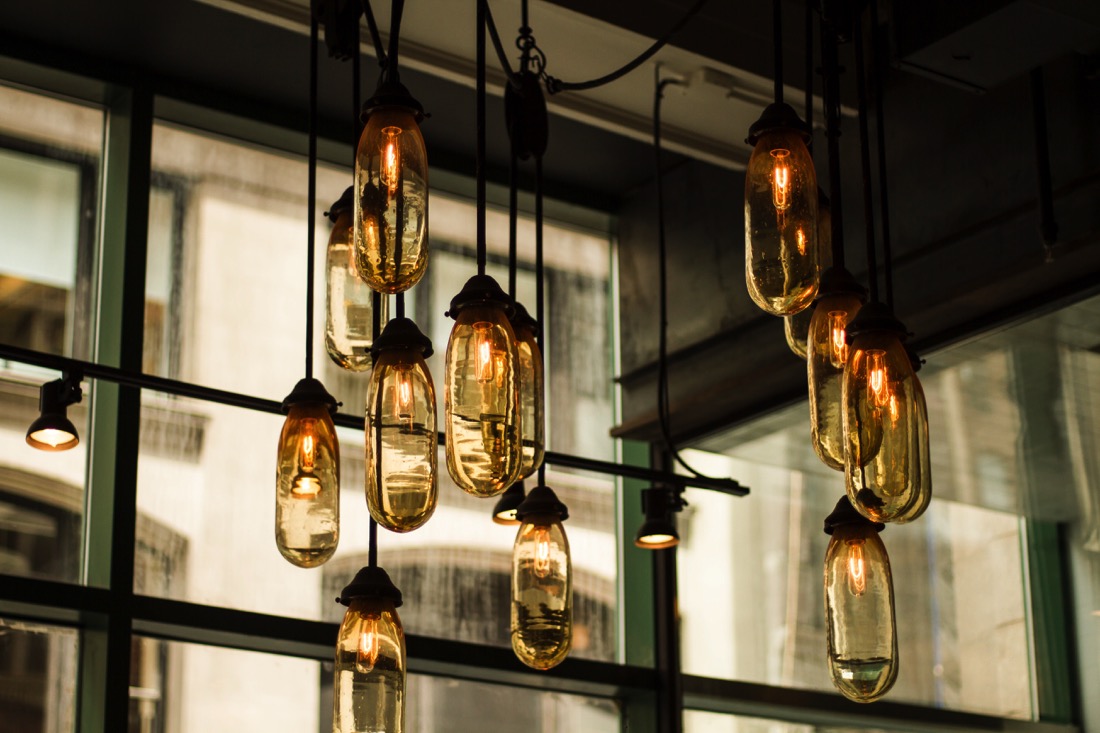
Tile Cutting Machine Water: The Essential Guide to Cooling, Lubrication & Dust Control
Tile cutting, whether for intricate mosaics or large-format porcelain slabs, is a precise and demanding task. While the cutting blade is the star, the unsung hero ensuring clean cuts, blade longevity, and operator safety is tile cutting machine water. This critical component is far more than just a liquid; it’s an integral part of the cutting process in wet tile saws and bridge saws. Understanding its roles, requirements, and management is paramount for achieving professional results, protecting expensive equipment, and safeguarding health. This comprehensive guide delves deep into the multifaceted world of tile cutting machine water, exploring its vital functions, system components, maintenance needs, water quality considerations, and environmental impact.
1. The Core Functions: Why Tile Cutting Machine Water is Non-Negotiable
Tile cutting machine water isn’t an optional add-on; it’s fundamental to the effective and safe operation of wet-cutting equipment. Its primary functions are interconnected and indispensable:
Cooling the Blade: Friction generated during cutting generates immense heat at the point of contact between the diamond blade and the tile. Without cooling, this heat would rapidly build up. Excessive heat is disastrous: it can glaze the diamond segments (rendering them ineffective), warp the blade core, and even cause catastrophic blade failure. Tile cutting machine water acts as a heat sink, absorbing this thermal energy and carrying it away, keeping the blade at an optimal operating temperature. Consistent cooling ensures the diamonds on the blade remain exposed and sharp, maximizing cutting efficiency and blade life.
Lubricating the Cut: The water acts as a lubricant between the blade and the tile material. This lubrication reduces friction beyond just cooling benefits. Reduced friction means:
Smoother cutting action with less resistance.
Significantly reduced chipping on both the tile surface and edges.
Less strain on the cutting machine’s motor and drive system.
Enhanced precision, especially for delicate cuts and brittle materials like glass or natural stone.
Suppressing Hazardous Dust: Cutting tiles, particularly ceramic, porcelain, and natural stone, generates respirable crystalline silica (RCS) dust. Silica dust is a severe health hazard, classified as a carcinogen, and prolonged exposure can lead to silicosis, lung cancer, and other respiratory diseases. Tile cutting machine water is the most effective on-tool dust control method. It captures dust particles at the source, binding them to the water and forming a slurry, drastically reducing the amount of harmful dust released into the air the operator breathes. This is arguably the most critical safety function of the water system. Proper water flow is essential for effective dust suppression.
2. Anatomy of a Wet Cutting System: How Tile Cutting Machine Water is Delivered
The effective application of tile cutting machine water relies on a well-designed system integrated into the cutting machine:
The Water Reservoir/Tank: This is the source of the water. Tanks vary significantly in size depending on the machine type (portable vs. stationary bridge saw). They need to be easily accessible for filling and cleaning. Some larger professional saws may even connect directly to a mains water supply with a continuous feed system, eliminating the need for a tank but requiring drainage management.
The Water Pump: Typically a small, submersible electric pump sits inside the reservoir. Its job is to draw water from the tank and pressurize it for delivery through the system. Pump reliability and sufficient flow rate (measured in gallons per hour – GPH or liters per minute – LPM) are crucial for consistent water delivery to the blade.
Delivery Hoses/Tubing: Flexible tubes carry the water from the pump to the cutting head or nozzle assembly. These need to be durable enough to withstand the workshop environment and resist kinking, which would restrict flow.
Flow Control Valve: This critical component, often a simple knob or lever, allows the operator to adjust the volume of water reaching the blade. Finding the right flow rate – enough for cooling and dust suppression without excessive splashback – is key. The optimal flow depends on the material being cut, the blade size, and the cut depth.
Water Nozzles/Spray Bars: This is the business end of the system. Nozzles are strategically positioned (usually above and sometimes below the blade) to direct a steady stream or spray of tile cutting machine water precisely onto the cutting point. Proper alignment is essential to ensure water hits both sides of the blade where it contacts the tile. Spray bars distribute water across a wider section of the blade. Nozzles can clog, so they often have removable tips for cleaning.
Splash Guards & Collection Trays: These components contain the water and slurry generated during cutting, directing it back towards the reservoir (in recirculating systems) or into a collection point for drainage. They minimize mess and help recover some water.
3. Water Quality Matters: What Goes Into Your Tile Cutting Machine
Not all water is created equal when it comes to tile cutting machine water. While plain tap water is commonly used, its quality can significantly impact performance and maintenance:
Impurities and Their Effects:
Dissolved Minerals (Hard Water): Calcium, magnesium, and other minerals can build up inside the pump, hoses, and especially the nozzles, restricting water flow over time. This scaling reduces cooling and dust suppression efficiency and can eventually damage the pump.
Sediment & Dirt: Particles in the water can accelerate nozzle clogging and act as abrasives inside the pump, potentially shortening its lifespan. Dirty water can also stain light-colored tiles (like marble or travertine) during cutting.
Biological Growth: Stagnant water in warm environments can promote algae or bacterial growth. This leads to slimy tanks, foul odors, and can clog the system. Biofilms can also harbor pathogens.
Recommended Water Types:
Softened Water: Reduces scale buildup significantly.
Filtered Water: Removes sediment and some dissolved solids.
Deionized (DI) or Reverse Osmosis (RO) Water: The purest options, virtually eliminating scale and sediment concerns. However, they can be more costly and require separate production systems. Often used in high-precision stone fabrication shops.
Clean Tap Water: Acceptable in many situations, especially for intermittent use, but requires more vigilant maintenance to combat scaling and biological growth.
Additives (Use with Caution): Some operators add small amounts of specific additives:
Rust Inhibitors: Can help protect metal parts within the pump and machine from corrosion, especially important if using pure water (which can be slightly corrosive) or if equipment sits unused.
Biocides/Algaecides: Used to prevent biological growth in the reservoir. Must be specifically designed for industrial water systems and used according to instructions. Avoid household cleaners or detergents, as they can foam excessively, damage pump seals, and potentially leave residues affecting the cut or tile surface.
4. Maintenance Imperative: Keeping Your Tile Cutting Machine Water System Running Smoothly
Neglecting the tile cutting machine water system leads to poor performance, blade damage, increased dust exposure, and costly repairs. Regular maintenance is non-negotiable:
Daily/Pre-Use Checks:
Water Level: Always ensure the reservoir has sufficient clean water before starting. Running the pump dry can destroy it in seconds.
Nozzle Alignment & Flow: Visually check that water is hitting the blade correctly on both sides at the cutting point. Adjust nozzles if necessary. Verify adequate flow using the control valve.
Obvious Leaks: Inspect hoses, connections, and the pump housing for leaks.
Regular Cleaning (Frequency Depends on Use):
Reservoir/Tank: Empty, scrub, and rinse the tank regularly to remove accumulated sediment and slime. Weekly cleaning is a good starting point for frequent users; more often for dirty environments or when cutting materials generating a lot of slurry. Let it dry if the machine won’t be used for an extended period.
Pump Intake/Filter Screen: Many pumps have a small screen over the intake. Clean this screen frequently to ensure unobstructed water flow to the pump.
Nozzles: Remove nozzles and clean the orifices with a pin or small wire. Soak in vinegar or a descaling solution if mineral deposits are present. Ensure they are clear before reinstalling.
Hoses: Flush hoses periodically. Check for cracks or kinks.
Splash Guards & Trays: Clean off accumulated slurry to maintain proper drainage and prevent overflow.
Dealing with Scale: If using hard water, periodic descaling is essential:
Fill the reservoir with a mixture of white vinegar and water (e.g., 1:1 ratio) or a commercial descaling solution.
Run the pump and let the solution circulate through the entire system for 15-30 minutes.
Drain completely, then flush thoroughly with clean water to remove all traces of acid.
Pump Care: Protect the pump from running dry and clean its intake. If performance drops significantly and cleaning doesn’t help, the pump may need replacement.
5. The Slurry Situation: Environmental Responsibility and Disposal
The mixture of tile cutting machine water, fine tile particles (including silica), and worn abrasive material from the blade creates tile cutting slurry. This waste stream requires responsible management:
Environmental Concerns: Silica dust, even when wet, can become airborne again if the slurry dries out. Dumping slurry directly into storm drains, sewers (without permission), or onto the ground is illegal in most areas and harmful to the environment. The fine particles can clog waterways and settle, damaging ecosystems. Heavy metals or other contaminants from certain tile glazes or stones might also be present.
Proper Disposal Methods:
Solidification & Landfill: The most common method. Allow the slurry to settle in a container. Decant the clearer water from the top (check local regulations regarding this water discharge – it often needs further treatment or evaporation). Mix the remaining sludge with a solidifying agent (like sawdust, cat litter, or commercial slurry solidifiers) until it forms a non-pourable cake. Dispose of the solidified waste in accordance with local construction waste landfill regulations.
Slurry Separation Systems: Professional workshops often invest in slurry separators or filter presses. These systems mechanically separate the solid waste from the water. The solids are bagged for landfill, and the filtered water can often be recycled back into the cutting machine (significantly reducing fresh water consumption) or discharged if it meets local water quality standards after treatment. These systems represent a significant upfront cost but offer long-term efficiency and environmental benefits.
Professional Waste Removal: Hire a licensed waste disposal company specializing in industrial sludge to collect and process the slurry.
Never Dump Improperly: Always prioritize compliant disposal methods. Check your local municipal and state/provincial environmental regulations for specific requirements regarding tile cutting slurry disposal.
Tile cutting machine water is far more than just a liquid coolant. It’s a vital system performing the essential, interlinked functions of blade cooling, cut lubrication, and critically, hazardous silica dust suppression. Understanding its roles, maintaining its delivery system (pump, hoses, nozzles, tank), managing water quality, and responsibly handling the resulting slurry are fundamental aspects of professional, efficient, and safe tile installation and fabrication. Investing attention and care into your tile cutting machine water system directly translates to sharper blades, cleaner cuts, longer machine life, reduced health risks, and responsible environmental practices. Never underestimate the power of proper water management in achieving flawless tile work.
continue reading
Related Posts
- 1631 words8.3 min read
- 1917 words9.7 min read