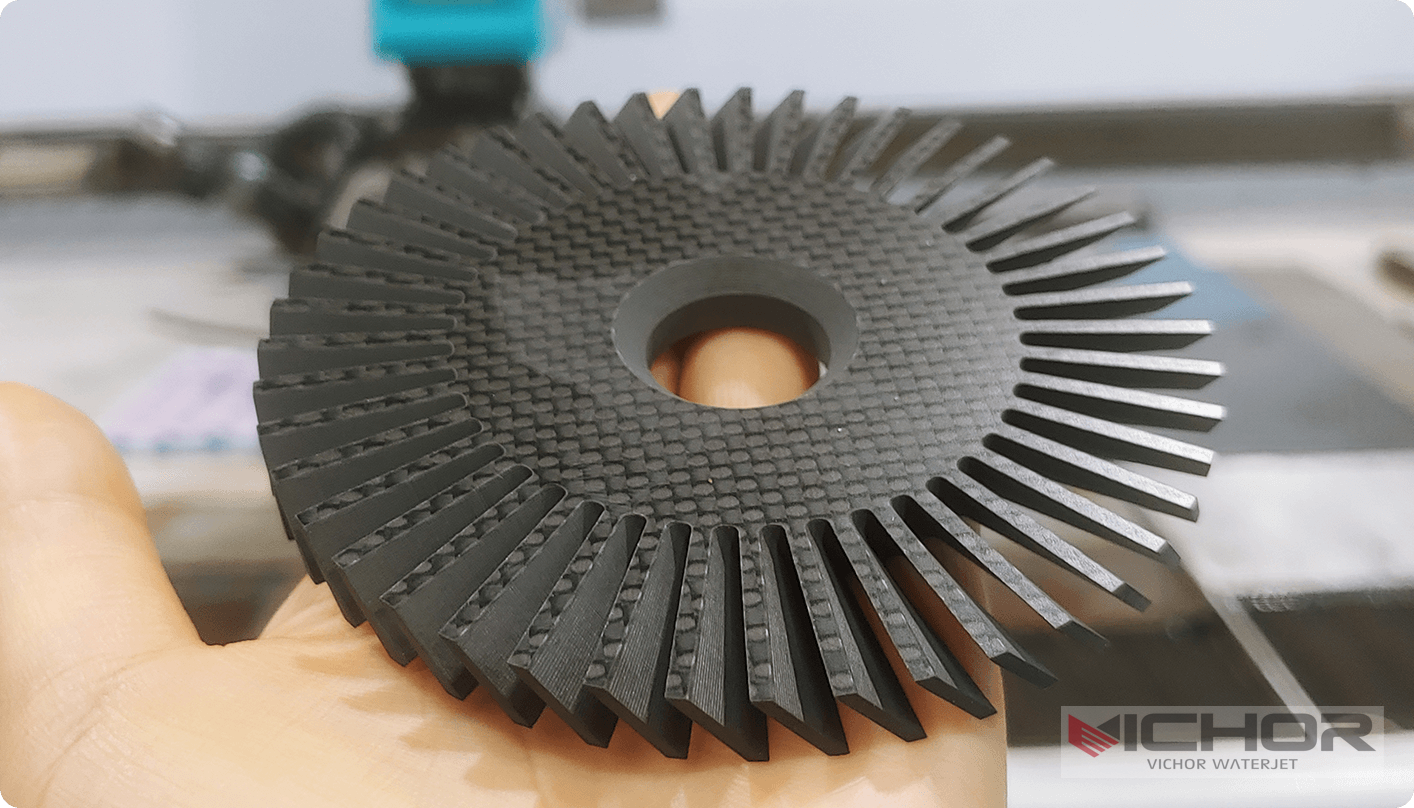
In the world of manufacturing, prototyping, signage, packaging, and countless other industries, foam materials like EPS, polyurethane, EPP, and specialized composites are indispensable. Cutting these materials cleanly, accurately, and without thermal damage or excessive waste is paramount. This is where Foam Water Jet Cutting Service providers step in, offering a superior solution that combines unmatched precision with incredible versatility. This article delves deep into the world of professional foam water jet cutting service, exploring its technology, benefits, applications, and why it’s often the optimal choice.
Understanding the Core Technology
At its heart, waterjet cutting is a cold cutting process that utilizes an extremely high-pressure stream of water, often mixed with an abrasive garnet, to erode material. However, for softer materials like foam, the process frequently employs “pure waterjet” cutting. This means:
Ultra-High Pressure: Specialized pumps intensify water pressure to levels exceeding 60,000 PSI (often 60,000 – 90,000 PSI).
Fine Orifice: This pressurized water is forced through a tiny gem orifice (typically diamond or sapphire), creating a coherent, ultra-high-velocity water stream.
Pure Water Stream: For foam cutting, abrasive grit is usually unnecessary. The pure water stream itself possesses enough kinetic energy to cleanly slice through the material.
CNC Precision: The cutting head is mounted on a sophisticated Computer Numerical Control (CNC) gantry system. This system interprets CAD drawings (DXF, DWG, etc.) and moves the cutting head with exceptional accuracy (often within +/- 0.005 inches or better) along the programmed path.
Minimal Kerf: The water stream itself is very thin (0.010″ to 0.040″ typically for pure waterjet on foam), resulting in minimal material waste (“kerf”) and allowing for intricate cuts and nesting of parts.
The “cold” nature of the process is crucial for foam, preventing melting, warping, or toxic fume generation associated with thermal methods like lasers or hot wires.
Compatible Foam Materials: A Wide Spectrum
One of the standout advantages of using a professional foam water jet cutting service is its remarkable material compatibility. It handles virtually any foam type with ease:
Expanded Polystyrene (EPS): Commonly used for packaging, insulation, and lightweight models. Waterjet cuts complex shapes without crumbling edges.
Extruded Polystyrene (XPS): Higher density than EPS, used for insulation boards, architectural models. Waterjet provides clean, precise cuts.
Polyurethane Foam (PU): Ranges from soft, flexible foams (packaging, filtration, seating) to rigid foams (insulation, structural cores). Waterjet excels at contouring and sculpting both types.
Expanded Polypropylene (EPP): Known for its resilience and energy absorption (automotive parts, packaging, reusable containers). Waterjet cleanly cuts its often-tough cellular structure.
Polyethylene Foam (PE): Cross-linked (XLPE) or non-cross-linked (LDPE, HDPE). Used for flotation, padding, insulation. Waterjet avoids tearing or compressing the material.
Specialty Foams: Including PVC foams (Sintra, Komatex – often used for signage), acoustic foams, filtration foams, and composite foam cores (like those used in marine and aerospace sandwich panels). Waterjet handles their unique properties effectively.
Laminated Foams: Cutting through foam layers bonded to other materials (fabrics, films, metals) in a single pass is a significant strength of waterjet.
A reliable foam water jet cutting service will have experience with this vast array, understanding the nuances of cutting each type for optimal results.
Key Advantages Over Alternative Cutting Methods
Why choose a foam water jet cutting service over other common foam fabrication methods? The benefits are compelling:
No Heat-Affected Zone (HAZ): Unlike laser cutting, plasma cutting, or hot wire cutting, waterjet produces zero thermal distortion. Edges remain pristine, with no melting, burning, or toxic fumes. Material properties are unchanged right up to the cut edge.
Exceptional Precision and Complexity: CNC control allows for cutting intricate 2D profiles, sharp corners, fine details, and complex geometries impossible with manual methods or difficult with routers. Tolerances are consistently tight.
Minimal Material Stress: The water stream applies negligible lateral force on the material. This prevents compression, tearing, or delamination common with blade-based CNC routers or die cutting, especially on softer or more fragile foams.
Versatility in Thickness: Waterjet can effectively cut foam from thin sheets (less than 0.5 inches) up to very thick blocks (12 inches, 24 inches, or even more, depending on the machine). No need for multiple passes or specialized tooling changes.
Fast Setup and Prototyping: Changing from one job to another primarily involves loading a new CAD file. There’s no need for custom dies (like in die cutting) or specialized tooling (like specific router bits). This makes it ideal for rapid prototyping and low-to-medium volume production runs.
Clean Cuts and Smooth Edges: Pure waterjet cutting on foam typically produces smooth, sealed edges requiring little to no secondary finishing. This is a significant advantage over methods that can leave rough, furry, or open-cell edges.
Reduced Waste (Kerf & Nesting): The thin kerf width minimizes material loss. Advanced nesting software used by foam water jet cutting service providers optimizes part placement on the raw sheet or block, further maximizing material yield and reducing costs.
Environmentally Friendlier: The primary consumable is water (often recycled within the machine). No toxic fumes are generated. Abrasive, if used minimally for denser composites, is typically non-toxic garnet sand.
Diverse Applications Across Industries
The unique capabilities of foam water jet cutting service make it invaluable across numerous sectors:
Packaging: Creating custom protective inserts for electronics, medical devices, fragile items, and industrial equipment. Complex shapes cradle products perfectly.
Signage & Display: Precision cutting of PVC foams (Sintra, Komatex), EPS letters, and intricate display components with smooth, ready-to-paint or laminate edges.
Architectural Models & Prototyping: Accurately fabricating detailed scale models of buildings, landscapes, and products from various rigid foams.
Aerospace & Marine: Cutting core materials (like PVC or PU foams) for composite sandwich panels used in aircraft components, boat hulls, and decks. Contouring insulation panels.
Automotive: Prototyping and production of interior components (headliners, door panels), acoustic insulation parts, protective packaging, and EPP energy absorbers.
Foundry & Casting: Creating precise EPS and EPP patterns and cores for investment casting and evaporative foam casting (Lost Foam).
Themed Entertainment & Props: Sculpting large EPS blocks for scenic elements, sculptures, and props. Creating detailed models and set pieces.
Filtration: Cutting intricate shapes from open-cell polyurethane and other filter foams.
Gaskets & Seals: Prototyping and low-volume production of foam gaskets and seals with complex profiles.
Medical & Healthcare: Fabricating components for prosthetics, orthotics, medical device packaging, and padding from specialized medical-grade foams.
Choosing the Right Foam Water Jet Cutting Service Provider
Not all waterjet shops are created equal, especially when focusing on foam. Here’s what to look for when selecting a foam water jet cutting service partner:
Specific Foam Expertise: Ensure they have extensive experience cutting the specific types of foam you use. Handling EPS effectively is different from cutting dense XLPE or laminated composites.
Pure Waterjet Capability: Verify they utilize pure waterjet cutting for foam. While abrasive jets are powerful, they are generally overkill and less desirable for most foams, potentially causing more kerf and edge roughness.
Machine Size & Capacity: Confirm their machine bed size accommodates your largest parts or sheets and can handle the thicknesses you require.
Precision & Tolerance Capability: Discuss their standard tolerances and if they can meet your specific accuracy requirements. Look for modern CNC controls.
CAD/CAM & Nesting Software: They should be proficient with industry-standard CAD file formats and utilize efficient nesting software to minimize your material costs.
Material Handling: How do they handle and support large or thick foam blocks during cutting to prevent deflection or vibration?
Secondary Services: Do they offer value-added services like light finishing, laminating before/after cutting, assembly, or packaging that could streamline your process?
Quality Control: Inquire about their quality assurance processes to ensure parts meet specifications consistently.
Communication & Customer Service: Responsiveness, clear communication, design for manufacturability (DFM) feedback, and project management are crucial.
Competitive Pricing & Turnaround: Get quotes, but balance cost with the quality, expertise, and reliability the foam water jet cutting service provides. Understand their standard lead times.
When precision, complexity, material integrity, and versatility are non-negotiable for your foam components, partnering with a professional foam water jet cutting service is the intelligent solution. It overcomes the limitations of traditional foam cutting methods by delivering cold, stress-free cuts with exceptional accuracy across a vast range of foam types and thicknesses. From intricate packaging inserts and detailed architectural models to critical aerospace cores and large-scale props, waterjet technology unlocks design possibilities while ensuring high-quality results. By carefully selecting a foam water jet cutting service provider with the right expertise and capabilities, manufacturers, designers, and engineers can significantly enhance their product quality, reduce waste, accelerate prototyping, and achieve greater production flexibility. For complex foam shapes, waterjet cutting isn’t just an option; it’s often the superior process.
continue reading