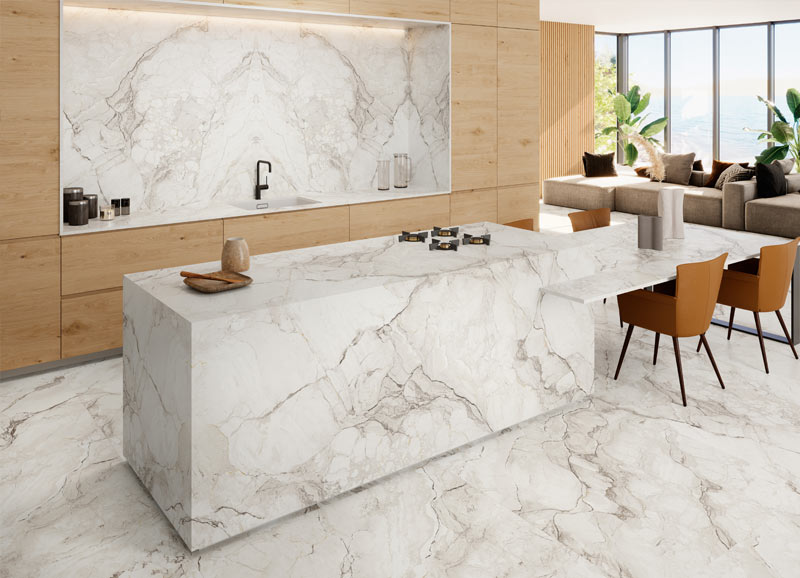
Water Jet Cutting Glass: The Ultimate Guide to Precision, Versatility & Cool Cutting
Glass, with its inherent beauty and fragility, presents unique challenges for fabrication. Traditional cutting methods often involve scoring, snapping, thermal stress, or abrasive grinding – processes prone to chipping, cracking, micro-fractures, and limitations in complex shapes. Enter water jet cutting glass, a revolutionary technology that has transformed how designers, architects, and manufacturers work with this versatile material. This comprehensive guide explores the seven key aspects that make water jet cutting glass the preferred method for precision fabrication.
1. The Fundamental Principle: Harnessing the Power of Water and Abrasive
At its core, water jet cutting glass is an erosion process. Here’s how it achieves such remarkable results:
Ultra-High Pressure: A high-pressure intensifier pump pressurizes ordinary water to extreme levels, typically between 60,000 and 90,000 PSI (4,000 to 6,200 bar).
Focusing the Stream: This pressurized water is forced through a tiny gemstone orifice (often diamond or sapphire), creating a supersonic stream thinner than a human hair.
Introducing the Cutting Edge (Abrasive Jet): For cutting hard materials like glass, an abrasive material (typically garnet sand) is precisely metered into this high-velocity water stream within a mixing chamber. The abrasive particles are accelerated by the water, transforming the stream into an incredibly powerful cutting tool.
Micro-Erosion: This high-velocity mixture of water and abrasive strikes the glass surface with immense kinetic energy. It literally erodes the material at a microscopic level along a precisely controlled path dictated by a CNC (Computer Numerical Control) system. The water then flushes away the eroded particles and cools the cut.
This process makes water jet cutting glass fundamentally different from thermal methods (like lasers) or mechanical scoring/snapping, eliminating heat-related stresses and providing unmatched flexibility.
2. Unmatched Precision and Complex Geometry Capabilities
Water jet cutting glass excels where other methods falter: intricate shapes and tight tolerances.
CNC Precision: Guided by advanced CAD/CAM software, the waterjet nozzle follows complex paths with exceptional accuracy. Tolerances of +/- 0.005 inches (0.13 mm) or better are routinely achievable, crucial for parts requiring perfect fitment.
Intricate Details: Sharp inside corners, complex curves, detailed cutouts, and delicate features are easily produced. Think intricate decorative panels, precise holes for hardware near edges, or complex architectural elements.
No Tooling Changes: Unlike die cutting or milling, water jet cutting glass requires no custom tooling for different shapes. Simply change the digital file, and the machine cuts a new design instantly, making it ideal for prototyping, custom one-offs, and short runs.
Near-Net Shape Cutting: The ability to cut very close to the final shape minimizes secondary finishing operations, saving time and material.
This precision makes water jet cutting glass indispensable for applications ranging from high-tech electronics and medical devices to bespoke art installations and luxury furniture.
3. Material Versatility: Beyond Just Glass
While our focus is water jet cutting glass, a key advantage of the technology is its incredible versatility on the same machine:
Glass Types: It handles virtually all types: annealed float glass, tempered glass (cut before tempering), laminated glass (cutting layers simultaneously or individually), stained glass, fused glass, borosilicate (Pyrex), frosted glass, and even thick glass blocks. Different thicknesses require adjustments in speed and pressure, but the core process remains effective.
Composites: Easily cuts materials like stone, tile (porcelain, ceramic), metals (steel, aluminum, brass, titanium), plastics (acrylic, polycarbonate), foam, rubber, and laminates.
Multi-Material Projects: A single waterjet machine can cut all the components for a complex project involving glass, metal brackets, stone bases, and plastic spacers, ensuring perfect fit and consistency.
This versatility makes water jet cutting glass shops highly valuable partners for projects involving diverse materials.
4. Superior Edge Quality: Minimizing Post-Processing
The edge quality achieved with water jet cutting glass is a major differentiator:
Smooth, Frosted Finish: The abrasive action creates a uniformly satin or frosted matte finish directly from the cut. This is often aesthetically desirable, especially in architectural or decorative applications, eliminating the need for costly edge polishing in many cases.
Minimal Chipping & Micro-Fractures: Unlike scoring and snapping, water jet cutting glass produces virtually no chipping along the cut edge. The erosion process also minimizes the creation of micro-fractures that can weaken the glass or become starting points for future cracks.
Consistency: The CNC-controlled process ensures edge quality is consistent across the entire cut and from part to part.
Reduced Secondary Finishing: For applications requiring a polished edge, the waterjet cut provides an excellent starting point, significantly reducing the time and labor needed for subsequent polishing compared to edges from rougher cutting methods.
The high-quality edge directly off the machine translates to cost savings and faster project completion.
5. The Critical Advantage: Cool Cutting (No Heat-Affected Zone – HAZ)
This is arguably the most significant benefit of water jet cutting glass, especially compared to laser cutting or plasma:
Thermally Neutral Process: The cutting medium is cold water mixed with abrasive. The process generates negligible heat at the cutting point.
Eliminates Thermal Stress: Glass is highly sensitive to thermal shock and stress. Heat-based cutting methods (like lasers) create a Heat-Affected Zone (HAZ) along the cut. This localized heating and rapid cooling can cause:
Micro-cracking and weakening of the glass structure.
Optical distortions (waviness) near the cut edge.
Residual stresses that can lead to spontaneous breakage later, especially if the glass is to be tempered.
Problems cutting pre-tempered glass (it would shatter).
Preserves Material Integrity: Water jet cutting glass leaves the material in its original state – chemically, structurally, and optically. No annealing is required after cutting. This is vital for the structural integrity of the glass component and its subsequent processing (like tempering).
The cool-cutting nature makes water jet cutting glass the only viable method for many critical applications, particularly when cutting laminated glass layers simultaneously without damaging the interlayer or when preparing glass for tempering.
6. Design Freedom and Flexibility
Water jet cutting glass liberates designers from the constraints of traditional glass fabrication:
Rapid Prototyping: Digital files mean designs can be iterated and cut quickly and cost-effectively for testing and refinement.
Mass Customization: Easily produce unique, one-off pieces or small batches without the high setup costs associated with molds or dies. Every piece can be different.
Complex Integration: Seamlessly integrate cutouts for handles, vents, mounting points, lighting, or electronic components directly into the glass design. Create intricate patterns and textures impossible with other methods.
Scalability: While perfect for customization, water jet cutting glass is also efficient for larger production runs due to its automation and minimal setup time between jobs.
Late-Stage Changes: Design modifications can often be accommodated right up to cutting with minimal disruption, simply by updating the CAD file.
This flexibility fuels innovation in architecture, interior design, art, signage, and industrial applications.
7. Environmental and Safety Considerations
Water jet cutting glass offers advantages beyond just the cut:
Reduced Waste: The narrow kerf (cutting width, typically 0.03″ to 0.05″ / 0.76mm to 1.27mm) and nesting capabilities of CAD software minimize material waste compared to some traditional methods.
No Hazardous Fumes: Unlike some thermal cutting processes, water jet cutting glass produces no toxic fumes, smoke, or dust (the abrasive is contained within the water stream and collected in a tank). This creates a safer working environment.
Coolant Function: The water acts as a natural coolant and dust suppressant.
Recyclability: The primary waste stream is the spent abrasive (garnet) and glass particles suspended in water. Garnet is inert and can often be recycled or disposed of safely. Water is filtered and can be recycled within the system.
Water jet cutting glass is more than just a cutting method; it’s an enabling technology that unlocks the full potential of glass as a design and engineering material. Its unique combination of cold-cutting action, exceptional precision, ability to handle intricate geometries, superior edge quality, remarkable material versatility, and inherent design flexibility makes it the go-to solution for architects, artists, designers, and manufacturers worldwide.
Whether creating breathtaking architectural facades, delicate electronic components, robust industrial parts, or unique decorative pieces, water jet cutting glass delivers results that are simply unattainable with traditional methods. By eliminating heat stress, minimizing chipping, enabling complex designs, and offering a cleaner, safer process, it represents the cutting edge of glass fabrication technology. When precision, quality, versatility, and material integrity matter, water jet cutting glass is the clear choice.
continue reading
Related Posts
- 2163 words10.9 min read
- 1640 words8.3 min read