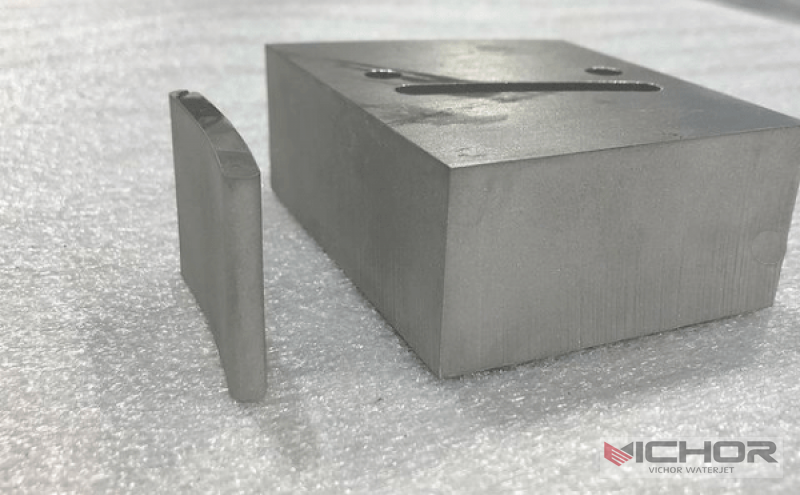
Intensifier Pump: The Ultimate Guide to High-Pressure Powerhouses
In the demanding world of industrial processes and advanced manufacturing, generating immense hydraulic pressure is often a critical requirement. Enter the intensifier pump, a specialized and robust piece of engineering designed to transform relatively low input pressure into exceptionally high output pressure. These hydraulic workhorses are indispensable in applications where standard pumps fall short. This comprehensive guide delves deep into the world of intensifier pump technology, exploring its principles, components, applications, advantages, and selection criteria.
1. The Core Principle: How Does an Intensifier Pump Work?
At its heart, an intensifier pump operates on a beautifully simple yet highly effective principle: Pascal’s Law. This fundamental law of hydraulics states that pressure applied to a confined fluid is transmitted undiminished in all directions. The intensifier pump leverages this by utilizing pistons of significantly different surface areas.
The Input Stage: Low-pressure fluid (often hydraulic oil at pressures ranging from 1000 to 5000 psi, supplied by a standard hydraulic power unit) is directed to a large-diameter piston, often called the “drive piston.”
Force Multiplication: The force generated by this low-pressure fluid acting on the large drive piston area (F_low = P_low * A_large) is substantial.
The Output Stage: This force is mechanically transmitted (usually via a connecting rod) to a much smaller-diameter plunger (the “intensifier plunger”) acting on the high-pressure output fluid (typically water, oil, or an emulsion).
Pressure Amplification: Because the force (F_low) remains constant but is applied to a significantly smaller area (A_small) on the output side, the output pressure (P_high) is dramatically increased. The pressure ratio is determined by the inverse ratio of the piston/plunger areas: P_high = P_low * (A_large / A_small).
Reciprocating Action: Most intensifier pumps are reciprocating. Hydraulic valves alternately direct fluid to one side of the drive piston, pushing it and the connected intensifier plunger forward to discharge high-pressure fluid, then to the other side to retract it, often while refilling the output chamber. This creates a pulsating flow, though modern systems often incorporate multiple intensifiers and sophisticated dampeners to smooth the output.
This elegant force-multiplication principle is what gives the intensifier pump its unique capability to generate pressures far exceeding those possible with standard positive displacement or centrifugal pumps, routinely reaching 40,000 psi, 60,000 psi, and even exceeding 100,000 psi in specialized units.
2. Key Components: Anatomy of a High-Pressure Generator
Understanding the critical components within an intensifier pump assembly reveals why it’s built for extreme duty:
Drive Cylinder: Houses the large-diameter drive piston. Constructed from high-strength steel, it handles the input hydraulic pressure and guides the piston’s movement. High-quality seals prevent internal leakage between the drive and intensifier sides.
Drive Piston: The large piston acted upon by the low-pressure hydraulic fluid. Its large surface area is key to generating the initial force. Durable seals ensure efficient power transfer.
Intensifier Plunger: A hardened, high-precision rod (often ceramic-coated or made from ultra-hard alloys like tungsten carbide) with a much smaller diameter than the drive piston. This plunger directly pressurizes the process fluid. Its surface finish and concentricity are critical for seal life.
High-Pressure Cylinder/Chamber: The chamber where the intensifier plunger acts on the output fluid. This component is subject to extreme cyclic stresses and must be manufactured from specially forged and treated high-strength alloys. Fatigue resistance is paramount.
Check Valves: Crucial one-way valves control the flow of the low-pressure input fluid into the drive cylinder and the high-pressure output fluid out of the intensifier chamber. They must seat perfectly to prevent backflow and pressure loss at extreme pressures.
Directional Control Valves: Sophisticated hydraulic valves (often pilot-operated spool valves) precisely control the flow of low-pressure fluid to alternately extend and retract the drive piston/intensifier plunger assembly.
High-Pressure Seals: Perhaps the most critical components. These seals (often advanced polymer or composite designs like PTFE blends with reinforcing elements) must contain the immense output pressure around the reciprocating intensifier plunger while minimizing friction and wear. Seal design and material selection are constantly evolving.
Pulsation Dampeners: Essential for smoothing the inherent pressure pulses generated by the reciprocating action. Accumulators or specialized dampening chambers absorb energy during the discharge stroke and release it during the refill/retraction stroke, providing a more stable output flow.
Filtration System: Ultra-fine filtration (often down to 1 micron or less) is mandatory both on the low-pressure hydraulic input and the process fluid intake. Contaminants are the primary enemy of high-pressure seals and precision surfaces.
3. Where Power Meets Precision: Key Applications of Intensifier Pumps
The unique ability of the intensifier pump to generate ultra-high pressures makes it the technology of choice in numerous critical industries:
Waterjet Cutting: The dominant application. Intensifier pump systems pressurize water (or water mixed with abrasive garnet) to 40,000 – 100,000 psi, creating a supersonic stream capable of precisely cutting virtually any material (metal, stone, glass, composites, food) with minimal heat-affected zones and exceptional edge quality. The reliability and pressure capability of the intensifier pump directly determine cutting speed and thickness capacity.
Hydrostatic Testing: Verifying the integrity of pressure vessels, pipelines, valves, and other critical components requires subjecting them to pressures significantly exceeding their operating limits. Intensifier pump systems provide the controlled, high-pressure fluid (usually water or oil) needed for safe and reliable testing.
Descaling: In steel mills, high-pressure water jets generated by intensifier pump systems (typically 2000-4500 bar) are used to remove scale (iron oxide) from billets, slabs, and blooms before further processing like rolling.
High-Pressure Cleaning (HPC): For industrial cleaning tasks requiring extreme force to remove tenacious deposits, coatings, or contaminants from surfaces (e.g., ship hulls, heat exchangers, concrete), intensifier pump-powered systems offer unparalleled cleaning power compared to standard pressure washers.
Metal Forming (Hydroforming): Using high-pressure fluid (usually oil or water-oil emulsion) inside a sealed die cavity, intensifier pump systems force sheet metal or tubing to conform precisely to the shape of the die, creating complex, lightweight, and strong parts for automotive, aerospace, and appliance industries.
Reverse Osmosis (RO) Seawater Desalination: High-pressure intensifier pump systems (operating around 800-1200 bar) are increasingly used to push seawater through semi-permeable RO membranes, overcoming the natural osmotic pressure to produce fresh water efficiently. Their energy efficiency is crucial here.
Food Processing (High-Pressure Processing – HPP): Non-thermal pasteurization using ultra-high pressure (up to 87,000 psi / 6000 bar) generated by intensifier pump systems inactivates pathogens and extends shelf life while preserving taste, texture, and nutrients in products like juices, meats, and guacamole.
Laboratory & Research: Generating controlled ultra-high pressures for material science research, chemical synthesis, or physics experiments often relies on specialized intensifier pump systems.
4. Advantages and Limitations: Why Choose (or Reconsider) an Intensifier Pump?
Understanding the strengths and weaknesses of intensifier pump technology is vital for selecting the right solution:
Advantages:
Extremely High Pressure: Unmatched capability to generate pressures far beyond other pump types (40k psi to 100k+ psi).
Scalable Power: Output pressure is largely independent of flow rate, allowing pressure to be maintained even at low flows. Flow rate is increased by adding more intensifier units (“blocks”) to the pump.
Robustness & Durability: Designed for continuous operation in harsh industrial environments with proper maintenance.
Efficiency: While overall efficiency depends on the entire system (including the hydraulic power unit), the intensification process itself is mechanically efficient due to the direct force transfer.
Clean Operation (Waterjet): When using water, it offers a cold-cutting process without heat, fumes, or mechanical stresses associated with traditional cutting.
Precision Control: Modern systems offer sophisticated electronic control over pressure and flow.
Limitations/Considerations:
Pulsating Flow: Inherent to the reciprocating action, requiring dampeners which add complexity and cost. Smooth flow comes at a premium.
Higher Initial Cost: Significantly more expensive than standard pressure washers or lower-pressure pumps due to the high-precision components and robust construction.
Maintenance Intensity: Seals, valves, and plungers are wear items operating under extreme conditions, requiring regular inspection, maintenance, and replacement. Downtime for maintenance must be factored in.
Noise and Vibration: The reciprocating mechanism and high-pressure fluid flow can generate significant noise and vibration, necessitating sound enclosures and proper mounting.
Filtration Demands: Extremely sensitive to fluid contamination, requiring meticulous filtration systems on both hydraulic and process fluid sides.
System Complexity: Requires a supporting hydraulic power unit, sophisticated controls, and filtration, making the overall system footprint larger than simpler pump types.
5. Selecting the Right Intensifier Pump: Key Considerations
Choosing the optimal intensifier pump requires careful analysis of your specific application needs:
Required Pressure (PSI/Bar): This is the primary driver. Select a pump rated comfortably above your maximum operating pressure.
Required Flow Rate (GPM/LPM): Determines the cutting speed (waterjet), cleaning rate (HPC), or cycle time (hydroforming). Flow is typically increased by adding more intensifier cylinders (“boosts”).
Process Fluid: Water, oil, oil/water emulsion, or chemicals? Material compatibility for seals, plungers, valves, and the high-pressure cylinder is critical.
Duty Cycle: Will it run continuously 24/7, or intermittently? This impacts cooling requirements, component selection, and expected maintenance intervals.
Control Requirements: Do you need simple on/off control, or precise electronic pressure/flow modulation with programmable profiles? This dictates the sophistication of the pump controller and valves.
Pulsation Tolerance: How critical is a smooth flow? Applications like precise waterjet cutting or HPP demand sophisticated dampening, increasing cost.
Reliability & Maintenance: Consider Mean Time Between Failures (MTBF) for critical components, ease of access for maintenance, availability of spare parts, and manufacturer support. Operating costs heavily depend on seal and plunger life.
Energy Efficiency: Compare the overall system efficiency (hydraulic power unit + intensifier pump), especially for high-duty-cycle applications like desalination. Variable frequency drives (VFDs) on the hydraulic power unit can offer significant savings.
Footprint and Noise: Ensure the pump and its required support systems (HPU, chillers, filters) fit the available space. Consider noise mitigation requirements.
Total Cost of Ownership (TCO): Look beyond the initial purchase price. Factor in energy consumption, maintenance costs (seals, valves, filters, labor), expected component lifetimes, and potential downtime costs.
The Future of Intensifier Technology
Intensifier pump technology continues to evolve. Research focuses on enhancing durability through advanced materials (ceramics, nano-coatings) for plungers and seals, improving energy efficiency via smarter controls and hydraulic designs, reducing pulsation through innovative dampening and multi-cylinder configurations, and developing more compact and quieter systems. The demand for higher pressures, greater reliability, and lower operating costs ensures that the intensifier pump will remain a cornerstone technology for ultra-high-pressure applications for the foreseeable future.
The intensifier pump stands as a remarkable feat of engineering, transforming modest hydraulic force into the immense pressures required for cutting-edge industrial processes. From sculpting intricate metal parts with waterjet precision to ensuring the safety of pressure vessels and pasteurizing food without heat, its impact is widespread. Understanding its working principle, key components, diverse applications, and inherent advantages and limitations is crucial for engineers, technicians, and decision-makers relying on ultra-high-pressure technology. By carefully considering the selection criteria, businesses can harness the formidable power of the intensifier pump to enhance efficiency, quality, and innovation within their operations. As material science and control systems advance, these high-pressure powerhouses will continue to push the boundaries of what’s possible.
continue reading
Related Posts
- 2163 words10.9 min read