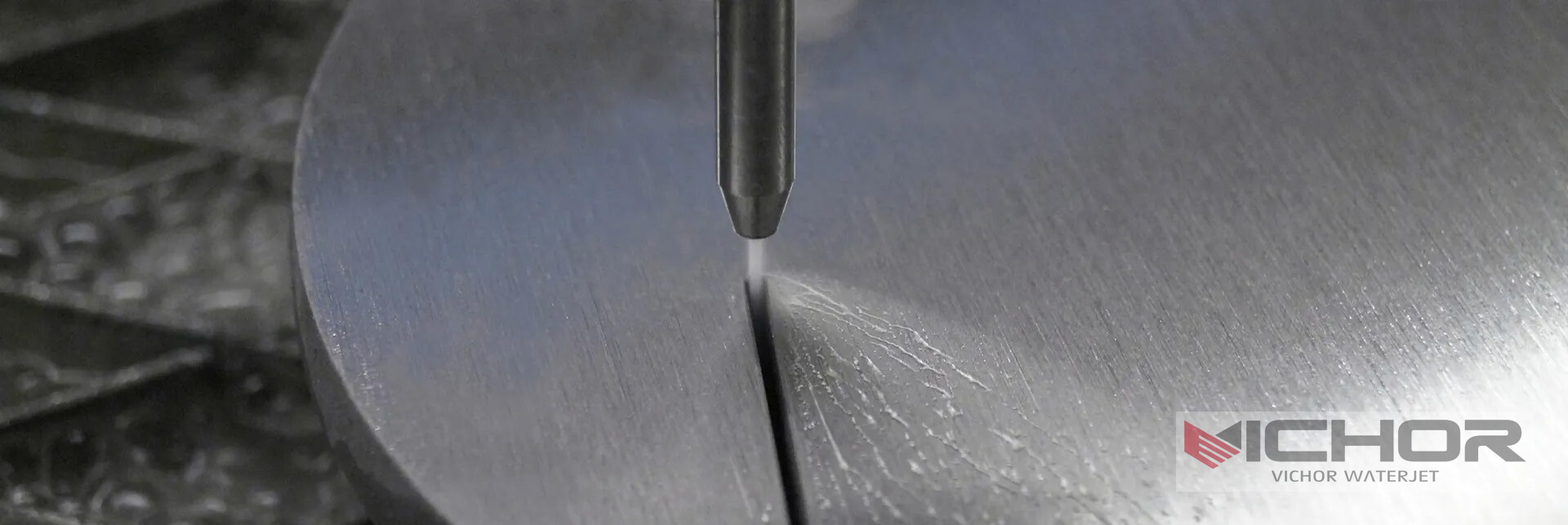
Laminated glass, the safety champion of the glazing world, is ubiquitous in modern architecture, automotive windshields, and security applications. Its unique construction – typically two or more glass sheets bonded by a resilient interlayer like PVB (Polyvinyl Butyral) or SGP (SentryGlas Plus) – makes it incredibly strong and shatter-resistant. However, this very strength and composition pose significant challenges when it comes to cutting, especially for complex shapes or post-production modifications. Traditional mechanical methods often struggle, leading to chipping, delamination, or heat damage. This is where the revolutionary technology of cutting laminated glass with water jet emerges as the superior solution. This comprehensive guide delves deep into why and how waterjet cutting has become the gold standard for processing this vital material.
1. Understanding the Waterjet Cutting Process for Laminated Glass
At its core, cutting laminated glass with water jet utilizes an incredibly focused, high-velocity stream of water. For laminated glass, an abrasive material – usually garnet sand – is introduced into this pure water stream. This transforms it into an abrasive waterjet, a potent cutting tool capable of slicing through virtually any material, including the tough combination of glass and polymer interlayers.
The Mechanics: Ultra-high-pressure pumps (typically generating 60,000 to 90,000 PSI) force water through a tiny diamond or sapphire orifice, creating a supersonic pure water jet.
Abrasive Introduction: This pure water stream then enters a mixing chamber where abrasive garnet particles are drawn in via the Venturi effect. The abrasive particles are violently accelerated by the water stream within a focusing tube (nozzle).
The Cut: The resulting abrasive-laden jet exits the nozzle at speeds exceeding Mach 3. It impacts the laminated glass surface with immense kinetic energy, creating a micro-erosion effect. This erosion action cleanly shears through both the glass layers and the interlayer simultaneously, particle by particle, along a precisely controlled path dictated by CNC (Computer Numerical Control) software. The kerf (cut width) is typically small, ranging from 0.8mm to 1.5mm depending on the nozzle size and material thickness.
Cutting laminated glass with water jet is fundamentally a cold-cutting process. There is no significant heat generated at the cut line, which is crucial for preventing thermal stress, cracking, or degradation of the sensitive PVB/SGP interlayer – a major limitation of laser cutting.
2. Why Waterjet Excels at Cutting Laminated Glass: Overcoming Traditional Challenges
Traditional methods like scoring and snapping, sawing, or grinding often fall short when cutting laminated glass:
Delamination Risk: Mechanical stress from scoring/snapping or sawing can cause the glass layers to separate from the interlayer, especially near cut edges or complex curves, compromising structural integrity and safety.
Chipping and Cracking: Glass is brittle. Mechanical tools can easily cause chipping on the top, bottom, or edge surfaces, leading to weak points and aesthetic flaws. Internal stresses can also trigger uncontrolled cracking.
Heat Sensitivity: PVB and SGP interlayers are thermoplastic. Methods generating heat (like lasers or high-speed saws without coolant) can melt, bubble, char, or weaken the interlayer bond, creating hazy lines, structural weaknesses, or even fire hazards in extreme cases.
Complexity Limitations: Cutting intricate internal shapes (holes, curves, notches) or tight radii is extremely difficult, if not impossible, with standard mechanical tools without significant risk of breakage.
Material Waste: Inaccurate cuts or breakage during traditional processing lead to higher material waste.
Cutting laminated glass with water jet directly addresses these challenges:
Minimal Mechanical Stress: The abrasive jet applies localized, focused force without inducing widespread stress across the panel, drastically reducing the risk of uncontrolled cracking or delamination.
Cold Cutting: Zero heat-affected zone (HAZ) ensures the interlayer remains completely unaffected – no melting, bubbling, or weakening. The glass itself isn’t thermally stressed.
No Chipping: The micro-erosion process produces exceptionally clean, chip-free edges on both the top and bottom surfaces of the glass.
Unmatched Complexity: CNC precision allows for cutting virtually any 2D shape with extreme accuracy and repeatability, including tight curves, sharp corners, and intricate internal cutouts that are impossible with other methods.
Reduced Waste: High precision and predictable results minimize material waste, especially valuable for expensive laminated or specialty glass types.
3. Key Advantages of Waterjet Cutting for Laminated Glass Applications
Choosing cutting laminated glass with water jet offers a multitude of benefits beyond simply overcoming traditional limitations:
Exceptional Edge Quality: The resulting cut edge is smooth, clean, and typically requires minimal post-processing (often just cleaning). While not optically perfect like a polished edge, it’s far superior to mechanically cut or snapped edges and is suitable for many applications where the edge might be encapsulated or framed.
Material Versatility: A single waterjet setup can cut laminated glass of varying thicknesses (from thin automotive glass to thick ballistic panels) and types (annealed, heat-strengthened, tempered – though note: tempered glass must be cut before tempering). It can also easily cut through combinations of glass and other materials in a single pass.
High Precision and Accuracy: Modern CNC waterjets offer remarkable precision (tolerances down to +/- 0.1mm or better are achievable), ensuring parts fit perfectly and designs are replicated flawlessly. This is critical for architectural fittings and complex assemblies.
Design Freedom: Unleash creativity. Waterjets enable complex geometries, decorative patterns, custom openings, logos, and artistic designs integrated directly into the laminated glass panel.
No Tooling Changes: Switching between different cutting tasks or shapes requires only a software file change, not physical tool changes. This significantly reduces setup time and increases flexibility for short runs or custom one-offs.
Environmentally Friendlier: The process generates no hazardous fumes or dust (like some dry cutting methods). Used abrasive garnet is inert and can often be recycled or safely landfilled. Water used is typically filtered and recycled within the system.
Consistency and Repeatability: Once programmed, CNC waterjets produce identical parts repeatedly, ensuring consistent quality across large projects.
4. Diverse Applications Enabled by Waterjet Cutting Laminated Glass
The unique capabilities of cutting laminated glass with water jet have opened doors across numerous industries:
Architecture & Construction:
Custom-shaped windows and skylights (rounds, ovals, complex polygons).
Decorative interior partitions, balustrades, and railings with intricate patterns.
Precise cutouts for hardware (hinges, handles, vents) in doors and facades.
Unique shower enclosures and bath screens.
Complex facades and curtain walls requiring bespoke panels.
Automotive & Transportation:
Prototyping and production of complex windshield shapes.
Cutting openings for sensors, antennas, or HUD (Heads-Up Display) components in windshields.
Manufacturing side and rear windows with specific cutouts.
Cutting laminated glass for train windows, aircraft windows, and marine applications.
Security & Safety Glass:
Precise cutting of thick, multi-layered ballistic and blast-resistant laminated panels for banks, embassies, and vehicles.
Cutting laminated glass for display cases, museum exhibits, and jewelry counters requiring high security.
Furniture & Interior Design:
Creating custom tabletops, shelves, and cabinet inserts with unique shapes and internal designs.
Decorative glass panels for doors, wall art, and room dividers.
Specialty Applications:
Aquariums and zoo exhibits requiring large, curved, or uniquely shaped laminated viewing panels.
Cutting laminated glass for solar panels or specialized optical applications.
Prototyping new laminated glass products and components.
5. Critical Considerations for Waterjet Cutting Laminated Glass Successfully
While incredibly effective, optimal results when cutting laminated glass with water jet depend on several factors:
Machine Calibration and Maintenance: Precise nozzle alignment (water orifice, mixing tube), consistent abrasive feed, and optimal water pressure are paramount for cut quality and accuracy. Regular maintenance is crucial.
Abrasive Selection and Flow Rate: High-quality, consistently sized garnet abrasive is essential. The flow rate must be optimized – too little abrasive leads to incomplete cuts and slow speeds; too much is wasteful and can widen the kerf unnecessarily.
Cutting Speed and Quality Settings: Finding the right balance between cutting speed and desired edge finish is key. Slower speeds generally yield smoother edges but increase production time. Traverse rates and pierce parameters need careful tuning for laminated glass.
Material Support: Proper support under the glass is vital to prevent vibration (which causes edge waviness) and breakout at the bottom of the cut. Specialized slatted tables or custom fixtures are used. Vacuum tables can help hold thinner sheets flat.
Piercing Technique: Starting a cut (piercing) within the material requires specific techniques to avoid excessive splashback or potential damage to the top surface. Piercing at reduced pressure or using specialized lead-in paths is common.
Interlayer Type: Standard PVB cuts very cleanly. Stiffer interlayers like SGP might require slight adjustments to feed rates or abrasive flow but are still readily cut. EVA (Ethylene-Vinyl Acetate) used in some decorative laminates also cuts well.
Edge Finishing: While waterjet edges are clean, they are typically satin-finished. If a polished edge is required for aesthetic or functional reasons (e.g., exposed edges in frameless glass), secondary polishing operations will be necessary.
Operator Expertise: Understanding the nuances of waterjet cutting parameters and material behavior is essential for achieving consistent, high-quality results, especially with expensive laminated glass panels.
Cutting laminated glass with water jet has revolutionized how this essential safety material is processed. By harnessing the power of ultra-high-pressure water and abrasive garnet, this cold-cutting technology overcomes the inherent limitations and risks associated with traditional mechanical methods. It delivers unparalleled precision, eliminates heat damage and delamination, enables breathtaking design complexity, and produces clean, chip-free edges. From intricate architectural masterpieces and complex automotive components to critical security glazing and bespoke interior design elements, waterjet cutting unlocks the full potential of laminated glass. As the demand for safer, stronger, and more aesthetically versatile glass solutions continues to grow across industries, waterjet technology stands as the indispensable, precise, and reliable partner for shaping the future of laminated glass fabrication. For any project demanding accuracy, complexity, and the highest quality finish on laminated glass, waterjet cutting is unequivocally the superior choice.
continue reading