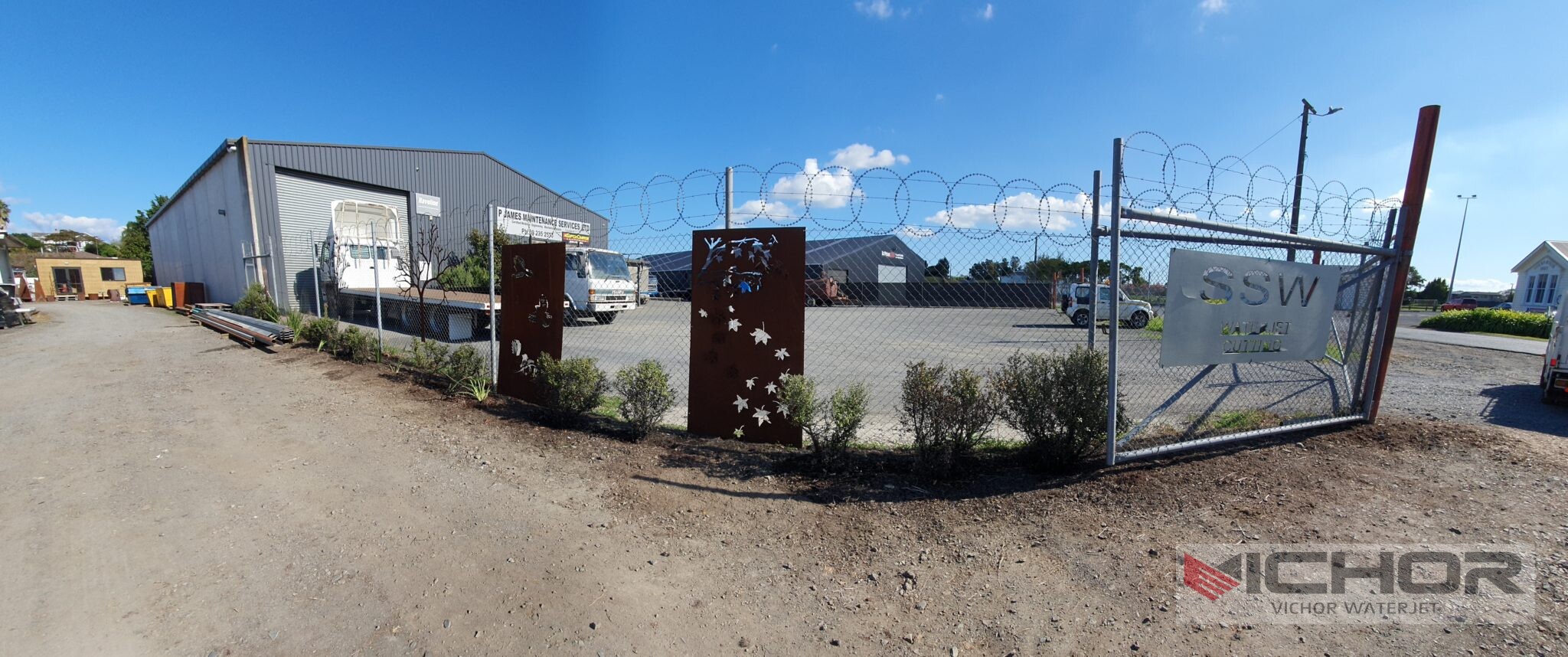
Unlock Complex Designs: The Power of 5 Axis Waterjet Cutting Explained
In the relentless pursuit of manufacturing precision, efficiency, and versatility, 5 axis waterjet cutting has emerged as a transformative technology. Moving far beyond the capabilities of traditional 3-axis systems, this advanced machining process unlocks the ability to create complex, intricate, and highly accurate parts from an astonishingly wide range of materials. This article delves deep into the world of 5 axis waterjet cutting, exploring its fundamental principles, key advantages, diverse applications, and why it’s becoming an indispensable tool in modern fabrication.
What Exactly is 5 Axis Waterjet Cutting?
At its core, 5 axis waterjet cutting utilizes an ultra-high-pressure stream of water, often mixed with an abrasive garnet, to erode material. The defining feature of a 5 axis waterjet cutting machine is its cutting head’s ability to move along five distinct axes simultaneously. While traditional 3-axis machines (X, Y, Z) move the cutting head left/right, forward/backward, and up/down, a 5-axis system adds two rotational axes (typically A and C):
X-axis: Horizontal movement (left/right).
Y-axis: Horizontal movement (forward/backward).
Z-axis: Vertical movement (up/down – controlling the nozzle standoff distance).
A-axis: Rotation around the X-axis (tilting the cutting head forward/backward).
C-axis: Rotation around the Z-axis (rotating the cutting head clockwise/counter-clockwise).
This multi-directional freedom allows the abrasive waterjet stream to approach the workpiece from virtually any angle. Instead of the workpiece needing complex fixturing or multiple setups, the 5 axis waterjet cutting head dynamically orients itself to maintain optimal cutting angles, even on highly contoured or three-dimensional surfaces. This capability fundamentally changes how complex geometries are produced.
The Compelling Advantages of 5 Axis Waterjet Cutting
The transition from 3-axis to 5 axis waterjet cutting delivers a suite of powerful benefits that significantly enhance manufacturing capabilities:
Unparalleled Geometric Complexity & True 3D Cutting: This is the hallmark advantage. 5 axis waterjet cutting excels at producing parts with compound angles, intricate bevels (including varying angles along a single edge), undercuts, and complex 3D contours that are impossible or prohibitively expensive with 3-axis machines. It can machine sculpted surfaces directly from solid blocks or cut complex shapes on pre-formed parts without specialized tooling.
Dramatically Reduced Secondary Operations: By cutting bevels, chamfers, and complex edge geometries directly within the primary cutting process, 5 axis waterjet cutting eliminates the need for time-consuming and costly secondary machining, grinding, or finishing operations. This significantly reduces lead times, labor costs, and handling.
Superior Edge Quality & Precision on Angled Cuts: When cutting bevels on thick materials with a 3-axis machine, the waterjet stream naturally tapers (kerf taper), leading to inaccuracies and poor edge quality on the angled surface. 5 axis waterjet cutting dynamically tilts the cutting head to compensate for this taper, ensuring the stream remains perpendicular to the cut surface throughout the entire thickness. This results in straighter walls, sharper corners, near-elimination of taper on bevels, and significantly improved accuracy and surface finish on complex geometries.
Enhanced Versatility & Reduced Fixturing: The ability of the cutting head to orient itself optimally means complex parts often require minimal or simpler fixturing. Parts can be machined in a single setup, reducing setup time, potential for error between operations, and fixture costs. This flexibility is invaluable for prototyping and low-volume, high-mix production.
Material Savings & Nesting Efficiency: The precision and ability to cut complex shapes with minimal kerf (the width of the cut) allow for tighter nesting of parts on a single sheet or block of material, maximizing material utilization and reducing waste costs, especially when working with expensive alloys or composites.
Materials & Applications: Where 5 Axis Waterjet Cutting Shines
The cold-cutting nature of waterjet technology, combined with the agility of 5-axis motion, makes this process uniquely suited for a vast array of materials and industries:
Metals: From aluminum and stainless steel to titanium, Inconel, tool steels, brass, and copper – thick or thin. Ideal for aerospace components (engine parts, structural elements), defense, automotive prototypes and parts, intricate tooling, and complex architectural metalwork.
Composites: Carbon fiber reinforced polymers (CFRP), fiberglass, Kevlar. Crucial in aerospace (wing skins, fuselage parts), automotive (lightweight components), and sporting goods, where delamination and heat damage from other processes are major concerns. 5 axis waterjet cutting provides clean, precise cuts without thermal degradation.
Stone & Tile: Creating complex 3D sculptures, intricate inlays, countertops with integrated drainboards, vanity tops, and bespoke architectural elements with precise bevels and edge details.
Glass: Cutting thick laminated glass, creating complex shapes for architectural features, furniture, or artistic installations without thermal stress or micro-cracking.
Plastics & Polymers: Acrylics, polycarbonates, HDPE, UHMW, even sensitive materials like PTFE. Used for signs, machine guards, prototypes, and functional parts requiring precision.
Foams & Insulation: Cutting complex molds, plugs, and insulation panels for aerospace, marine, and construction industries.
Specific Application Examples:
Aerospace: Machining complex titanium engine brackets with integral mounting flanges and beveled edges in a single setup.
Energy: Cutting precise bevels on thick-walled pipe for welding preparation in oil & gas pipelines or power generation.
Medical: Fabricating intricate components for surgical instruments or implants from biocompatible metals and plastics.
Automotive: Prototyping complex suspension components or cutting lightweight composite body panels.
Architecture & Art: Creating flowing, sculptural metal facades, intricate stone inlays, or complex 3D art pieces.
Comparing 5 Axis Waterjet Cutting to Other Technologies
Understanding where 5 axis waterjet cutting fits within the manufacturing landscape requires comparison:
vs. 3-Axis Waterjet: As detailed, 5-axis adds critical capabilities for complex geometry, beveling, taper elimination, and reduced fixturing. 3-axis remains efficient for simpler 2D flat cutting.
vs. 5-Axis Milling (CNC): Milling uses rotating cutting tools which generate heat and significant mechanical forces. Waterjet is cold and force-free, making it superior for heat-sensitive materials (composites, tempered glass, certain plastics), very hard materials (like ceramics or hardened tool steel), and materials prone to work hardening. Waterjet also creates no Heat Affected Zone (HAZ). However, milling generally offers faster cutting speeds on softer metals and can achieve tighter tolerances and finer surface finishes on certain operations. Milling also struggles with very thick sections where 5 axis waterjet cutting excels.
vs. Laser Cutting: Lasers are fast and precise for 2D sheet metal cutting but generate intense heat (HAZ) and are generally limited to thinner materials. They cannot effectively cut reflective materials (copper, brass) or many non-metals (stone, glass, thick composites) without damage. 5 axis waterjet cutting handles thick sections, reflective materials, and diverse non-metals without thermal distortion or HAZ.
vs. Plasma Cutting: Plasma is primarily for conductive metals and generates significant heat, HAZ, and dross. It lacks the precision and edge quality of waterjet and cannot cut non-conductive materials. 5 axis waterjet cutting offers superior precision, edge quality, and material versatility without heat damage.
The Future of 5 Axis Waterjet Cutting: Trends & Innovations
5 axis waterjet cutting technology continues to evolve rapidly:
Increased Speed & Precision: Advancements in pump technology (delivering higher, more stable pressures like 90,000+ PSI), improved motion control systems, and sophisticated nozzle designs are constantly pushing the boundaries of cutting speed while maintaining or improving precision and edge quality.
Enhanced Software & Automation: CAD/CAM software specifically designed for 5 axis waterjet cutting is becoming more powerful and intuitive, simplifying the programming of complex geometries, automating collision avoidance, and optimizing toolpaths for speed and quality. Integration with factory automation (robotic loading/unloading) is increasing throughput.
Smarter Machines & AI: Integration of sensors for real-time monitoring of cut quality, abrasive flow, and nozzle condition. AI and machine learning are beginning to be used for predictive maintenance, adaptive cutting (adjusting parameters on the fly based on sensor feedback), and further optimization of toolpaths.
Sustainability Focus: Efforts are underway to develop more efficient pumps, improve abrasive recovery and recycling systems, and reduce overall water consumption, making the process more environmentally friendly.
Hybrid Manufacturing: Exploring the integration of 5 axis waterjet cutting with additive manufacturing (3D printing) or other subtractive processes within a single machine platform for complete part production.
5 axis waterjet cutting is far more than just an incremental improvement; it represents a paradigm shift in subtractive manufacturing. Its unique ability to combine the inherent advantages of cold, force-free waterjet cutting with the geometric freedom of 5-axis motion unlocks unprecedented design possibilities and manufacturing efficiencies. By eliminating secondary operations, handling an unmatched breadth of materials, and producing complex 3D parts with superior precision and edge quality, 5 axis waterjet cutting delivers significant cost and time savings, especially for prototypes, low-volume production, and highly complex components.
As technology advances in speed, precision, software, and automation, the adoption of 5 axis waterjet cutting will continue to grow across aerospace, automotive, energy, medical, and architectural industries. For manufacturers seeking to push the boundaries of design complexity while maintaining efficiency and material integrity, investing in 5 axis waterjet cutting capability is not just an option; it’s increasingly becoming a strategic necessity for staying competitive in a demanding market. It empowers engineers and designers to truly “unlock complex designs.”
continue reading
Related Posts
- 1559 words7.8 min read
- 1716 words8.7 min read