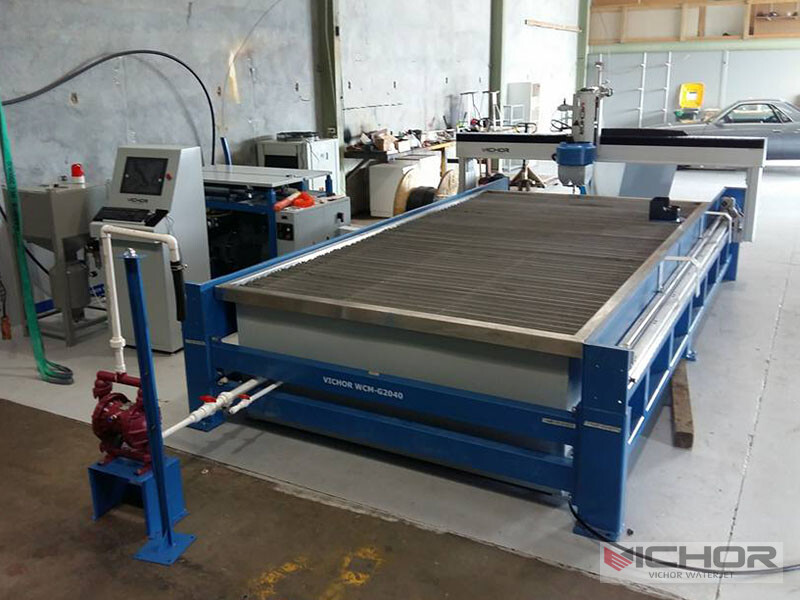
What Makes a High Quality Water Jet: 5 Key Aspects for Superior Performance
In the demanding world of precision cutting, the term “high quality water jet” is more than just a buzzword; it’s a critical differentiator between achieving exceptional results and facing costly compromises. Whether cutting intricate shapes in titanium, delicate patterns in stone, or thick plates of composite material, the quality of the water jet system directly impacts accuracy, edge finish, productivity, operating costs, and long-term reliability. But what truly defines a high quality water jet? Let’s delve into the five fundamental aspects that separate superior systems from the rest.
1. Unmatched Precision and Accuracy: The Hallmark of Excellence
At the core of a high quality water jet lies its ability to deliver exceptional precision and accuracy, consistently, over time and across diverse materials. This isn’t just about hitting a target dimension; it’s about achieving complex geometries with tight tolerances, minimal taper, and exceptional edge quality.
Advanced Motion Control: Superior systems utilize high-precision, rigid linear guides (often hardened steel or ceramic), high-torque servo motors, and sophisticated motion control software. This combination minimizes vibration, backlash, and positional error, ensuring the cutting head follows the programmed path with micron-level accuracy.
Dynamic Head Height Control (DHTC): A critical feature of any high quality water jet, DHHC continuously and automatically adjusts the cutting head’s height above the workpiece. This compensates for material warpage, uneven surfaces, and taper formation during piercing and cutting. Maintaining the optimal standoff distance (typically 0.010″ to 0.150″) is paramount for consistent kerf width, minimal taper, and maximizing abrasive effectiveness. Advanced systems use reliable non-contact sensors for real-time feedback.
Minimized Taper: All abrasive water jets exhibit some degree of taper (wider kerf at the top than the bottom). High-end systems significantly reduce this through precise nozzle alignment, optimized orifice and mixing tube quality, consistent pressure, and sophisticated cutting strategies (like tilting the head or adaptive pathing). This is crucial for parts requiring perpendicular edges or fitting into assemblies.
Superior Edge Quality: Beyond dimensional accuracy, a high quality water jet produces a remarkably smooth cut edge with a fine, satin-like finish. This reduces or often eliminates the need for secondary finishing operations, saving significant time and cost. Achieving this requires consistent pressure, optimal abrasive flow and mixing, and minimal vibration throughout the system.
2. Cutting Edge Technology: The Heart of the System
The core technology components – the intensifier pump, cutting head, and controls – are where the true engineering prowess of a high quality water jet shines.
High-Pressure Intensifier Pump: The pump is the engine. Top-tier systems feature robust, reliable intensifier pumps capable of generating and sustaining ultra-high water pressure (typically 60,000 PSI to 90,000+ PSI) with minimal fluctuation (<1%). Key elements include:
Durable Components: Hardened ceramic plungers, high-strength alloy blocks, and premium seals designed for longevity under extreme stress.
Efficient Design: Advanced designs minimize heat generation and energy consumption.
Reliability & Longevity: Built for continuous operation in industrial environments, minimizing downtime and maintenance costs. A high quality water jet pump will have a significantly longer mean time between failures (MTBF) than cheaper alternatives.
Precision Cutting Head: This is where water transforms into a cutting tool. Quality is paramount:
Orifice (Water Jet Nozzle): Made from ultra-hard materials like synthetic sapphire or diamond, a high quality water jet orifice maintains a perfectly round, consistent diameter (typically 0.010″ to 0.016″) for extended periods. Imperfect or worn orifices create unstable, flaring jets that ruin cut quality.
Mixing Tube (Focusing Tube): Typically made from super-hard tungsten carbide or composite diamond, this tube precisely mixes the high-pressure water stream with abrasive and focuses the cutting jet. Long-lasting tubes with consistent internal diameter and bore straightness are essential for achieving tight kerf widths and minimal taper. A high quality water jet system uses precisely matched orifices and mixing tubes.
Abrasive Delivery System: Consistent, controlled abrasive feed is critical. High-end systems use precision metering valves and vibratory feeders to ensure an optimal, uninterrupted flow of high-grade abrasive into the mixing chamber.
High-Grade Abrasive: The quality of the garnet abrasive directly impacts cut speed, edge quality, and mixing tube life. A high quality water jet operation demands consistent, angular, properly sized (typically 80 Mesh), and impurity-free garnet. Inferior abrasive leads to slower cutting, rougher edges, and accelerated wear on expensive components.
3. Robust Construction and Rigidity: The Foundation of Stability
Precision cutting at extreme pressures demands an exceptionally stable platform. Vibration is the enemy of accuracy and edge quality. A truly high quality water jet features:
Heavy-Duty Machine Frame: Constructed from thick, stress-relieved steel or high-grade castings, the frame provides immense mass and rigidity to dampen vibrations generated by the cutting process and the pump. Lighter frames flex, causing chatter and dimensional inaccuracies.
Precision Guideways & Drives: High-accuracy, pre-loaded linear motion systems (like box ways or heavy-duty linear guides) and robust rack-and-pinion or precision ball screw drives ensure smooth, frictionless, and backlash-free motion under heavy cutting loads. This stability is fundamental for achieving the micron-level precision expected from a high quality water jet.
Durable Cutting Table: Designed to withstand the impact of the jet, high-pressure water, and abrasive slurry without warping or excessive wear. Slat or grid designs using hardened materials ensure longevity and easy debris removal.
Effective Water Management: A sophisticated tank system for catching the spent water and abrasive slurry, equipped with efficient separation systems (like drag conveyors or screw classifiers) to remove sludge and allow water recirculation or clean disposal, is essential for environmental compliance and operational cleanliness.
4. Advanced Control Software and Automation: Intelligence Meets Power
The brains behind the brawn. The software controlling a high quality water jet is sophisticated, intuitive, and packed with features that optimize performance, streamline operation, and maximize efficiency.
Powerful CAD/CAM Integration: Seamless import of complex 2D and 3D CAD models (DXF, DWG, STEP, IGES, etc.). Advanced CAM software automatically generates efficient, optimized cutting paths, including lead-ins/outs, piercing strategies, cut sequencing, and nesting to minimize material waste.
Intelligent Piercing: High-pressure piercing can damage material surfaces. Advanced software offers specialized piercing routines (soft pierce, shallow pierce, plunge pierce) to minimize top-side splashback and damage, especially critical for delicate materials or finished surfaces.
Cutting Process Optimization: Software that dynamically adjusts cutting speed based on material type, thickness, and desired edge quality. It manages abrasive feed rate synchronization with pump pressure and traverse speed for optimal results.
Taper Compensation: Sophisticated algorithms automatically adjust the cutting path to compensate for inherent jet taper, resulting in parts with near-perpendicular edges without manual intervention.
User-Friendly Interface: Intuitive controls, clear visualizations, simulation capabilities, and comprehensive diagnostics make operation efficient and reduce the potential for errors. Remote monitoring capabilities are increasingly common in high quality water jet systems.
Automation Compatibility: Designed for integration with material handling systems (load/unload robots, conveyors) and factory networks (Industry 4.0), enabling lights-out manufacturing and maximizing throughput.
5. Reliability, Support, and Total Cost of Ownership (TCO): The Long-Term Value Proposition
Investing in a high quality water jet is an investment in long-term productivity and lower overall operating costs. The initial price tag is just one factor; the Total Cost of Ownership (TCO) is where superior systems truly prove their worth.
Proven Reliability & Durability: Built with premium components and rigorous manufacturing standards, high-end water jets are engineered for years of dependable service in demanding production environments. This minimizes unplanned downtime, a major cost driver.
Reduced Maintenance & Consumable Costs: While consumables (orifices, mixing tubes, seals) are inherent to the process, a high quality water jet:
Uses longer-lasting consumables (e.g., diamond orifices, carbide tubes).
Causes less wear due to system stability and optimized cutting parameters.
Is designed for easier access and faster maintenance, reducing labor costs.
Higher Productivity: Faster cutting speeds (achieved through higher pressure and optimized technology), faster positioning speeds, reduced setup times, and minimized need for secondary finishing directly translate to more parts produced per hour and lower labor costs per part.
Minimized Material Waste: Superior precision and advanced nesting capabilities within the software ensure optimal material utilization, reducing scrap costs significantly, especially when working with expensive metals or composites.
Exceptional Technical Support & Service: Reputable manufacturers of high quality water jet systems provide comprehensive support: expert installation, thorough operator training, readily available spare parts, responsive field service technicians, and knowledgeable application engineers. This support network is invaluable for maximizing uptime and resolving issues quickly.
Warranty: Strong warranty terms reflect the manufacturer’s confidence in their product’s durability and provide peace of mind.
Choosing a high quality water jet system is not merely a purchase; it’s a strategic decision that impacts the core capabilities of a manufacturing operation. By focusing on the five critical aspects – unparalleled precision driven by advanced motion control and DHTC, cutting-edge technology embodied in the pump and cutting head, rock-solid construction for unwavering stability, intelligent software enabling optimization and automation, and the long-term value derived from reliability and lower TCO – businesses invest in a tool that delivers consistent, superior results.
The benefits are tangible: faster production times, reduced material waste, elimination of secondary finishing steps, the ability to cut virtually any material with precision, and the confidence that comes from reliable, continuous operation. In a competitive landscape where precision, efficiency, and versatility are paramount, a high quality water jet is far more than a cutting machine; it’s a fundamental enabler of innovation and manufacturing excellence. Investing in true quality upfront pays substantial dividends throughout the system’s operational life.
continue reading