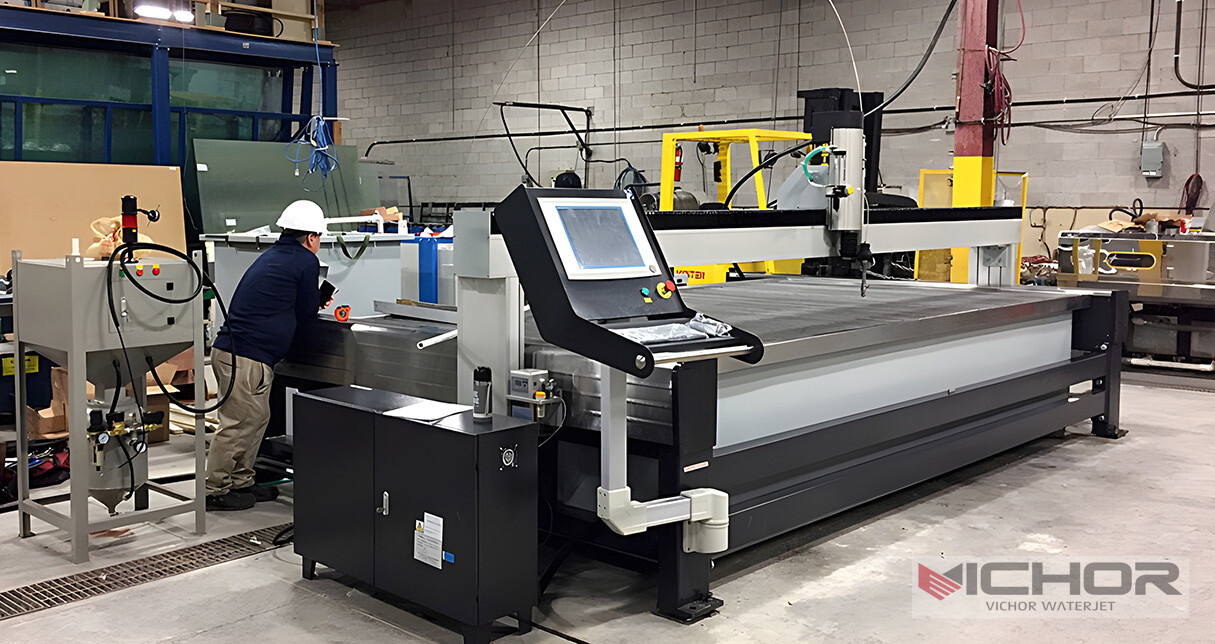
Superior Water Jet Technology: Revolutionizing Precision Cutting Across Industries
In the dynamic landscape of industrial fabrication and manufacturing, the quest for more efficient, versatile, and precise cutting methods is relentless. Standing out as a truly transformative technology is Superior Water Jet cutting. This advanced process harnesses the incredible power of high-pressure water, often augmented with abrasives, to slice through an astonishingly wide array of materials with unparalleled precision and minimal waste. Unlike thermal processes such as laser or plasma cutting, Superior Water Jet technology operates without generating heat-affected zones (HAZ), preserving material integrity and opening doors to applications impossible for other methods. This article delves deep into the multifaceted advantages that make Superior Water Jet systems the superior choice for countless modern manufacturing challenges.
1. Unmatched Material Versatility: Cutting Virtually Anything
The most profound strength of Superior Water Jet technology lies in its breathtaking material versatility. This is where it truly earns the “superior” designation. While thermal cutting methods are often limited by material reflectivity, conductivity, or melting point, a Superior Water Jet system cuts without discrimination.
Metals: From delicate foils and thin sheets of aluminum, copper, and brass to thick plates of hardened tool steel (up to 12 inches or more), titanium, Inconel, and armor plating. The cold-cutting process prevents hardening or warping.
Stone & Tile: Granite, marble, slate, limestone, porcelain, ceramic – intricate designs and precise shapes are effortlessly achieved without chipping or micro-fractures common with sawing.
Glass & Composites: Laminated glass, bulletproof glass, acrylics, fiberglass, carbon fiber composites – cut cleanly without delamination, melting, or toxic fumes.
Plastics & Rubber: From soft foams and rubber gaskets to dense UHMW-PE, nylon, and acrylics. No melting or hazardous gases are produced.
Exotics & Laminates: Materials like Kevlar, honeycomb structures, circuit boards, food products (using pure water jets), and multi-material laminates pose no challenge.
This unparalleled range eliminates the need for multiple dedicated cutting machines, streamlining production and offering immense flexibility to job shops and specialized manufacturers alike. A Superior Water Jet is truly a universal cutting tool.
2. Precision Beyond Compare: Achieving Intricate Details & Tight Tolerances
Superior Water Jet systems are synonymous with exceptional precision. Modern CNC-controlled machines achieve accuracies routinely within ±0.003 inches (±0.076 mm) and positional repeatability even tighter. This level of precision is crucial for:
Intricate Prototyping: Creating complex, detailed prototypes directly from CAD models without expensive tooling.
Fine Features: Cutting sharp inside corners, small holes (down to fractions of the jet diameter with piercing techniques), and intricate patterns impossible with mechanical methods.
Near-Net Shapes: Minimizing secondary machining operations by cutting very close to final dimensions.
Tight Tolerance Components: Manufacturing parts for aerospace, medical devices, and electronics where dimensional accuracy is paramount.
The kerf width (the width of material removed by the cut) of a Superior Water Jet is very narrow, typically ranging from 0.020″ to 0.050″ (0.5mm to 1.27mm) depending on the orifice size and abrasive flow, minimizing material waste even on complex contours. Advanced dynamic waterjet cutting heads can tilt the jet to compensate for taper, ensuring perpendicular walls even on thick materials – a hallmark of truly Superior Water Jet performance.
3. The Cold Cutting Advantage: Preserving Material Integrity
This is arguably the defining characteristic that elevates Superior Water Jet cutting above thermal processes. The cutting action is purely mechanical, generated by the erosive force of high-velocity water (and abrasive particles). This results in:
No Heat-Affected Zone (HAZ): The material’s microstructure, hardness, temper, and grain structure remain completely unchanged right up to the cut edge. There is no hardening, annealing, warping, or residual stress induced by heat.
No Thermal Distortion: Thin metals and heat-sensitive plastics cut without buckling, melting, or curling at the edges.
Safe Cutting of Explosives and Heat-Sensitive Materials: Applications where sparks or heat could cause ignition (like explosives or pyrotechnics) are uniquely suited for waterjet. Similarly, materials that degrade with heat (certain composites, plastics, tempered glass) are perfectly preserved.
Clean, Burr-Free Edges: While a slight textured finish is inherent, edges are typically free of the slag, dross, or heavy burrs associated with plasma or laser cutting, often requiring minimal or no secondary finishing. This inherent quality is a key benefit of a Superior Water Jet system.
This cold-cutting capability ensures the final part retains its original strength and properties, critical for structural components and high-performance applications.
4. Environmental Friendliness and Operational Safety
In an era of increasing environmental awareness and stringent workplace safety regulations, Superior Water Jet technology offers significant advantages:
Minimal Hazardous Byproducts: Unlike plasma or laser cutting, which can generate hazardous fumes, vapors, and molten spatter, waterjet cutting primarily produces a slurry of water, spent abrasive, and cut material particles. This slurry is non-toxic and can often be recycled or disposed of more easily (though responsible management is still essential). Pure waterjet cutting (no abrasive) is even cleaner, used for food and sensitive materials.
Reduced Dust: Compared to dry machining processes like sawing or routing, waterjet significantly suppresses airborne dust, improving air quality in the workshop and protecting operator health.
Lower Fire Risk: The absence of sparks, intense heat, or flammable gases drastically reduces the risk of fire, especially crucial when cutting combustible materials.
Quieter Operation: While high-pressure pumps generate noise, the cutting process itself is generally quieter than many mechanical cutting or grinding operations, contributing to a better working environment.
Water Recycling: Modern Superior Water Jet systems increasingly incorporate closed-loop water recycling systems, significantly reducing freshwater consumption and wastewater volume. This enhances sustainability credentials.
The inherent safety and reduced environmental impact make adopting Superior Water Jet technology a responsible choice for modern businesses.
5. Cost-Effectiveness and Operational Efficiency
While the initial investment in a Superior Water Jet system can be substantial, the total cost of ownership and operational efficiency often make it an economically superior choice in the long run:
Reduced Secondary Operations: The combination of high precision, excellent edge quality, and no HAZ frequently eliminates or drastically reduces the need for costly secondary machining, grinding, deburring, or heat treatment processes.
Minimal Material Waste: The narrow kerf and nesting capabilities of modern CAD/CAM software allow for highly efficient material utilization, especially valuable with expensive metals, stones, or composites. This inherent efficiency is a core feature of Superior Water Jet optimization.
Low Consumable Costs (Relatively): While abrasives (like garnet) and high-pressure components (orifices, mixing tubes) are consumables, their cost per part is often significantly lower than the energy costs or specialized gases required for laser or plasma, particularly on thicker materials.
Fast Setup & Programming: CNC programming for waterjet is generally straightforward, and setup involves primarily loading material and selecting the correct cutting head/nozzle. No specialized fixturing for heat dissipation is needed. Quick changeovers enhance flexibility for high-mix, low-volume production.
Unattended Operation: Modern Superior Water Jet systems are highly automated, capable of running lights-out operations for extended periods, maximizing machine uptime and productivity.
Versatility = Reduced Capital Expenditure: Replacing multiple dedicated machines (e.g., plasma for steel, router for composites, saw for stone) with a single Superior Water Jet system saves significant floor space and capital investment.
The efficiency gains and reduction in downstream processing costs often translate into a compelling ROI, particularly for businesses handling diverse materials and complex parts.
Superior Water Jet technology is far more than just another cutting tool; it represents a paradigm shift in manufacturing capabilities. Its defining characteristics – unparalleled material versatility, exceptional precision achieved cold, inherent environmental and safety benefits, and demonstrable long-term cost-effectiveness – solidify its position as a truly superior solution. From intricate aerospace components and pristine stone countertops to delicate food products and robust industrial machinery parts, Superior Water Jet systems deliver unmatched quality, flexibility, and efficiency. As the technology continues to evolve with advancements in pump design, control software, cutting head dynamics, and automation, its dominance in precision cold cutting across a vast spectrum of industries is set to grow even further. For manufacturers seeking a competitive edge through innovation, quality, and versatility, investing in Superior Water Jet technology is an investment in the future of fabrication.
continue reading