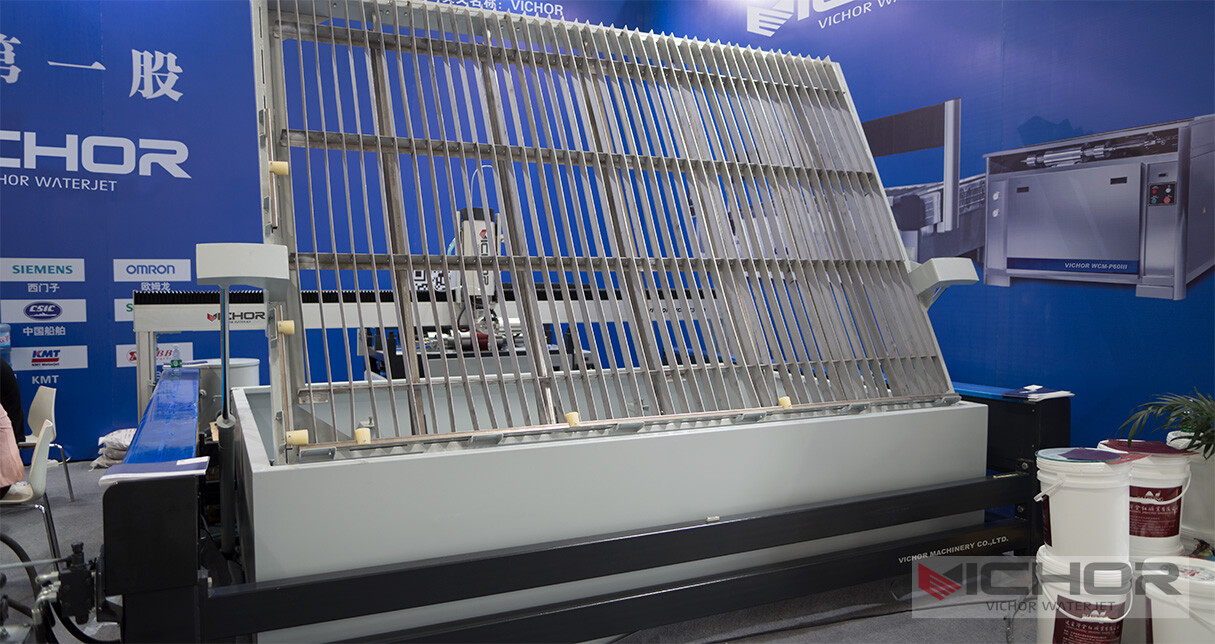
Cut Jet Technology Explained: How Waterjet Cutting Works & Its Benefits
In the world of precision manufacturing and fabrication, few technologies offer the versatility and power of cut jet systems, commonly known as waterjet cutting. This remarkable process harnesses the immense energy of ultra-high-pressure water, often mixed with abrasive particles, to slice through virtually any material with astonishing accuracy and minimal thermal distortion. From intricate aerospace components to rugged architectural stonework, cut jet technology has revolutionized how industries approach cutting tasks. This comprehensive guide delves deep into the workings, advantages, applications, and critical considerations of cut jet systems, providing a clear understanding of why this technology is a cornerstone of modern manufacturing.
1. The Fundamental Principles of Cut Jet Technology
At its core, a cut jet system is deceptively simple yet incredibly sophisticated. It starts with a high-pressure pump, typically intensifier-based or direct-drive, capable of generating pressures ranging from 40,000 psi (2,750 bar) up to an astonishing 90,000 psi (6,200 bar) or more. This pump forces ordinary tap water through a tiny orifice, usually made of sapphire or diamond, converting the high pressure into an extremely high-velocity stream – often exceeding Mach 3 (three times the speed of sound).
For cutting harder materials like metals, stone, or composites, an abrasive material (most commonly garnet sand) is introduced into this supersonic water stream within a specialized mixing tube. The water stream accelerates the abrasive particles, transforming the cut jet into a potent erosive tool. For softer materials like foam, rubber, or food products, pure waterjets without abrasive are used. The kinetic energy transfer from the water and abrasive to the workpiece is what enables the cut jet to make such precise and clean cuts with remarkably little force exerted on the material itself.
2. The Mechanics: How a Cut Jet System Actually Cuts
Understanding the cutting mechanics reveals the brilliance of cut jet technology. The process involves several key stages:
Pressurization: The pump creates the ultra-high pressure needed.
Orifice Acceleration: Water forced through the orifice forms a coherent, high-velocity stream.
Abrasive Induction (Abrasive Jet Only): Abrasive is drawn into the stream via a venturi effect in the mixing chamber.
Focusing & Mixing: The water and abrasive mix thoroughly within the focusing (mixing) tube, creating the effective cutting tool.
Material Erosion: The high-velocity abrasive particles impact the workpiece surface at extreme speed, causing micro-chipping and erosion along the desired cut path.
Kerf Formation & Swarf Removal: The cut jet continuously removes material, creating a cut path (kerf). The spent water, abrasive, and eroded material (swarf) are captured in a catcher tank below the workpiece.
The cutting head, controlled by a CNC (Computer Numerical Control) system, moves precisely according to programmed paths, enabling complex 2D and 3D shapes to be cut. The cutting speed, pressure, abrasive flow rate, and nozzle standoff distance are all critical parameters optimized for the specific material and desired cut quality. The lack of a heat-affected zone (HAZ) is a defining characteristic, as the cut jet process is primarily mechanical erosion, not thermal melting or burning.
3. Material Versatility: What Can a Cut Jet Cut?
This is where cut jet technology truly shines. Its ability to cut an exceptionally wide range of materials is unparalleled:
Metals: Steel (mild, tool, hardened, stainless), aluminum, titanium, copper, brass, bronze, Inconel, tungsten. Thicknesses range from thin foils to slabs exceeding 10 inches (250mm+).
Stone & Tile: Granite, marble, slate, limestone, travertine, engineered stone, ceramic, and porcelain tile – ideal for intricate countertops, inlays, and architectural features.
Glass: Thick or thin, laminated or tempered (edge starting required) – used for decorative panels, signage, and industrial components.
Composites: Carbon fiber reinforced polymer (CFRP), fiberglass, Kevlar, laminates – crucial for aerospace and automotive parts without delamination.
Plastics & Rubber: Acrylic, polycarbonate, PVC, UHMW, neoprene, silicone – cut cleanly without melting or toxic fumes.
Foams: Polyurethane, polystyrene, foam rubber – perfect for packaging, insulation, and modeling.
Food: Ideal for portioning frozen foods, baked goods, or delicate items without contamination (using pure waterjet).
Exotics: Materials like ballistic armor, titanium alloys, and sensitive explosives can be cut safely where thermal processes fail.
The cut jet’s cold-cutting nature means no material alteration due to heat, preserving the inherent properties of even the most sensitive alloys or composites.
4. Key Advantages and Benefits of Using Cut Jet Technology
Choosing cut jet cutting offers numerous compelling benefits over laser, plasma, EDM, or mechanical methods:
No Heat-Affected Zone (HAZ): The most significant advantage. Material properties remain unchanged near the cut edge – no hardening, warping, or micro-cracking. Critical for structural integrity and post-processing.
Exceptional Material Versatility: As outlined above, one machine handles an astonishingly diverse range
of materials and thicknesses.
High Precision and Accuracy: Modern CNC cut jet systems achieve tolerances of +/- 0.003″ to 0.005″ (0.075mm to 0.125mm) or better, with excellent edge quality and minimal taper (especially on thinner materials or with dynamic head compensation).
Minimal Material Waste (Nesting): The narrow kerf (as small as 0.02″ to 0.05″ / 0.5mm to 1.3mm) and ability to nest parts very closely together significantly optimize material usage and reduce costs.
Environmentally Friendly: The process uses water and natural abrasives (garnet). No toxic fumes, gases, or oils are produced. Water can often be recycled. Garnet can sometimes be recycled for certain applications.
Minimal Mechanical Stress: The cutting force exerted on the workpiece is very low, allowing delicate or thin parts to be cut without distortion or clamping damage.
Single-Pass Cutting: Complex shapes, sharp corners, and fine details are cut in a single operation without tool changes, reducing setup time.
Safety: No combustible gases (like plasma) or intense radiation (like laser) are involved. The primary hazard is the extremely high-pressure water itself, contained within the machine.
5. Diverse Industrial Applications of Cut Jet Cutting
The unique capabilities of cut jet technology make it indispensable across numerous sectors:
Aerospace & Defense: Precision cutting of titanium alloys, aluminum structures, composites (wings, fuselage panels), engine components, and specialized armor plating without compromising material integrity.
Automotive: Prototyping, gaskets, interior trim (fabric, foam, composites), fiberglass body panels, airbag textiles, and specialized filters.
Architecture & Construction: Intricate metal facades, structural steel components, complex stone and tile inlays for countertops and floors, decorative glass panels, and signage.
Manufacturing & Job Shops: General fabrication of parts from diverse materials, tooling, prototypes, machinery components, and custom one-off productions. Cut jet is the ultimate job shop tool.
Marine: Cutting hull components, composites for decks and superstructures, and interior fittings.
Electronics: Cutting circuit board laminates, insulating materials, and creating precise enclosures without thermal damage.
Art & Sculpture: Enabling artists to work with metals, stone, glass, and other materials to create intricate designs impossible with traditional tools.
Medical Device Manufacturing: Cutting biocompatible metals (titanium, stainless steel), plastics, and composites for implants, surgical tools, and equipment housings with sterile water options.
6. Choosing the Right Cut Jet System: Factors to Consider
Selecting a cut jet system involves careful evaluation of several factors:
Pump Type & Pressure:
Intensifier Pumps: Most common. Use hydraulic oil to drive a piston that pressurizes water. Offer high pressure (60k-90k+ psi), reliability, and scalability. Require water deionization.
Direct-Drive Pumps: Use an electric motor directly coupled to crankshaft-driven plungers. Typically lower pressure (40k-60k psi), simpler design, lower initial cost, but potentially higher long-term maintenance and lower maximum cutting capability/thickness. Often don’t require deionized water.
Table Size & Configuration: Dictates the maximum workpiece size. Consider gantry style (moving bridge) vs. cantilever designs. Cutting bed type (water tank vs. slat bed) is crucial for material support and waste removal.
Cutting Head Technology: Look for features like automatic height control (AHC) to maintain optimal standoff distance over uneven surfaces, dynamic waterjet compensation (taper control), and quick-change nozzle assemblies. 5-axis cut jet heads enable complex beveling and 3D cutting.
CNC Control & Software: User-friendly interface, powerful nesting capabilities, CAD/CAM integration, simulation tools, and robust path planning are essential for productivity and precision. Look for features optimized for waterjet dynamics.
Abrasive Delivery System: Efficient, consistent, and controllable abrasive metering is critical for cut quality and operating cost management.
Intended Applications: Match the machine’s capabilities (pressure, horsepower, table size, head features) to the primary materials, thicknesses, and part complexities you need to cut.
Operating Costs: Factor in costs of abrasives (garnet), pump consumables (seals, valves, orifices, mixing tubes), electricity, water treatment (for intensifiers), and maintenance.
7. The Future of Cut Jet Technology
Cut jet technology continues to evolve rapidly. Key trends shaping its future include:
Higher Pressures & Pump Efficiency: Development of pumps reliably operating at 100,000 psi and beyond for faster cutting speeds on thick materials and improved edge quality. Focus on energy efficiency is paramount.
Enhanced Precision & Speed: Improved motion control systems, predictive kerf compensation algorithms, and more sophisticated nozzle designs aim for laser-like precision at competitive speeds, even on thicker materials.
Advanced Abrasive Technologies: Research into alternative, more efficient, or recyclable abrasives to reduce operating costs and environmental impact.
Smarter Software & Automation: Integration of AI for predictive maintenance, real-time process optimization, automated nesting, and seamless integration into Industry 4.0 smart factories. Increased use of robotics for loading/unloading.
Hybrid Manufacturing: Combining cut jet cutting with additive manufacturing (3D printing) or other subtractive processes (milling) in single machine platforms for complex part production.
Cut jet technology stands as a testament to the power of harnessing natural forces with precision engineering. Its unique ability to cut virtually any material without heat distortion, coupled with exceptional versatility, precision, and environmental benefits, ensures its continued dominance in modern fabrication. From the intricate demands of aerospace to the robust needs of construction and the creative expressions of art, the cut jet stream provides a solution that thermal processes simply cannot match. As pump pressures increase, controls become smarter, and operating costs are further optimized, the reach and impact of cut jet cutting will only continue to expand, solidifying its role as an essential tool for innovation and manufacturing excellence across the globe. Understanding its principles, capabilities, and selection criteria empowers businesses to leverage this remarkable technology effectively.
continue reading
Related Posts
- 1917 words9.7 min read