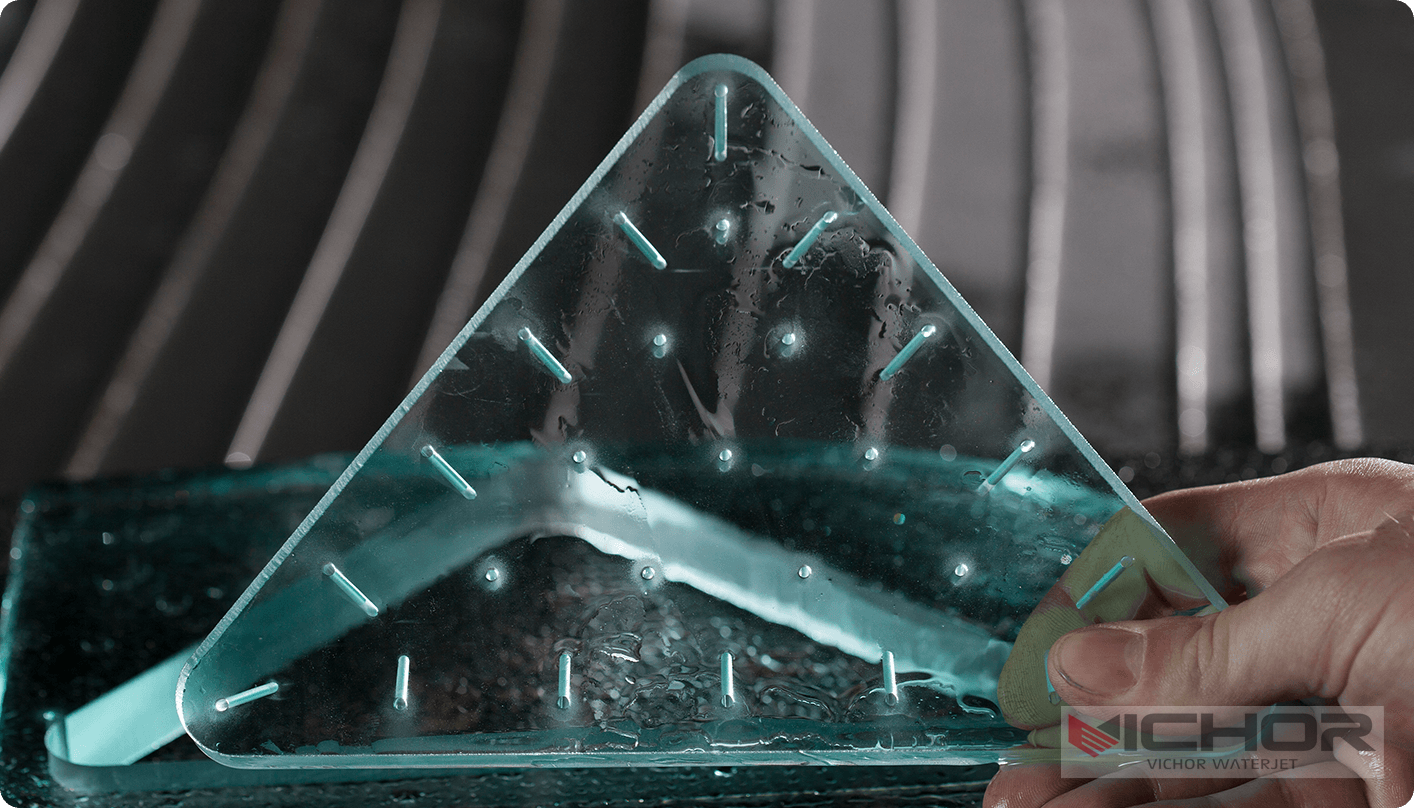
The Ultimate Guide to Waterjet Cutting Machines: Precision, Power & Versatility Unlocked
In the world of modern fabrication and manufacturing, precision, versatility, and the ability to handle diverse materials are paramount. Enter water cutting machines, also known as waterjet cutters, a technology that harnesses the incredible power of highly pressurized water, sometimes augmented with abrasives, to slice through virtually any material with astonishing accuracy and minimal thermal or mechanical stress. Unlike traditional cutting methods involving heat (lasers, plasma) or physical force (sawing, milling), water cutting machines offer a unique “cold cutting” process, opening doors to applications impossible with other technologies. This comprehensive guide dives deep into the fascinating world of waterjet cutting, exploring how it works, its key advantages, vast applications, and critical considerations for users.
How Waterjet Cutting Machines Work: Harnessing Nature’s Force
At the heart of every water cutting machine lies a surprisingly simple principle: extreme pressure creates extreme cutting power. However, the engineering required to achieve and control this pressure is highly sophisticated.
Ultra-High Pressure Generation: The process begins with an intensifier pump or a direct drive pump. An intensifier pump uses hydraulic oil acting on a large piston to drive a smaller piston pressurizing water. This amplification effect generates pressures typically ranging from 60,000 PSI (4,100 bar) to an astonishing 90,000 PSI (6,200 bar) or even higher. Direct drive pumps use advanced electric motors and crankshaft mechanisms to achieve similar pressures, often with higher efficiency and lower noise. This pressurized water is stored in an accumulator to ensure a smooth, pulsation-free flow.
The Jewel: The Orifice: The pressurized water is forced through a tiny orifice, usually made of diamond, sapphire, or ruby. This orifice, typically only 0.004″ to 0.016″ (0.10mm to 0.40mm) in diameter, focuses the high-pressure stream into a coherent, ultra-fast jet traveling at speeds exceeding Mach 3 (over 2,000 mph or 3,200 km/h).
Pure vs. Abrasive Waterjet:
Pure Waterjet Cutting: For soft materials like rubber, foam, gaskets, food products, thin plastics, and insulation, the pure, ultra-high-pressure water stream is sufficient. It produces a very fine, clean cut with minimal kerf (cut width).
Abrasive Waterjet Cutting: To cut hard materials (metals, stone, ceramics, glass, composites, thick plastics), an abrasive material, most commonly garnet sand, is introduced into the high-pressure water stream just after it exits the orifice. This happens in a mixing chamber. The abrasive particles are accelerated by the water jet, transforming it into a powerful erosive tool capable of slicing through inches of hardened steel or armor plate. The abrasive is fed into the mixing tube via a metering system and venturi effect created by the high-speed water.
Focusing the Stream: The Mixing Tube/Nozzle: After the abrasive is mixed in (for abrasive cutting), the combined stream travels through a mixing tube (also called a focus tube or nozzle), typically made of ultra-hard carbide or composite materials. This tube further focuses and stabilizes the abrasive-laden jet, ensuring its cutting effectiveness. The diameter of this tube largely determines the kerf width.
Motion Control: The high-pressure cutting head is mounted on a precision CNC (Computer Numerical Control) gantry system or robotic arm. This system moves the cutting head precisely according to digital design files (like CAD drawings), enabling complex 2D shapes and even 3D contours to be cut with high accuracy and repeatability. Advanced controllers manage the motion, pressure, abrasive feed rate, and cutting head height (Z-axis) for optimal results.
Pure Waterjet vs. Abrasive Waterjet: Choosing the Right Cutting Method
Understanding the distinction between pure and abrasive cutting is fundamental to effectively utilizing water cutting machines:
Pure Waterjet Cutting:
Mechanism: Relies solely on the kinetic energy of the ultra-high-pressure water stream.
Materials: Ideal for soft, easily erodible materials: Rubber, foam (all types), leather, paper/cardboard, thin plastics (<1/8″), food (pizza, cakes, frozen goods), diapers, gaskets, insulation, carpet, textiles.
Advantages: Extremely fine, clean cuts; very small kerf width; minimal material deformation; no heat affected zone (HAZ); very low operating cost (no abrasive); fast cutting on suitable materials; hygienic for food processing.
Disadvantages: Limited material thickness capability on soft materials; cannot cut hard materials effectively.
Abrasive Waterjet Cutting:
Mechanism: Combines the kinetic energy of high-pressure water with the erosive power of abrasive particles (usually garnet).
Materials: Capable of cutting an incredibly wide range of hard materials: Metals (steel, stainless steel, aluminum, titanium, brass, copper, tool steel), stone (granite, marble, tile), glass (toughened, laminated), ceramics, composites (carbon fiber, fiberglass), plastics (thick acrylic, PVC, Delrin), concrete, armor plate, exotic alloys.
Advantages: Cuts virtually any material regardless of hardness; “cold cutting” process – no Heat Affected Zone (HAZ), preserving material properties; no thermal distortion; no hazardous fumes/vapors; high precision and edge quality; ability to start cuts from the middle of a plate (piercing); excellent for thick materials (up to 12″+ in some metals, much thicker in softer materials).
Disadvantages: Wider kerf than pure waterjet or lasers; slower cutting speed compared to plasma or lasers on thinner metals (though faster on thick materials); higher operating cost due to abrasive consumption; generates a slurry waste stream requiring management; nozzle wear necessitates regular replacement.
The Unmatched Advantages of Waterjet Cutting Machines
Water cutting machines offer a compelling set of benefits that make them indispensable in many industries:
No Heat Affected Zone (HAZ): This is arguably the most significant advantage. Since waterjet cutting is a cold process, it does not generate heat that alters the metallurgical structure, hardens edges, creates micro-cracks, or causes warping/distortion in the material. This is crucial for heat-sensitive materials (like tempered glass, some plastics, heat-treated metals) and applications where material integrity is paramount (aerospace, tooling).
Material Versatility: One machine, one process, countless materials. From soft foam to hardened tool steel, granite to titanium, waterjet cutting machines handle them all without needing to change the fundamental cutting mechanism, only switching between pure water or adding abrasive. This eliminates the need for multiple dedicated cutting machines.
High Precision and Edge Quality: Modern CNC-controlled water cutting machines achieve impressive tolerances (typically +/- 0.003″ to +/- 0.005″ or better) and produce smooth edge finishes, often requiring little to no secondary finishing operations. Intricate details and complex geometries are easily achievable.
Minimal Mechanical Stress: Unlike sawing or milling, which impose significant mechanical forces and vibrations on the workpiece, waterjet cutting applies very little side force. This allows cutting delicate or thin materials without deformation and enables precise nesting of parts very close together, maximizing material utilization.
Environmentally Friendly Cutting: Waterjet cutting produces no hazardous fumes, vapors, or toxic gases (unlike plasma or laser cutting certain materials). The primary waste is a slurry of water, spent abrasive, and cut material particles, which can often be recycled or disposed of responsibly. The process itself uses water, a natural and abundant resource (though recycling systems are common).
Ability to Cut Thick Materials: While lasers struggle beyond a few inches and plasma edges become beveled, waterjet cutting machines excel at cutting very thick materials (e.g., 6-12+ inches of metal, much thicker stone or composites) with consistent edge quality and minimal taper (especially with dynamic head angling).
Omni-Directional Cutting: Waterjets can start a cut anywhere on the material surface (via piercing), enabling internal cutouts and complex nested patterns without pre-drilled starter holes, maximizing material yield.
Diverse Applications Across Industries: Where Waterjet Cutting Machines Shine
The unique capabilities of waterjet cutting machines make them vital across a staggering array of sectors:
Aerospace & Defense: Cutting intricate titanium, aluminum, and composite components for aircraft structures, engine parts (with no HAZ), armor plating, radomes, and insulation materials. Precision and material integrity are critical.
Automotive: Prototyping, gaskets, interior trim (foam, carpet, leather), airbag fabric, fiberglass components, filters, composite parts, and even cutting headliners and dashboards.
Architecture, Art & Monumental: Cutting intricate designs, lettering, and shapes in stone (granite, marble countertops, monuments), tile, glass (decorative panels, shower enclosures), and metal for sculptures, façades, signage, and interior design elements.
Manufacturing & Fabrication: General metal fabrication (steel, stainless, aluminum parts for machinery, frames, brackets), tool and die making, cutting gears, bearings, and complex parts from plate stock. Excellent for prototypes and low-volume production.
Electronics: Cutting circuit boards (prototyping), creating precise gaskets and seals from rubber/felt, cutting composite panels for enclosures, and trimming delicate components.
Food Processing: Hygienically cutting frozen foods (meat, fish, vegetables), baked goods (cakes, pizzas), and other food products without contamination or heat damage. Pure waterjet is ideal.
Medical Device Manufacturing: Cutting biocompatible materials (titanium, stainless steel, plastics) for implants, surgical tools, and device components with high precision and no thermal degradation. Cutting foam for prosthetics and padding.
Glass & Ceramics: Cutting tempered glass (safely, without shattering), laminated glass, ceramics, and porcelain tiles into complex shapes for architectural and decorative uses.
Composites: Cutting carbon fiber reinforced polymers (CFRP), fiberglass, Kevlar, and other composites without delamination, fraying, or heat damage, crucial for aerospace and high-performance automotive.
Packaging & Plastics: Cutting plastic sheets (acrylic, polycarbonate, PVC), creating molds and prototypes, and cutting dense foam for packaging inserts.
Material Compatibility: What Can Waterjet Cutting Machines Cut?
The list of materials compatible with water cutting machines is exceptionally broad. Here’s a more detailed breakdown:
Metals: Steel (mild, hardened, tool steel), Stainless Steel (all grades), Aluminum (all alloys and thicknesses), Titanium, Brass, Copper, Bronze, Inconel, Monel, Tungsten Carbide (thin), Lead, Armor Plate.
Stone & Tile: Granite, Marble, Slate, Sandstone, Limestone, Travertine, Engineered Stone, Porcelain Tile, Ceramic Tile.
Glass: Float Glass, Tempered Glass, Laminated Glass, Mirrored Glass, Patterned Glass.
Ceramics: Technical Ceramics, Porcelain, Brick, Refractory Materials.
Composites: Carbon Fiber Reinforced Polymer (CFRP), Fiberglass (GRP), Kevlar, Honeycomb Panels, Phenolics, Laminates.
Plastics & Polymers: Acrylic (PMMA), Polycarbonate, PVC, ABS, Nylon, Delrin (POM), Polyethylene (HDPE, UHMW), Polypropylene, Rubber (natural & synthetic), Foam (all densities – PU, PE, EVA, etc.), LEXAN, Gasket Materials (cork, fiber).
Textiles & Leather: Carpet, Felt, Upholstery Fabrics, Leather (all types), Canvas.
Paper & Cardboard: Thick cardstock, Corrugated Board, Paper Pulp Products.
Food: Frozen Meat, Fish, Poultry, Vegetables, Cheese, Baked Goods (Cakes, Bread, Pizza), Fruits.
Other: Wood (though not always the most efficient vs. saws), Concrete (thin sections), Asphalt.
Key Considerations When Using Waterjet Cutting Machines
While incredibly versatile, operating waterjet cutting machines effectively involves understanding several factors:
Operating Costs: Abrasive (garnet) consumption is the single largest ongoing cost for abrasive waterjet cutting. Pump maintenance (seals, filters, intensifier components), electricity (high-pressure pumps are power-hungry), nozzle/orifice wear (especially the orifice in pure waterjet), and water treatment/recycling also contribute. Pure waterjet costs are significantly lower.
Cutting Speed: Waterjet is generally slower than laser or plasma cutting on thin sheet metal (< 1/4″). However, its speed remains relatively constant regardless of material hardness, and it becomes significantly faster and more cost-effective than other methods on thicker materials (especially > 1/2″).
Kerf Width and Taper:
Kerf: The cutting stream creates a measurable cut width, wider than a laser beam. Kerf width depends on the orifice size, mixing tube diameter, material type, and thickness. This must be accounted for in part nesting and design (kerf compensation).
Taper: A natural characteristic where the top of the cut is slightly wider than the bottom, especially noticeable in thicker materials. Advanced machines use Dynamic Waterjet® technology or similar (tilting the cutting head slightly during the cut) to virtually eliminate taper and produce near-vertical edges.
Edge Finish: While generally smooth, the edge finish can vary. Pure waterjet produces very smooth edges on soft materials. Abrasive waterjet edges have a characteristic “satin” finish. The finish quality depends on material, cutting speed, abrasive type/grit size, and nozzle condition. Slower speeds yield smoother finishes. The edge is typically matte and ready for many applications, though polishing might be needed for cosmetic surfaces.
Noise and Slurry Management: Waterjet cutting generates significant noise (primarily from the pump and cutting stream), requiring hearing protection and potentially acoustic enclosures. The abrasive slurry waste requires a catcher tank and a filtration/recycling system or proper disposal methods. Dust extraction might be needed for certain materials.
Machine Footprint and Setup: Industrial water cutting machines require substantial floor space for the machine itself, the high-pressure pump unit (often separate), water supply/treatment, and slurry management system. Setup and calibration are crucial for achieving optimal precision.
Waterjet cutting machines represent a pinnacle of versatile, precise, and material-friendly cutting technology. By harnessing the power of ultra-high-pressure water, with or without abrasives, they overcome the limitations of thermal and mechanical cutting methods. The absence of a Heat Affected Zone, the unparalleled material versatility, the ability to cut thick sections with precision, and the environmentally conscious nature of the process solidify their position as indispensable tools in modern manufacturing, fabrication, art, and countless specialized fields.
Whether crafting intricate details in delicate stone, slicing through thick titanium for aerospace components, producing hygienic food cuts, or creating complex prototypes from diverse materials, water cutting machines offer a solution where others fall short. While considerations like operating costs and cutting speed play a role, the unique advantages and sheer breadth of application ensure that waterjet technology will continue to evolve and shape the future of cutting for years to come. For businesses seeking a single, powerful, and adaptable cutting solution, investing in a waterjet cutting machine is often a transformative decision.
continue reading
Related Posts
- 1136 words5.7 min read
- 1322 words6.7 min read
- 1730 words8.8 min read