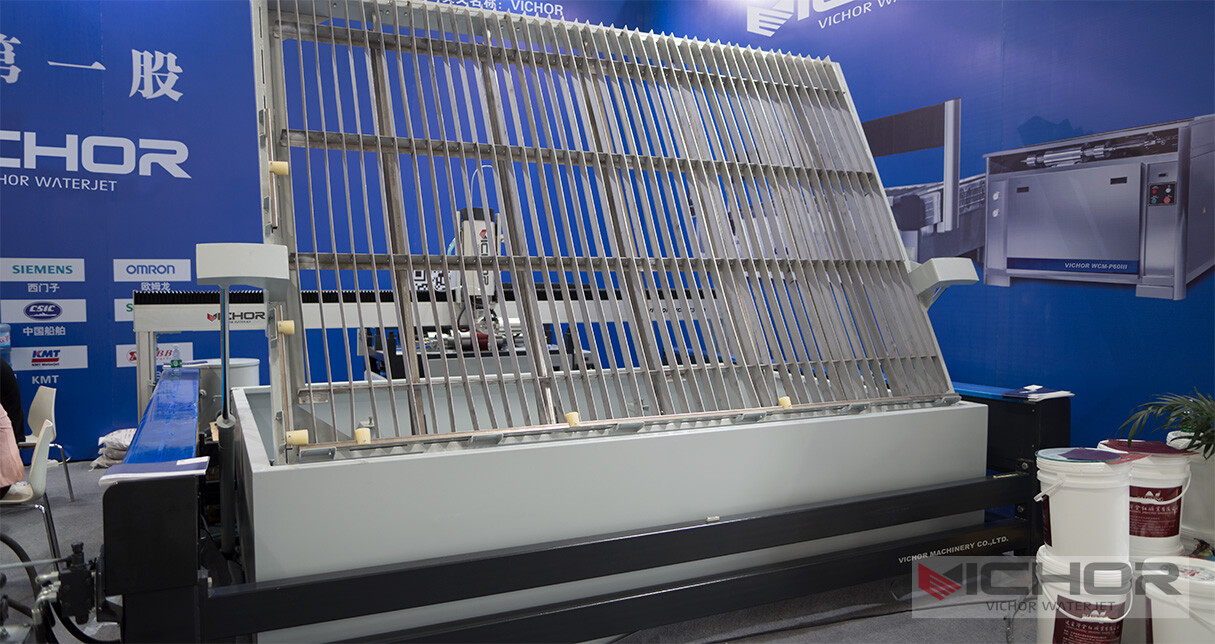
Small Waterjet Cutter: The Compact Powerhouse for Precision Cutting
For decades, waterjet cutting technology has been synonymous with industrial might, capable of slicing through thick metal plates with astonishing precision. But what about smaller workshops, labs, artists, or businesses needing intricate cuts without the footprint of a behemoth? Enter the small waterjet cutter – a revolution in accessibility and versatility, bringing the incredible power of abrasive waterjet technology to a much wider audience. This ultimate guide explores why compact waterjet systems are becoming indispensable tools across diverse fields.
1. What Exactly is a Small Waterjet Cutter? Demystifying the Technology
At its core, a small waterjet cutter utilizes the same fundamental principle as its larger counterparts: harnessing the immense power of ultra-high-pressure water. Water is pressurized to levels exceeding 60,000 PSI (often reaching 90,000 PSI in modern systems) and forced through a tiny, precision gem orifice (typically ruby or diamond), creating a supersonic stream. For cutting harder materials like metals, stone, glass, or composites, an abrasive material (usually garnet sand) is introduced into this stream within a mixing tube. The resulting abrasive waterjet acts like a microscopic, high-velocity saw, eroding material with exceptional precision and minimal heat-affected zone (HAZ).
The “small” designation primarily refers to:
Physical Footprint: Significantly reduced machine size, often designed to fit into garage workshops, university labs, or small manufacturing cells.
Cutting Envelope: A smaller X-Y cutting area (e.g., 2′ x 2′, 2′ x 4′, 4′ x 4′ are common for compact models) compared to industrial machines that might handle 10′ x 20′ or larger plates.
System Capacity: Lower horsepower intensifier pumps (e.g., 30HP, 50HP) compared to 100HP+ industrial pumps, translating to lower operating costs and utility requirements.
Target Material Thickness: While capable of impressive cuts, small waterjet cutters are typically optimized for materials ranging from thin foils up to around 2-3 inches thick, depending on the material and specific machine power, rather than the 6-12+ inches tackled by massive industrial systems.
This miniaturization doesn’t compromise core accuracy; modern small waterjet cutter systems still deliver tolerances within ±0.003″ to ±0.005″ and produce smooth, burr-free edges.
2. Why Choose a Small Waterjet Cutter? Key Advantages Over Alternatives
The rise of the small waterjet cutter isn’t just about size; it’s about unlocking unique capabilities previously unavailable or impractical for smaller operations:
True Cold Cutting: The waterjet process generates negligible heat. This is crucial for materials sensitive to heat distortion or hardening, like aerospace alloys (titanium, Inconel), tempered glass, certain plastics (acrylic doesn’t melt), and exotic composites. Lasers and plasma cutters simply can’t match this.
Unmatched Material Versatility: A single small waterjet cutter can effortlessly switch between cutting stainless steel, aluminum, brass, copper, stone, tile, glass, rubber, foam, plastics, laminates, carbon fiber, and even food products (using pure water) – all without changing tools. This eliminates the need for multiple dedicated machines.
Exceptional Precision and Edge Quality: Capable of intricate contours, sharp corners, and fine details with smooth, sandblasted finishes right off the machine. Minimal secondary finishing is often required. Kerf width is small and consistent.
Minimal Material Waste: The narrow kerf (typically 0.030″ to 0.050″ with abrasive) and intelligent nesting software allow for highly efficient material utilization, especially important for expensive stock.
Reduced Operating Costs (Compared to Large Waterjets): Lower initial investment, significantly reduced power consumption (smaller pump), less abrasive consumption (due to smaller orifice/mixing tube and thinner materials), and lower facility requirements (no massive foundation, standard electrical hookups often suffice).
Ease of Use & Automation: Modern small waterjet cutter systems feature intuitive CAD/CAM software, making programming accessible. Many offer semi-automated or fully automated abrasive loading systems and tank cleaning, reducing labor intensity.
Compared to CNC routers, lasers, or plasma cutters, the small waterjet cutter offers a unique combination of cold cutting and extreme material versatility that makes it irreplaceable for many applications.
3. Where Are Small Waterjet Cutters Used? Diverse Applications Unleashed
The accessibility of the small waterjet cutter has opened floodgates for innovation across countless sectors:
Prototyping & R&D Labs: Rapidly iterate complex metal, plastic, and composite prototypes without heat distortion. Perfect for universities and product development teams. A small waterjet cutter fits neatly in the lab.
Job Shops & Contract Manufacturing: Handle diverse short-run jobs and custom parts for various industries without needing multiple machines. Offer unique capabilities competitors might lack.
Aerospace & Defense (Small Parts): Precision cutting of intricate components from titanium, aluminum alloys, and composites for drones, satellites, avionics housings, and specialized tooling. The cold cut preserves material integrity.
Automotive (Custom & Aftermarket): Create custom brackets, gaskets (from various materials), intricate interior components, signage, and specialized tools. The small waterjet cutter handles mixed materials effortlessly.
Art, Architecture & Signage: Produce stunningly detailed sculptures, intricate metal artwork, architectural models, decorative panels (metal, stone, glass), and complex signage letters with perfect edges.
Electronics: Cut precise enclosures, heatsinks, insulators, and shielding components from metals and specialized plastics without thermal damage.
Medical Device Manufacturing: Fabricate intricate surgical tools, implants (trial components), device housings, and components from biocompatible metals and plastics with critical precision and no HAZ.
Glass & Stone Fabrication: Cut sinks, intricate tile designs, decorative glass panels, tabletops, and mosaics with chipping-free edges. A small waterjet cutter is ideal for boutique fabrication.
Education: Teach advanced manufacturing principles, CAD/CAM, and material science with a safe, versatile, and highly engaging tool.
4. Key Features to Consider When Choosing a Small Waterjet Cutter
Not all compact systems are created equal. Key specifications to evaluate include:
Pump Power & Pressure: Higher horsepower (e.g., 50HP vs 30HP) and pressure (e.g., 60k vs 90k PSI) enable faster cutting speeds and the ability to tackle thicker, harder materials more effectively. Direct-drive pumps are often preferred for compact systems due to efficiency and lower noise.
Cutting Envelope (Table Size): Match the X-Y travel to the largest parts you anticipate producing, considering both part size and efficient nesting potential. Ensure adequate Z-axis height for your material stack-ups and nozzle assemblies.
Motion System & Accuracy: Look for robust linear guides (preferably pre-loaded), high-quality ball screws or linear motors, and a rigid gantry structure. Resolution and repeatability specs are critical. Dynamic waterjet head height control (5-axis or Z-AWC) is a major advantage for maintaining cut quality on warped or beveled surfaces.
Control System & Software: User-friendly, industry-standard CAD/CAM software is essential. Look for features like automatic kerf compensation, nesting optimization, cut path simulation, and straightforward machine control. Compatibility with common file formats (DXF, DWG, STEP, etc.) is a must.
Abrasive Delivery System: Efficient, consistent abrasive metering is vital for cut quality and cost control. Compare hopper sizes, metering mechanisms, and ease of refilling. Some small waterjet cutter models offer fully automated systems.
Cutting Head Technology: Quality of the orifice, mixing tube, and focusing nozzle directly impacts cut quality, speed, and consumable life. Ease of maintenance and replacement is important.
Tank Design & Material Handling: Consider ease of loading/unloading material, tank drainage, sludge removal systems, and overall durability. Water management systems (filtration, chilling) impact performance and consumable life.
Footprint & Facility Requirements: Precisely measure your available space, including access for installation. Verify electrical needs (voltage, phase), water supply/drainage, and potential noise considerations.
5. Getting Started with a Small Waterjet Cutter: Implementation & Best Practices
Integrating a small waterjet cutter successfully involves careful planning:
Thorough Needs Assessment: Define your primary materials, typical thicknesses, required tolerances, part sizes, and desired production volume. Be realistic about growth projections.
Space & Infrastructure Prep: Ensure adequate floor space (including clearance around the machine for operation and maintenance), proper electrical supply (consult manufacturer specs), reliable water source and drainage, and potentially a chiller unit. Adequate ventilation is recommended. The small waterjet cutter still needs proper setup.
Operator Training: Invest in comprehensive training from the manufacturer or supplier. Operators need to understand machine operation, software programming, basic maintenance, safety protocols, and troubleshooting.
Material Handling: Plan how materials will be stored, transported to the machine, loaded, and how cut parts and skeletons will be removed and handled safely.
Consumables Management: Establish reliable suppliers for high-quality abrasives (garnet), orifices, mixing tubes, and high-pressure seals. Monitor usage rates and costs.
Water Management: Implement a water recycling or filtration system if possible to reduce waste and disposal costs. Properly manage the abrasive sludge generated.
Safety First: Strictly adhere to all safety guidelines. The high-pressure water stream is extremely dangerous. Always wear appropriate PPE (safety glasses, hearing protection, steel-toed boots). Implement lockout/tagout procedures. Never bypass safety interlocks. Ensure the cutting chamber door is closed during operation.
Start Simple: Begin with less complex parts and easier materials to build operator confidence and understand the machine’s capabilities before tackling highly intricate or challenging jobs.
Preventive Maintenance: Religiously follow the manufacturer’s maintenance schedule for the pump, cutting head, motion system, and filtration units to ensure reliability, longevity, and consistent cut quality. Regular maintenance is key for any small waterjet cutter.
The small waterjet cutter represents a democratization of one of the most powerful and versatile cutting technologies available. By packing immense capability into a manageable footprint and cost structure, it empowers makers, innovators, small manufacturers, and specialized industries to achieve results previously out of reach. Its unique combination of cold cutting, unparalleled material versatility, high precision, and relatively low operating costs makes it not just an alternative, but often the optimal solution for a vast range of cutting challenges. As technology continues to advance, making these systems even more user-friendly, efficient, and affordable, the adoption of the small waterjet cutter is poised to accelerate, reshaping the landscape of precision fabrication for years to come. Whether you’re crafting intricate art, prototyping the next breakthrough, or manufacturing critical small components, this compact powerhouse offers a world of possibilities.
continue reading
Related Posts
- 2225 words11.2 min read
- 1448 words7.3 min read