuration of the water cutter head directly dictate almost every aspect of waterjet cutting performance:
Cutting Speed: A worn orifice (larger hole) reduces water pressure and velocity, decreasing abrasive suction and acceleration. A worn mixing tube (larger ID) reduces jet coherence and energy density. Both drastically reduce cutting speed. A perfectly tuned water cutter head with sharp orifice and correct mixing tube ID maximizes speed.
Edge Quality (Striations & Smoothness): A coherent jet produced by a well-maintained water cutter head with a precise mixing tube creates smoother cuts with finer, more consistent striations. Worn components lead to a “flaring” jet, causing wider, rougher kerfs with deeper, more irregular striations and increased taper.
Kerf Width and Taper: The inner diameter of the mixing tube is the primary determinant of kerf width. A new tube produces the narrowest possible kerf. As the tube wears and ID increases, the kerf widens. Taper (the difference in width between the top and bottom of the cut) is minimized with a sharp orifice, correct mixing tube ID/length ratio, and optimal cutting speed – all governed by the water cutter head’s condition and setup.
Precision and Accuracy: Jet coherence is vital for holding tight tolerances and intricate details. A degraded jet from a worn water cutter head will have more divergence, reducing positional accuracy and the ability to cut sharp corners or small features.
Abrasive Consumption Efficiency: The orifice condition and mixing chamber design determine the efficiency of the Venturi effect, dictating how effectively abrasive is drawn in and mixed. A worn orifice or clogged inlet reduces abrasive flow relative to water, wasting abrasive and reducing cutting power. An optimized water cutter head ensures the correct abrasive-to-water ratio.
Noise Level: Surprisingly, a well-maintained water cutter head with a sharp orifice and good mixing tube can produce a slightly quieter, more focused jet stream compared to a worn head with a flaring jet.
Monitoring cut quality and speed provides the first indicators that the water cutter head components (orifice and mixing tube) may need attention.
5. Maintenance, Inspection, and Best Practices
Proactive maintenance of the water cutter head is non-negotiable for achieving consistent results and minimizing operating costs:
Regular Inspection Schedule: Visually inspect the orifice and mixing tube daily for obvious damage or wear. Measure orifice diameter and mixing tube ID regularly using precision pin gauges or optical comparators (frequency depends on usage intensity – high-volume shops might do this multiple times per shift). Track wear rates.
Preventive Replacement: Don’t wait for components to fail completely. Establish replacement intervals based on tracked wear data, material cut, and required quality levels. Replacing an orifice or tube before it degrades performance significantly is cheaper than lost production time and wasted material from poor cuts.
Cleaning Procedures: Flush the water cutter head regularly, especially when changing abrasive types or after periods of inactivity. Follow manufacturer guidelines for disassembly and cleaning to prevent damage to seals and precision surfaces. Ensure abrasive lines are free of moisture and blockages.
Proper Installation & Alignment: When replacing orifices or mixing tubes, follow manufacturer torque specifications precisely. Ensure perfect concentricity between the orifice and mixing tube during reassembly. Misalignment destroys performance instantly. Use alignment tools if provided.
Water Quality Management: Use filtered, deionized water. Impurities cause accelerated orifice wear (erosion) and can lead to clogging or scaling inside the water cutter head passages and mixing chamber.
Abrasive Quality & Consistency: Use high-quality, consistently sized garnet abrasive. Poor quality or contaminated abrasive accelerates wear on both the orifice and, especially, the mixing tube.
Collision Avoidance: Implement and maintain reliable machine collision detection systems. Even minor impacts can crack expensive diamond orifices or bend carbide mixing tubes.
Record Keeping: Maintain detailed logs of component changes, wear measurements, cutting parameters, and observed performance. This data is invaluable for optimizing maintenance schedules and diagnosing problems.
Treating the water cutter head with care and adhering to a disciplined maintenance regime ensures peak performance and maximizes return on investment.
6. Innovations and Future Trends in Water Cutter Head Technology
The evolution of the water cutter head continues, driven by demands for higher precision, faster speeds, longer component life, and greater process control:
Enhanced Materials & Coatings: Research into even harder, tougher materials and advanced coatings (like nanocrystalline diamond) for orifices and mixing tubes promises further extended life, especially under ultra-high-pressure (90k+ PSI) regimes.
“Intelligent” Heads: Integration of sensors directly into the water cutter head is emerging. Sensors could monitor:
Orifice and mixing tube wear in real-time (e.g., via pressure drop, acoustic emission).
Abrasive flow rate consistency.
Jet coherence/vibration.
Temperature.
This data allows for predictive maintenance, automatic parameter adjustment, and real-time quality assurance.
Improved Mixing Dynamics: Computational Fluid Dynamics (CFD) modeling is being used to optimize mixing chamber and tube geometries for more efficient abrasive entrainment, better particle acceleration, and reduced turbulence, leading to sharper, more coherent jets.
Modular & Quick-Change Designs: Heads designed for rapid swapping of entire cutting assemblies (orifice holder + mixing tube) minimize machine downtime during changeovers, crucial for high-mix production environments.
Dynamic Cutting Control: Integration with machine controls could allow for dynamic adjustment of Z-axis height or even abrasive flow based on real-time sensor feedback from the water cutter head to optimize cut quality throughout the entire process, especially on thick or varying materials.
Specialized Head Designs: Development of heads optimized for specific tasks, like very high-pressure pure water cutting (no abrasive) for soft materials, or heads designed for minimal taper in thick plate cutting.
The water cutter head remains a focal point for innovation, ensuring waterjet technology continues to advance in precision, efficiency, and application scope.
The water cutter head is far more than a simple nozzle; it is the high-precision engine that powers abrasive waterjet cutting. Its intricate design, involving critical components like the gem orifice and carbide mixing tube working under extreme conditions, directly determines the speed, quality, precision, and cost-effectiveness of the entire cutting process. Understanding its function, the impact of wear, and implementing rigorous maintenance protocols are fundamental for any successful waterjet operation. From transforming high-pressure water into a supersonic stream to perfectly mixing and focusing abrasive particles, the water cutter head performs a remarkable feat of engineering. As innovations in materials, sensing, and design continue to emerge, the water cutter head will remain central to unlocking the full potential and expanding the capabilities of waterjet technology in modern manufacturing. Investing in quality components and diligent care for this vital assembly is an investment in consistent, high-performance cutting.
continue reading
Related Posts
- 1559 words7.8 min read
- 1716 words8.7 min read