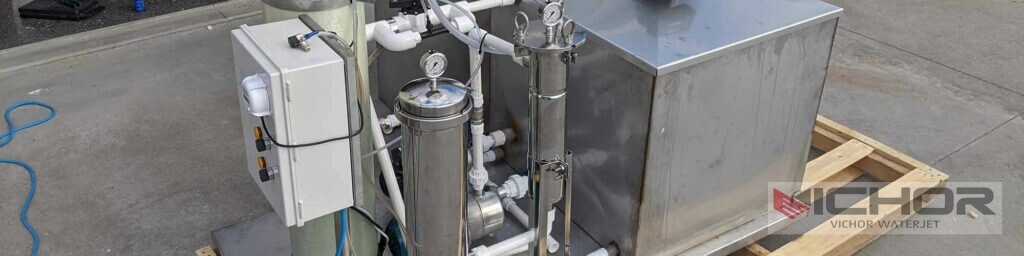
The Cutting Edge: How High-Pressure Water Cut Through Steel with Unmatched Precision
The concept of water cut through steel sounds like science fiction – a gentle stream slicing effortlessly through one of humanity’s strongest and most ubiquitous materials. Yet, this is not magic; it’s the remarkable reality of abrasive waterjet (AWJ) cutting, a technology revolutionizing manufacturing, fabrication, and art. This ultimate guide dives deep into the fascinating science and practical applications of how water cut through steel, exploring its principles, advantages, limitations, and diverse uses.
The Science Behind the Stream: How Water Cut Through Steel
At its core, the ability for water cut through steel relies on harnessing immense energy and a clever addition. Pure water, pressurized to astronomical levels (often 60,000 PSI and beyond), possesses significant kinetic energy. When forced through a tiny orifice (typically made of sapphire or diamond), this pressurized water accelerates to supersonic speeds, forming an incredibly coherent, pencil-thin jet.
However, while ultra-high-pressure water alone can cut softer materials like rubber, foam, or food, it lacks the necessary “bite” for hard metals like steel. This is where abrasives enter the picture. Garnet sand (a hard, naturally occurring mineral) is precisely metered into the supersonic water stream within a specialized mixing chamber. The accelerated water particles act as hammers, imparting their kinetic energy to the abrasive garnet particles. These energized abrasives become the microscopic chisels that perform the actual erosion and cutting work.
The process is fundamentally mechanical erosion, not melting or burning. As the abrasive-laden stream impacts the steel surface at incredible velocity, the hard garnet particles microscopically chip away at the material grain by grain. This cold-cutting mechanism is key to many of waterjet’s unique advantages. The synergy of the ultra-fast water carrier and the hard abrasive grit is what truly enables water cut through steel effectively and efficiently, transforming a fluid into an incredibly precise cutting tool.
The Mechanics of the Cut: Precision and Kerf
Understanding how the stream interacts with the steel provides insight into the precision achievable. As the abrasive waterjet plunges into the material:
Initial Impact Zone: The high-velocity stream creates immense localized pressure, initiating erosion immediately upon contact.
Cutting Zone: As the jet penetrates deeper, the abrasives continuously erode the material sideways and downwards. The surrounding water helps flush away the eroded particles (swarf) and cools the cut.
Kerf Formation: The path cut through the material is called the “kerf.” A waterjet kerf is typically very narrow, ranging from 0.020 inches to about 0.060 inches (0.5mm to 1.5mm), depending on the orifice/nozzle size, pressure, abrasive flow rate, and material thickness. This narrow kerf minimizes material waste.
Taper: A slight inherent taper often occurs in the kerf – it’s marginally wider at the top of the cut than at the bottom. This is due to the gradual dispersion of the jet’s energy as it travels deeper. Modern machines use sophisticated cutting head control (tilting or dynamic waterjet compensation) to minimize or even eliminate taper for critical applications, ensuring the process can water cut through steel with exceptional dimensional accuracy.
Edge Quality: The cut edge produced is typically smooth with a matte, satin-like finish. There is no Heat-Affected Zone (HAZ), meaning the steel’s microstructure and properties adjacent to the cut remain unchanged – a crucial factor for many applications. The edge quality can be fine-tuned by adjusting cutting speed, pressure, and abrasive quality.
Why Choose Waterjet? Advantages for Cutting Steel
The ability to water cut through steel offers a compelling set of advantages over traditional thermal cutting methods (like plasma or laser) and mechanical methods (like sawing or milling):
No Heat-Affected Zone (HAZ): This is arguably the most significant advantage. Plasma and laser cutting generate intense localized heat, melting the steel. This creates a HAZ where the material’s microstructure is altered, potentially leading to hardening, weakening, warping, or residual stresses. Waterjet’s cold-cutting process completely eliminates the HAZ, preserving the steel’s original temper, strength, and corrosion resistance. This is vital for critical structural components, tool steels, and hardened steels.
Material Versatility: While our focus is steel, the same machine that can water cut through steel can also cut virtually any other material – aluminum, titanium, copper, stone, glass, composites, rubber, plastics, ceramics, and even delicate materials like foam or food – simply by adjusting pressure and abrasives (or using pure water for soft materials). This eliminates the need for multiple dedicated cutting machines.
Exceptional Precision and Complexity: Waterjets are CNC-controlled, enabling incredibly intricate shapes and patterns with tight tolerances (± 0.003 inches or better is achievable). Sharp inside corners and complex geometries that are difficult or impossible with other methods are routine. It excels at cutting fine details, small holes, and intricate artwork from steel plate.
Minimal Mechanical Stress: Unlike sawing or punching, waterjet applies no significant mechanical force or vibration to the workpiece. This allows for cutting near edges, thin or delicate structures, and fixturing that might not withstand traditional machining forces. It also prevents work hardening in sensitive alloys.
Environmental & Safety Benefits: The process generates no hazardous fumes, gases, or molten spatter associated with thermal cutting. Dust is minimal and primarily contained within the cutting tank water. Garnet is non-toxic, though proper filtration and disposal of the abrasive slurry are necessary. Noise levels are generally lower than plasma cutting. The absence of heat also reduces fire risk.
Edge Quality: As mentioned, the cold-cut edge is clean, free of burrs (or easily removed), and ready for further processing or often even immediate use, saving time on secondary finishing operations.
The Machinery: Components Enabling Water to Cut Steel
The seemingly simple act of making water cut through steel requires sophisticated and robust equipment:
Ultra-High-Pressure Pump: The heart of the system. Uses either intensifier technology (hydraulic oil acting on a large piston to drive a smaller piston pressurizing water) or direct drive (crankshaft/rods driving plungers directly). Generates pressures from 40,000 PSI to over 90,000 PSI.
Abrasive Delivery System: Precisely meters dry garnet abrasive (typically 80 mesh for steel) from a hopper into the cutting head. Consistent flow is critical for cut quality and speed.
Cutting Head: Contains critical components:
Orifice: Tiny gem (sapphire, ruby, diamond) creating the initial ultra-fine, high-speed pure water jet.
Mixing Chamber: Where abrasive is entrained into the water jet under vacuum.
Focusing Tube (Nozzle): Typically made of tungsten carbide or synthetic diamond. Lengthens the coherent, abrasive-laden cutting stream and controls its diameter/quality. It’s a consumable part.
CNC Motion System: Precisely controls the movement of the cutting head over the workpiece (X, Y, Z axes). Advanced 5-axis systems allow for complex bevel cutting. Precision linear guides and ball screws are essential.
Cutting Table/Work Tank: Supports the workpiece and contains the high-energy jet and water/abrasive slurry after cutting. Equipped with water level control and often slats or a sacrificial grid to support the material.
Catcher Tank & Slurry Management: Located below the cutting table. Captures the spent water, abrasives, and cut material particles (swarf). Systems include settling tanks, cyclonic separators, and filters to recover water and abrasives (though garnet is typically single-use for precision cutting) and manage waste disposal.
Control System: Computer and software (CAD/CAM) for designing parts, generating cutting paths (nesting), controlling machine motion, pump pressure, abrasive feed, and monitoring the entire process.
Applications: Where Water Cutting Steel Shines
The unique capabilities of waterjet make it indispensable across countless industries where precision, no HAZ, and versatility in steel cutting are paramount:
Aerospace & Defense: Cutting high-strength alloys (titanium, Inconel), stainless steels, aluminum for structural components, engine parts, landing gear components, and armor plate without compromising material integrity.
Automotive: Prototyping, gaskets, brackets, suspension parts, decorative elements (especially stainless), and specialized tooling. Useful for cutting pre-hardened tool steels without annealing.
Machine Building & Tool & Die: Fabricating machine frames, bases, guards, complex gears, jigs, fixtures, and cutting intricate shapes from hardened tool and die steels without inducing stress or cracking. Essential for mold making.
Architecture & Construction: Creating intricate decorative steel panels, railings, balustrades, signage, structural components with complex profiles, and stainless steel cladding elements.
Energy (Oil & Gas, Nuclear): Cutting thick plate for pressure vessels, flanges, pipe supports, valve components, and heat exchangers, especially in corrosion-resistant alloys where HAZ is unacceptable. Cutting in hazardous environments due to lack of sparks/heat.
Medical Device Manufacturing: Cutting surgical instruments, implants (from biocompatible stainless steels), and device components requiring absolute precision and pristine, uncontaminated edges.
Art & Sculpture: Enables artists to create incredibly detailed and complex sculptures, wall art, and installations from steel sheet and plate, pushing creative boundaries.
Understanding the Limits: Speed, Thickness, and Cost
While remarkably versatile, waterjet isn’t always the fastest or cheapest solution for every steel cutting job:
Cutting Speed vs. Thickness: Waterjet cutting speed is significantly slower than plasma or laser for thin steel (e.g., < 1/2 inch / 12mm). While it can water cut through steel over 12 inches (300mm) thick, the cutting speed decreases dramatically with increasing thickness. Laser and plasma are generally faster for thicker sections too, though waterjet excels where HAZ is critical regardless of thickness.
Operating Costs: Consumables (orifice, focusing tube, abrasives) represent a significant ongoing cost. Garnet is the major expense. Pump maintenance and high energy consumption (to generate ultra-high pressure) also contribute. Initial machine investment is generally higher than plasma, comparable to or less than high-end lasers.
Accuracy Limitations (Extreme Precision): While highly precise, for tolerances tighter than a few thousandths of an inch, precision machining (milling, grinding) might still be required as a secondary operation.
Material Properties: Extremely hard materials (like some ceramics or carbides) or very thick, dense sections can push the limits of practical cutting speed and cost-effectiveness compared to other methods.
Slurry Handling: Managing and disposing of the abrasive-laden water slurry requires proper systems and environmental consideration.
The technology enabling water cut through steel represents a pinnacle of precision cold-cutting. By combining the brute force of ultra-high-pressure water with the focused erosion of abrasive particles, waterjet machining delivers unparalleled versatility and preserves the integrity of materials like steel. Its advantages – no HAZ, exceptional precision, complex geometry capability, minimal stress, and multi-material capacity – ensure its vital role in modern manufacturing, art, and innovation.
As pump pressures continue to rise, control systems become more sophisticated (with AI integration for process optimization), and abrasive delivery becomes even more precise, the boundaries of what waterjet can achieve will expand further. The ability to water cut through steel cleanly, accurately, and without thermal distortion isn’t just a technological marvel; it’s a fundamental tool shaping the future of fabrication across countless industries, proving that sometimes, the most powerful cut comes from the most fluid source.
continue reading
Related Posts
- 1254 words6.3 min read
- 1559 words7.8 min read