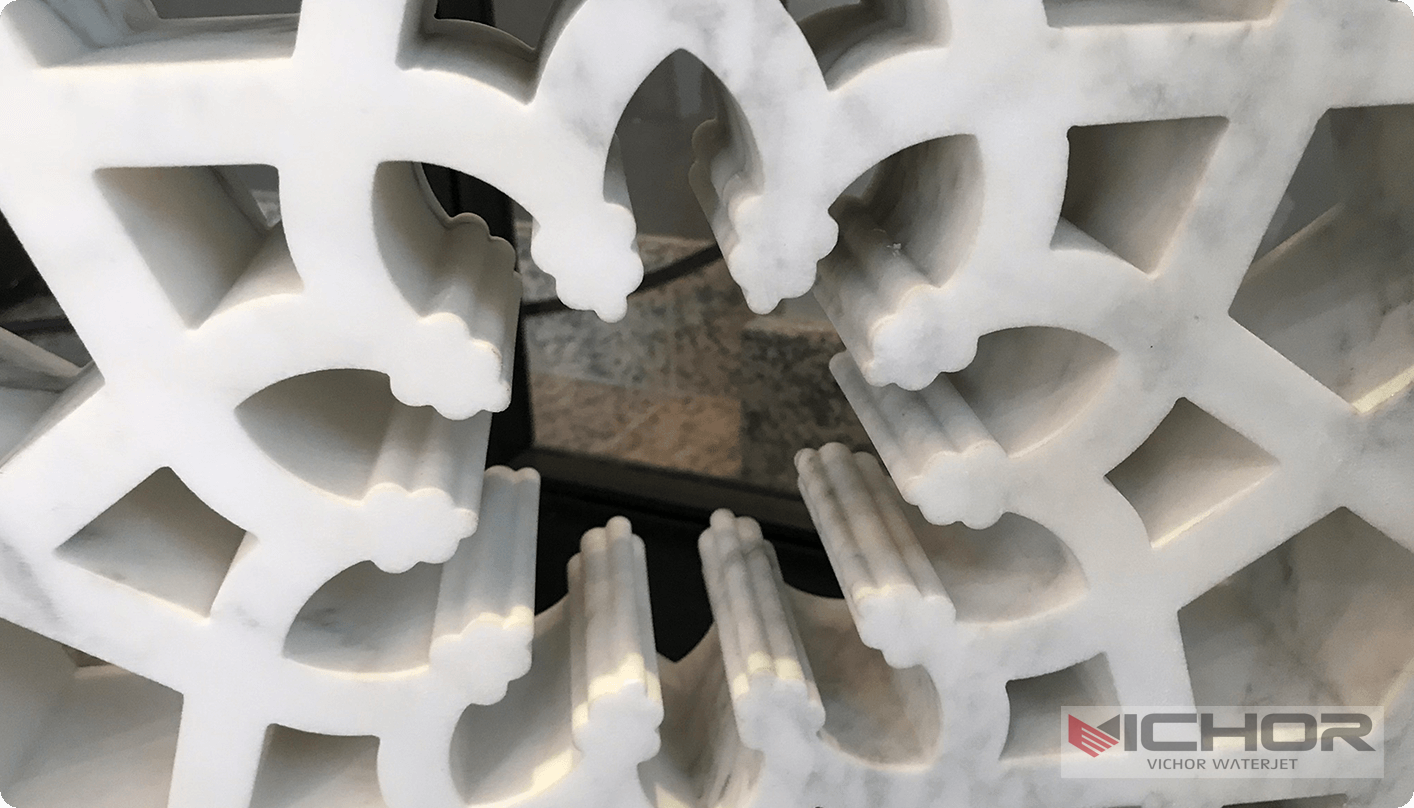
Water Iron Cutter Unlocked: The Ultimate Guide to Abrasive Waterjet Metal Cutting Technology
In the demanding world of metal fabrication and precision machining, finding a technology that combines raw power with delicate precision is the holy grail. Enter the water iron cutter, more accurately known as an abrasive waterjet cutter. This remarkable technology harnesses the focused energy of ultra-high-pressure water mixed with abrasive garnet to slice through virtually any material, including hardened steel, titanium, and iron alloys, with astonishing accuracy and minimal thermal impact. This comprehensive guide dives deep into the science, advantages, applications, and future of the water iron cutter, explaining why it has become an indispensable tool across countless industries.
What is a Water Iron Cutter? Demystifying the Technology
At its core, a water iron cutter is an abrasive waterjet cutting system specifically configured and optimized for cutting ferrous and non-ferrous metals. It leverages a fundamental principle: channeling immense kinetic energy into a tiny, focused stream. Here’s the basic process:
Ultra-High Pressure Generation: An intensifier pump takes standard municipal water pressure (typically 60-100 PSI) and multiplies it exponentially, generating pressures ranging from 60,000 PSI (4,100 bar) up to an incredible 90,000 PSI (6,200 bar) or more.
Waterjet Formation: This ultra-high-pressure water is forced through a tiny diamond or sapphire orifice (typically 0.010″ to 0.015″ / 0.25mm to 0.38mm in diameter), creating a supersonic “pure” waterjet stream.
Abrasive Introduction (The Key to Cutting Iron): For cutting hard materials like iron and steel, pure water isn’t enough. The pure waterjet enters a specialized mixing chamber (focusing tube or nozzle). Here, precisely metered abrasive garnet sand (usually 80 Mesh or similar) is drawn into the chamber via a venturi effect created by the high-speed waterjet.
Abrasive Acceleration & Cutting: The water stream violently accelerates the abrasive particles. This mixture of water and abrasive then exits through a longer, slightly wider carbide or ceramic focusing tube (typically 0.030″ to 0.050″ / 0.76mm to 1.27mm diameter). The resulting abrasive waterjet stream is a concentrated beam of erosive energy capable of slicing through thick metal plates.
CNC Precision: The cutting head is mounted on a sophisticated Computer Numerical Control (CNC) gantry system. This allows for precise, programmable movement in the X, Y, and often Z axes, enabling the cutting of complex 2D and 3D shapes directly from CAD/CAM files.
How Does a Water Iron Cutter Actually Cut Through Metal? The Mechanics of Erosion
Unlike thermal processes (laser, plasma, oxy-fuel) that melt material, the water iron cutter works purely through mechanical erosion. This “cold cutting” process is key to its unique advantages:
Kinetic Energy Transfer: The ultra-high velocity of the water stream (approaching Mach 3) transfers immense kinetic energy to the abrasive garnet particles.
Micro-Machining Impact: These accelerated abrasive particles act like microscopic hammers, striking the metal surface at incredibly high speeds.
Material Removal: Each impact creates a tiny fracture and removes a minuscule particle of material. The sheer number of impacts per second (billions) results in a continuous, controlled erosion process along the cutting path.
The Role of Water: While the abrasives do the primary cutting, the water serves critical functions:
Accelerating the abrasives.
Removing the eroded debris (swarf) from the kerf (the cut path).
Cooling the cut zone.
Providing cohesion to the jet stream.
This erosion mechanism allows the water iron cutter to slice through hardened tool steel, armor plate, titanium, and other notoriously difficult metals without altering their intrinsic properties.
The Unmatched Advantages of Using a Water Iron Cutter
The unique cold-cutting, mechanical erosion process of the water iron cutter delivers a suite of compelling benefits over traditional and other advanced metal cutting methods:
Zero Heat-Affected Zone (HAZ): This is arguably the most significant advantage. Since no heat is generated in the cutting process, there is:
No hardening or annealing: The metallurgical structure near the cut edge remains completely unchanged.
No thermal distortion: Parts retain their original flatness and dimensional stability. No warping or stress-induced bending.
No micro-cracking: Critical for materials prone to heat-induced cracking like high-strength alloys or tempered steels.
Material Versatility: A single water iron cutter can effortlessly switch between cutting:
Ferrous Metals: Mild steel, stainless steel (all grades), tool steel, cast iron, armor plate.
Non-Ferrous Metals: Aluminum, copper, brass, bronze, titanium, inconel, tungsten.
Composites: Carbon fiber, fiberglass, Kevlar (without delamination).
Plastics: Acrylic, PVC, polycarbonate, rubber (without melting).
Stone, Tile, Glass, Ceramics.
Laminates and Sensitive Materials: Electronics, food products, explosives.
Exceptional Precision and Edge Quality:
Tight Tolerances: Capable of holding tolerances of ±0.003″ to ±0.005″ (±0.076mm to ±0.127mm) or better, depending on machine calibration and material.
Smooth Edges: Produces a satin-smooth finish, often requiring minimal secondary finishing. Edge taper can be controlled and minimized.
Intricate Details: Can cut very complex shapes, sharp corners, and small features that are impossible or extremely difficult for plasma or flame cutting.
No Mechanical Stresses: The cutting force exerted by the waterjet is very low (typically a few pounds) compared to mechanical methods like milling or punching. This eliminates the risk of inducing stress or deformation in thin or delicate parts.
Environmentally Friendly:
No Hazardous Fumes: Unlike plasma or laser cutting metals, no toxic fumes, smoke, or molten spatter are produced. Only water and garnet (an inert mineral) are used.
Reduced Waste: Kerf width is narrow (typically 0.030″ to 0.050″ / 0.76mm to 1.27mm), minimizing material waste. Nesting software optimizes material usage.
Garnet Recycling: Spent garnet, while inert, can often be recycled for other uses like sandblasting or construction fill, reducing landfill burden. Water filtration systems are common.
Minimal Setup & Fixturing: Often requires only simple clamping due to the low cutting force.
Beyond Iron: The Astonishing Material Range of Waterjet Cutting
While excelling as a water iron cutter, the technology’s true power lies in its unparalleled versatility. One machine becomes the universal cutting solution:
Metals: As discussed, all metals are fair game – from thin foils to thick armor plate (12 inches/300mm+ in steel is possible).
Composites: The cold cut prevents delamination, melting, or fraying of layers in carbon fiber, fiberglass, honeycomb structures, and Kevlar. Essential for aerospace and automotive.
Stone and Tile: Used extensively for intricate countertops, mosaics, signage, and architectural elements. No chipping or thermal shock.
Glass: Cutting laminated safety glass, artistic patterns, or thick glass blocks without cracking or thermal stress.
Plastics and Rubber: Cuts without melting edges or releasing harmful fumes. Ideal for gaskets, seals, displays, and packaging.
Food: Used for portioning frozen foods, cakes, pastries, and even processed meats hygienically and precisely.
Foams and Insulation: Cleanly cuts complex shapes without compressing the material.
Exotics: Handles materials like titanium, inconel, hastelloy, tungsten carbide, and ceramics that are extremely difficult or impossible to cut economically with other methods.
This eliminates the need for multiple dedicated cutting machines for different materials in many job shops.
Precision Engineering: Accuracy, Taper Control, and Edge Quality in Waterjet Cutting
Modern water iron cutter systems are marvels of precision engineering, achieving results rivaling many machining processes:
Positional Accuracy: High-precision linear guides, ballscrews, and advanced motion control software enable positioning accuracy and repeatability within thousandths of an inch (hundredths of a millimeter).
Kerf and Taper Management:
Kerf Width: Typically ranges from 0.030″ to 0.050″ (0.76mm to 1.27mm), depending on orifice size, focusing tube size, pressure, and abrasive flow rate.
Taper Compensation: As the jet loses energy penetrating thicker material, a natural taper occurs (wider at the top than the bottom). Advanced dynamic cutting head control (tilting the head or using specialized nozzles) and CAM software algorithms automatically compensate during cutting to produce near-vertical edges even in thick plates.
Surface Finish (Ra): The edge quality (surface roughness) is primarily determined by the abrasive size and feed rate. Using finer garnet (e.g., 120 Mesh) and cutting slower produces a smoother finish (lower Ra value). Typical Ra values range from 125 to 250 microinches (3.2 to 6.3 micrometers) for metals, significantly smoother than plasma cutting. The finish is often described as a “satin” texture.
Dynamic Waterjet Control: Sophisticated systems adjust pressure, abrasive flow, and cutting head speed in real-time during acceleration, deceleration, cornering, and piercing to optimize cut quality, minimize taper, and reduce cycle times across the entire part geometry.
Piercing: Specialized piercing routines minimize splashback and damage to the material surface when starting an internal cut.
Industrial Applications: Where the Water Iron Cutter Shines
The unique capabilities of the water iron cutter make it indispensable across a vast spectrum of industries:
Aerospace: Cutting titanium engine components, aluminum structural parts, intricate brackets, heat-resistant alloys (Inconel), and composite panels (carbon fiber, fiberglass) without altering material properties or causing delamination.
Automotive: Prototyping, gaskets, interior trim, suspension components, body panels (aluminum, high-strength steel), composite parts, insulation, and specialized tooling.
Architecture & Construction: Decorative metal panels, structural steel components (beams, brackets), intricate stone and tile work, composite cladding, signage, and artistic installations.
Manufacturing & Job Shops: General metal fabrication, prototyping, low-volume/high-mix production, cutting tool blanks, machine components, and custom parts from virtually any material.
Defense & Military: Cutting armor plate (ballistic steel), titanium components for vehicles and aircraft, specialized composites, and explosive ordnance disposal (EOD – cold cutting prevents detonation).
Medical Device Manufacturing: Cutting intricate components from stainless steel, titanium, and specialized alloys for implants, surgical instruments, and diagnostic equipment with no heat-induced stress or contamination. Cutting biocompatible plastics.
Energy (Oil & Gas, Nuclear): Cutting corrosion-resistant alloys (stainless steels, duplex), pipe components, flanges, valve bodies, and specialized tooling for harsh environments. Useful in nuclear decommissioning.
Electronics: Precisely cutting circuit boards (prototypes), enclosures, insulators, and laminates without thermal damage or debris contamination.
Art & Sculpture: Enabling artists to work with diverse materials like metal, stone, glass, and composites to create complex and delicate forms impossible with other tools.
Limitations and Considerations of Waterjet Cutting
While incredibly powerful, the water iron cutter has some inherent limitations to consider:
Cutting Speed vs. Thickness: While faster than wire EDM for thick materials, waterjet cutting is generally slower than plasma or laser cutting for thin sheet metal (especially mild steel under 1/2 inch / 12mm). Cutting speed decreases significantly as material thickness increases.
Operating Costs: Significant costs include:
Abrasive Garnet: The largest consumable cost, used continuously during cutting.
High-Pressure Pump Wear: Intensifier pumps require maintenance and replacement of seals and components.
Orifices & Focusing Tubes: These wear parts need regular replacement (diamonds last longer than sapphires; carbide tubes wear faster than ceramic).
Electricity: High-pressure pumps are energy-intensive.
Water Treatment: Filtration systems may be needed.
Material Thickness Limitations: While capable of cutting very thick materials (12+ inches in steel), cycle times become very long. Practical economic thickness often depends on the application and required precision.
Edge Taper: While controllable, taper is inherent to the process, especially in thick materials. Compensation adds complexity and cost.
Noise: The cutting process, especially the pump and the jet impacting the catcher tank, can be loud, requiring hearing protection and potentially sound enclosures.
Water Exposure: The workpiece gets wet during cutting. For some materials or applications, drying is required afterward. Rust-sensitive ferrous metals need prompt drying or protective measures.
The Future of Water Iron Cutting: Innovation on the Horizon
Waterjet technology continues to evolve rapidly:
Higher Pressures: Pumps capable of 100,000+ PSI (6,900+ bar) are emerging, promising faster cutting speeds, especially in thick materials, and potentially finer cuts.
Enhanced Precision & Dynamics: Improved motion control systems, faster acceleration, and more sophisticated dynamic cutting head control (5-axis, 6-axis) for complex 3D shaping and improved taper control.
Smarter Software: AI and machine learning for optimized cutting paths, predictive maintenance, automated parameter selection, and real-time quality monitoring.
Reduced Consumable Costs: Research into longer-lasting orifices and focusing tubes, and more efficient abrasive delivery/recycling systems.
Hybrid Systems: Integrating waterjet cutting heads with other technologies like milling or laser on a single platform for combined processing.
Automation Integration: Seamless integration with robotic arms and automated material handling systems for lights-out manufacturing.
The water iron cutter, or abrasive waterjet system, stands as a testament to the power of focused kinetic energy. Its ability to cold-cut virtually any material – from hardened steel to delicate composites, thick iron plates to intricate titanium components – with exceptional precision and without altering material properties makes it an unparalleled and indispensable tool in modern manufacturing and fabrication. While considerations around speed for thin metals and operating costs exist, the advantages of zero HAZ, unmatched versatility, high precision, excellent edge quality, and environmental friendliness consistently outweigh the limitations for a vast array of critical applications. As technology advances with higher pressures, smarter software, and enhanced automation, the capabilities and reach of the water iron cutter will only expand, solidifying its position as a cornerstone technology for innovation across countless industries. Whether you need to slice through armor plate or craft delicate medical components, the waterjet provides a uniquely powerful and flexible solution.
continue reading
Related Posts
- 1640 words8.3 min read